Таблицы моментов затяжки болтов динамометрическим ключом
Момент затяжки – это усилие, которое прикладывается к резьбовому соединению при его завинчивании. Если закрутить крепеж с меньшим усилием, чем это необходимо, то, под воздействием вибраций, резьбовое соединение может раскрутиться, не обеспечивая нужную герметичность между скрепляемыми деталями, что может привести к тяжелым последствиям. Наоборот, если приложить к метизу большее усилие, чем требуется, произойдет разрушение резьбового соединения или скрепляемых деталей, например, может произойти срыв резьбы или появление трещин в деталях.
Для каждого размера и класса прочности резьбового соединения указаны определенные моменты затяжки. Все значения занесены в специальную таблицу усилий для затяжки динамометрическим ключом. Обычно, класс прочности болта указывается на его головке.
Классы прочности для метрических болтов
Класс прочности указывается цифрами на головке.
Классы прочности для дюймовых болтов
Информация о прочности выполнена в виде насечек на головке.
Резьбовые соединения затягивают стрелочным, предельным или цифровым динамометрическим ключом.
Таблица усилий затяжки метрических болтов
Усилие указано в Ньютон-метрах.
Таблица усилий затяжки дюймовых болтов
SAE |
1 или 2 |
5 |
6 или 7 |
8 |
||||||||
Размер |
Усилие |
Усилие |
Усилие |
Усилие |
||||||||
(дюймы)-(резьба) |
Ft-Lb |
Кг/м |
Н/м |
Ft-Lb |
Кг/м |
Н/м 13.5582 |
Ft-Lb |
Кг/м |
Н/м |
Ft-Lb |
Кг/м |
Н/м |
5/16 — 18 |
11 |
1. |
14.9140 17.6256 |
17 |
2.3511 |
23.0489 |
19 |
2.6277 |
25.7605 |
24 |
3.3192 |
32.5396 |
3/8 — 16 |
18 |
2. 2.7660 |
24.4047 |
31 |
4.2873 |
42.0304 |
34 |
4.7022 |
46.0978 |
44 |
6.0852 |
59.6560 |
7/16 — 14 |
28 |
3. |
37.9629 |
49 |
6.7767 |
66.4351 |
55 |
7.6065 |
74.5700 |
70 |
9.6810 |
94.9073 |
1/2 — 13 |
39 |
5. |
52.8769 |
75 |
10.3785 |
101.6863 |
85 |
11.7555 |
115.2445 |
105 120 |
14.5215 |
|
9/16 — 12 |
51 |
7. |
69.1467 |
110 |
15.2130 |
149.1380 |
|
16.5960 |
162.6960 |
155 |
21.4365 |
210.1490 |
5/8 — 11 |
83 |
11. |
112.5329 |
150 |
20.7450 |
203.3700 |
167 |
23.0961 |
226.4186 |
210 |
29.0430 |
284.7180 |
3/4 — 10 |
105 |
14. |
142.3609 |
270 |
37.3410 |
366.0660 |
280 |
38.7240 |
379.6240 |
375 |
51.8625 |
508.4250 |
7/8 — 9 |
160 |
22. |
216.9280 |
395 |
54.6285 |
535.5410 |
440 |
60.8520 |
596.5520 |
605 |
83.6715 |
820.2590 |
1 — 8 |
236 |
32. |
318.6130 |
590 |
81.5970 |
799.9220 |
660 |
91.2780 |
894.8280 |
910 |
125.8530 |
1233.7780 |
Для закручивания резьбовых соединений в соответствии с данными таблиц необходимо использовать специальный инструмент — динамометрический ключ.
Ниже представлены популярные модели ключей, диапазоны которых перекрывают большинство значений определенных моментов затяжки. Максимальную точность передачи крутящего момента обеспечивают электронные динамометрические ключи.
Таблицы моментов затяжки колес
Примерные значения для легковых автомобилей
Для легковых автомобилей используют ключи с присоединительным квадратом 1/2. Самыми популярными ключами являются модели с затяжкой до 200-210 Нм, например, ключи с диапазоном 28-210 или 42-210. Ниже представлены варианты подобных ключей.
Примерные значения для грузовых автомобилей и автобусов
Для коммерческого транспорта используют ключи с присоединительным квадратом 1/2, 3/4 и даже 1 дюйм. Ниже представлены варианты ключей для автобусов, коммерческих и грузовых автомобилей.
Порядок затяжки
Компания AIST располагает широким ассортиментом профессиональных ключей для выполнения различных работ с резьбовыми соединениями. У нас всегда возможно подобрать необходимый динамометрический ключ для автомобиля, как для легкового, так и для грузового транспортного средства.
*Значения таблиц моментов затяжки носят информационный характер, без ссылки на какой-либо ГОСТ.
Полезные статьи:
Таблицы моментов затяжки болтов динамометрическим ключом.
Для того, чтобы правильно установить колеса, необходимо при помощи динамометрического ключа равномерно ослабить колесные болты и гайки до рекомендованного момента затяжки. Каждый автопроизводитель устанавливает собственное усилие затяжки колесных болтов,измеряемое в Ньютон-метрах (НМ).
Момент затяжки – это усилие, которое прикладывается к резьбовому соединению при его завинчивании. Если закрутить крепеж с меньшим усилием, чем это необходимо, то, под воздействием вибраций, резьбовое соединение может раскрутиться, не обеспечивая нужную герметичность между скрепляемыми деталями, что может привести к тяжелым последствиям. Наоборот, если приложить к метизу большее усилие, чем требуется, произойдет разрушение резьбового соединения или скрепляемых деталей, например, может произойти срыв резьбы или появление трещин в деталях.
Для каждого размера и класса прочности резьбового соединения указаны определенные моменты затяжки. Все значения занесены в специальную таблицу усилий для затяжки динамометрическим ключом. Обычно, класс прочности болта указывается на его головке.
Классы прочности для метрических болтов
Класс прочности указывается цифрами на головке.
Классы прочности для дюймовых болтов
Информация о прочности выполнена в виде насечек на головке.
Таблица усилий затяжки метрических болтов
Усилие указано в Ньютон-метрах.
Нажмите на изображение чтобы увеличить
Таблица усилий затяжки дюймовых болтов
SAE | 1 или 2 | 5 | 6 или 7 | 8 | ||||||||
Размер | Усилие | Усилие | Усилие | Усилие | ||||||||
(дюймы)-(резьба) | Ft-Lb | Кг/м | Н/м | Ft-Lb | Кг/м | Н/м | Ft-Lb | Кг/м | Н/м | Ft-Lb | Кг/м | Н/м |
5/16 — 18 | 11 | 1.5213 | 14.9140 | 17 | 2.3511 | 23.0489 | 19 | 2.6277 | 25.7605 | 24 | 3.3192 | 32.5396 |
3/8 — 16 | 18 | 2. | 24.4047 | 31 | 4.2873 | 42.0304 | 34 | 4.7022 | 46.0978 | 44 | 6.0852 | 59.6560 |
7/16 — 14 | 28 | 3.8132 | 37.9629 | 49 | 6.7767 | 66.4351 | 55 | 7.6065 | 74.5700 | 70 | 9.6810 | 94.9073 |
1/2 — 13 | 39 | 5. | 52.8769 | 75 | 10.3785 | 101.6863 | 85 | 11.7555 | 115.2445 | 105 | 14.5215 |
|
9/16 — 12 | 51 | 7.0533 | 69.1467 | 110 | 15.2130 | 149.1380 | 120 | 16.5960 | 162.6960 | 155 | 21.4365 | 210.1490 |
5/8 — 11 | 83 | 11. | 112.5329 | 150 | 20.7450 | 203.3700 | 167 | 23.0961 | 226.4186 | 210 | 29.0430 | 284.7180 |
3/4 — 10 | 105 | 14.5215 | 142.3609 | 270 | 37.3410 | 366.0660 | 280 | 38.7240 | 379.6240 | 375 | 51.8625 | 508.4250 |
7/8 — 9 | 160 | 22. | 216.9280 | 395 | 54.6285 | 535.5410 | 440 | 60.8520 | 596.5520 | 605 | 83.6715 | 820.2590 |
1 — 8 | 236 | 32.5005 | 318.6130 | 590 | 81.5970 | 799.9220 | 660 | 91.2780 | 894.8280 | 910 | 125.8530 | 1233.7780 |
Для закручивания резьбовых соединений в соответствии с данными таблиц необходимо использовать специальный инструмент — динамометрический ключ.
Таблицы затяжек колесных гаек и болтов
Примерные значения для легковых автомобилей
Нажмите на изображение чтобы увеличить
Примерные значения для грузовых автомобилей и автобусов
Нажмите на изображение чтобы увеличить
Порядок затяжки
Часто автолюбители сталкиваются с такими ситуациями на различных гаражных автосервисах и шиномонтажах, которые открылись и не знают таких методов. Порядок затяжки колесных болтов важен на каждом автомобиле и его нарушение может привести к фатальным последствиям.
Данный материал носит исключительно информационный характер для автолюбителей, для СТО и автосервисов рекомендуем использовать типовой регламент в соответствии на мануалы по каждой марке и модели автомобиля.
Частичный источник: aist-tools. ru.
Читать подробно: О порядке затяжки колесных болтов или гаек.
Таблица усилия затяжки колесных болтов динамометрическим ключом » Центр обучения для специалистов с трудоустройством
В данной статье мы поговорим о вопросе который возникает у всех автолюбителей и шиномонтажников, как и с каким усилием затягивать болты или гайки на автомобиле. Для начала нужно понять что, сначала гайки или болты устанавливаются и подтягиваются на автомобиле с помощью гайковерта или колонного ключа и уже потом ведется финальная протяжка всех четырех колес.
Для надежной установки колеса на автомобиль, необходимо при помощи динамометрического ключа равномерно ослабить или протянуть колесные болты и гайки до рекомендованного момента затяжки. Все автопроизводители устанавливают собственное требования по усилию затяжки колесных болтов, это усилие измеряется в Ньютон-метрах (НМ). Момент затяжки колесных гаек или болтов автомобиля важно протягивать строго по таблице которая представлена ниже.
Производитель автомобиля | Модель | Момент затяжки (Нм) |
Alfa Romeo | Alfa 145/146/147 Alfa 156 Alfa 159 Alfa 166 Alfa Briera/Spider | 93+/-10 98 120 +/- 12 86 +/-8 120 +/- 12 |
Audi | A1/A2/A3/A4/A5/A6/A7/A8/TT Q5 Q7 | 120 140 160 |
BMW | 1 серия/3 серия/5 серия M5 Z3 X3,X5,X6 | 120 100 100+/-10 140 |
Chevrolet | Сruze Captiva Spark | 140 125 120 |
Chrysler | 300C 200C Grand Voyager | 150 120 135 |
Citroen | Xsara Picasso/Saxo C4/C5 Berlingo AX10/AX11/AX14/Sport | 85 80-100 85 90 |
Ford | KA/Mondeo/Scorpio/Puma Cougar Fiesta (2002-2008) Fiesta Fusion Probe Transit Connect | 85 128 90 110 110 90-120 90 |
Fiat | 500 Grande Punto/Punto Evo Ducato/Talento Ducato Maxi | 86 120 160 180 |
Hyundai | Все модели Starex | 110 130 |
Honda | Все модели | 108-110 |
Jeep | Cherokee Compass Patriot/Wrangler | 136 135 135 |
Jaguar | XKR S-Type XJ6 XJR/XJ12 XJ8/XJ-S | 125 128 65-85 88-102 66-82 |
KIA | Sorento/Picanto/ Rio/Shuma Carnival Margentis | 100 |
Как работать динамометрическим ключом
youtube.com/embed/Ur3Vw1_xrXE?start=3&feature=oembed» frameborder=»0″ allow=»accelerometer; autoplay; clipboard-write; encrypted-media; gyroscope; picture-in-picture» allowfullscreen=»»/>
Схема протяжки колесных болтов и гаек автомобиля
Таблица сила затяжки болтов
Таблицы усилий затяжки болтов динамометрическим ключом. Таблицы для динамометрического ключа
Момент затяжки – это усилие, которое прикладывается к резьбовому соединению при его завинчивании. Если закрутить крепеж с меньшим усилием, чем это необходимо, то, под воздействием вибраций, резьбовое соединение может раскрутиться, не обеспечивая нужную герметичность между скрепляемыми деталями, что может привести к тяжелым последствиям. Наоборот, если приложить к метизу большее усилие, чем требуется, произойдет разрушение резьбового соединения или скрепляемых деталей, например, может произойти срыв резьбы или появление трещин в деталях.
Для каждого размера и класса прочности резьбового соединения указаны определенные моменты затяжки. Все значения занесены в специальную таблицу усилий для затяжки динамометрическим ключом. Обычно, класс прочности болта указывается на его головке.
Классы прочности для метрических болтов
Класс прочности указывается цифрами на головке.
Классы прочности для дюймовых болтов
Информация о прочности выполнена в виде насечек на головке.
Таблица усилий затяжки метрических болтов
Усилие указано в Ньютон-метрах.
Таблица усилий затяжки дюймовых болтов
(дюймы)-(резьба) 1/4 — 20 — 28 | ||||||||||||
Таблицы затяжек колесных гаек и болтов
Примерные значения для легковых автомобилей
Примерные значения для грузовых автомобилей и автобусов
Порядок затяжки
Компания AIST располагает широким ассортиментом профессиональных ключей для выполнения различных работ с резьбовыми соединениями. У нас всегда возможно подобрать необходимый динамометрический ключ для автомобиля, как для легкового, так и для грузового транспортного средства.
Полезные статьи:
Таблица затяжки болтов динамометрическим ключом
instrument.guru > Оснастка > Таблица затяжки болтов динамометрическим ключом
Определенная степень закрутки резьбовых элементов выполняется с целью увеличения срока службы, прочности и повышению сопротивления различным влияющим факторам. Для каждого крепежного элемента есть определенная степень затяжки на каждом посадочном месте, рассчитывается она на основе нагрузок, температурных режимов и свойств материалов.
Вконтакте
Google+
Мой мир
Оглавление:
- Маркировка деталей
- Единицы измерения
- Моменты затяжки резьбовых соединений
- Моменты затяжки ленточных хомутов с червячным зажимом
- Как определить момент затяжки
Например, при воздействии температуры металлу свойственно расширяться, при условии влияния вибрации — крепеж получает дополнительную нагрузку, и чтобы минимизировать ее, закручивать нужно с правильным усилием. Рассмотрим силу затяжки болтов, таблицы, методы и инструменты для проведения работ
Маркировка деталей
Этот параметр указывается на головке болта. Для деталей, выполненных на основе углеродистой стали с классом прочности — 2, указываются цифры через точку, например: 3.5, 4.8 и т. д.
Первая цифра указывает 1/100 номинального размера прочностного предела на разрыв, измеряется в МПа. Например, если на головке болта, указано — 10.1, то первое число означает 10*100 = 1000 МПа.
Вторая цифра — отношение пределов текучести к прочности, умножается на 10, по вышеуказанному примеру — 1*10*10= 100 МПа.
Предел текучести — это максимальная нагрузка на болт. Для элементов, выполненных из нержавеющей стали, наносится тип стали А2 или А4, и далее предел прочности. Например: А4—40. Число в данной маркировке характеризует 1/10 предела прочности углеродистой стали.
Единицы измерения
Основной величиной является Паскаль, единица измерения давления, механического напряжения, согласно международной системе «СИ». Паскаль равняется давлению, вызванному силой в один ньютон, равномерно распределяющейся по плоской к ней поверхности с площадью в один квадратный метр.
Рассмотрим, как конвертируются единицы измерения:
- 1 Па = 1Н/м2.
- 1 МПа = 1 н/мм2.
- 1 н/мм2 = 10кгс/см2.
Моменты затяжки резьбовых соединений
Ниже приведена таблица затяжки болтов динамометрическим ключом.
Прочность болта, в Нм | |||
Размер резьбы | 8.8 | 10.9 | 12.9 |
М6 | 10 | 13 | 16 |
М8 | 25 | 33 | 40 |
М10 | 50 | 66 | 80 |
М12 | 85 | 110 | 140 |
М14 | 130 | 180 | 210 |
М16 | 200 | 280 | 330 |
М18 | 280 | 380 | 460 |
М20 | 400 | 540 | 650 |
Таблица усилия затяжки болтов для дюймовой резьбы стандарта США для крепежных деталей SAE класса 5 и выше.
Дюймы | Нм | фунт |
¼ | 12±3 | 9±2 |
5/16 | 25±6 | 18±4,5 |
3/8 | 47±9 | 35±7 |
7/16 | 70±15 | 50±11 |
½ | 105±20 | 75±15 |
9/16 | 160±30 | 120±20 |
5/8 | 215±40 | 160±30 |
¾ | 370±50 | 275±37 |
7/8 | 620±80 | 460±60 |
1 ньютон метр (Нм) равняется 0,1кГм.
ISO -Международный стандарт.
Моменты затяжки ленточных хомутов с червячным зажимом
В нижеуказанной таблицеприведены данные для первоначальной установки на новом шланге, а также для повторной затяжки уже обжатого шланга.
Размер хомута | Нм | фунт / дюйм |
16мм — 0,625 дюйма | 7,5±0,5 | 65±5 |
13,5мм — 0,531 дюйма | 4,5±0,5 | 40±5 |
8мм — 0,312 дюйма | 0,9±0,2 | 8±2 |
Момент затяжки для повторной стяжки | ||
16мм | 4,5±0,5 | 40±5 |
13,5мм | 3,0±0,5 | 25±5 |
8мм | 0,7±0,2 | 6±2 |
Как определить момент затяжки
- С помощью динамометрического ключа.
Этот инструмент должен быть подобран таким образом, чтобы момент затяжки крепежного элемента был на 20−30% меньше, чем максимальный момент на вашем ключе. При попытке превысить предел, ключ быстро выйдет из строя.
Усилие на затяжку и тип стали указывается на каждом болте, как расшифровывать маркировку описывалось выше. Для вторичной протяжки болтов нужно учитывать несколько правил:
- Всегда знать точное необходимое усилие для затяжки.
- При контрольной проверке затяжки стоит выставить усилие и проверить в круговом порядке все крепежные элементы.
- Запрещено использовать динамометрический ключ как обычный, им нельзя производить закрутку деталей, гайку или закручивать болт до примерного усилия, контрольная протяжка производится динамометрическим ключом.
- Динамометрический ключ должен быть с запасом.
- Без динамометрического ключа.
Для этого потребуется:
- Ключ накидной или рожковый.
- Пружинный кантер или весы, с пределом в 30 кг.
- Таблица, в которой указывается усилие затяжки болтов и момент затяжки гаек.
Момент затяжки — это усилие, приложенное на рычаг размерами в 1 метр. Например, нам требуется затянуть гайку с усилием 2 кГс/м:
- Измеряем длину нашего накидного ключа, она, к примеру, составила 0,20 метра.
- Делим 1 на 0,20 получаем цифру 5.
- Умножаем полученные результаты, 5 на 2кГс/м и получаем в итоге 10 кг.
Переходя к практике, берем наш ключ и весы, прикрепляем крючок к ключу и производим затяжку до нужного веса, согласно описанного выше расчета. Но даже такой способ в итоге окажется лучше, чем тянуть от «руки — на глаз», с погрешностью, чем выше усилие, тем она меньше. Это будет зависеть от качества весов, но лучше все-таки приобрести специальный ключ.
Вконтакте
Google+
Мой мир
Затяжка болтов динамометрическим ключом: таблицы, способы определения усилий
Чтобы увеличить прочность и срок эксплуатации резьбовых соединений, а также повысить их сопротивление различным внешним факторам необходимо правильно закрутить крепежные элементы, рассчитав усилие завинчивания. Каждое соединение имеет свою определенную степень затяжки в зависимости от посадочного места. Момент затяжки рассчитывается в зависимости от температурного режима, свойства материала и нагрузки, которая будет оказываться на резьбовое соединение.
К примеру, под воздействием температурных показателей металл начинает расширяться, а под воздействием вибрации на элемент оказывается дополнительная нагрузка. Соответственно, для минимизации воздействующих факторов, болты необходимо закручивать с расчетом правильного усилия. Предлагаем ознакомиться с таблицей силы затяжки болтов, а также методами и инструментами выполнения работ.
Что такое затяжное усилие и как его узнать?
Моментом затяжки называют показатель усилия, который необходимо приложить для резьбовых соединений в процессе их завинчивания. Если крепеж был закручен с прикладыванием небольшого усилия, чем это было нужно, то при воздействии различных механических факторов резьбовое соединение может не выдержать, теряется герметичность скрепленных деталей, что влечет за собой тяжелые последствия. Так же и при чрезмерном усилии, резьбовое соединение или скрепляемые детали могут попросту разрушиться, что приведет к срыву резьбы или появлению трещин в конструкционных элементах.
Каждый размер и класс прочности резьбовых соединений имеет определенный момент затяжки при работе с динамометрическим ключом, который указывается в специальной таблице. При этом обозначение класса прочности изделия располагается на его головке.
Маркировка и класс прочности деталей
Цифровое обозначение параметра прочности метрического болта указано на головке, и представлено в виде двух цифр через точку, к примеру: 4.6, 5.8 и так далее.
- Цифра до точки обозначает номинальный размер прочности предельного разрыва, рассчитывается как 1/100, и ее измерение осуществляется в МПа. К примеру, если на изделии указана маркировка — 9.2, то значение первого числа будет составлять 9*100=900 МПа.
- Цифра после точки является предельной текучестью по отношению к прочности, после расчета число необходимо умножить на 10, как указано в примере: 1*8*10=80 МПа.
Предельная текучесть представляет собой максимальную нагрузку на конструкцию болта. Элементы, которые выполняются из нержавеющих видов стали, имеют обозначение непосредственно самого вида стали (А2, А4), и только после этого указывается предельная прочность.
К примеру, А2-50. Значение в подобной маркировке обозначает 1/10 прочностного предела углеродистой стали. При этом, изделия, для изготовления которых используется углеродистая сталь, имеют класс прочности – 2.
Обозначение прочности для дюймовых болтов отмечается насечками на его головке.
Обозначение класса прочности дюймовых болтовВ чем измеряется затяжное усилие?
Основная величина измерения усилия затяжки болтов – Паскаль (Па). Международная система «СИ» предполагает, что данной единицей измеряется как давление, так и механическое напряжение. Соответственно, Паскаль равен значению давления, которое вызывается силой равной одному Ньютону и равномерным образом распределяется на плоскости размером в 1 м2.
Чтобы понять как можно конвертировать одну единицу измерения в другую, посмотрим пример:
- 1 Паскаль = 1 Нютону/м2;
- 1 МПаскаль = 1 Ньютону/мм2;
- 1 Ньютон/мм2 = 10 кгс/см2.
Значения усилий затяжки для различных типов болтов (таблица)
Для более удобного и точного восприятия представлена таблица затяжки болтов динамометрическим ключом.
Резьба | Класс прочности, Нм | Головка, мм | |||||||
3.6 | 4.6 | 5.8 | 6.8 | 8.8 | 9.8 | 10.9 | 12.9 | ||
М5 | 1.71 | 2.28 | 3.8 | 4.56 | 6.09 | 6.85 | 8.56 | 10.3 | 8 |
М6 | 2.94 | 3.92 | 6.54 | 7.85 | 10.5 | 11.8 | 14.7 | 17.7 | 10 |
М8 | 7.11 | 9.48 | 15.8 | 19 | 25.3 | 28.4 | 35.5 | 42.![]() | 13 |
М10 | 14.3 | 19.1 | 31.8 | 38.1 | 50.8 | 57.2 | 71.5 | 85.8 | 17 |
М12 | 24.4 | 32.6 | 54.3 | 65.1 | 86.9 | 97.7 | 122 | 147 | 19 |
М14 | 39 | 52 | 86.6 | 104 | 139 | 156 | 195 | 234 | 22 |
М16 | 59.9 | 79.9 | 133 | 160 | 213 | 240 | 299 | 359 | 24 |
М18 | 82.5 | 110 | 183 | 220 | 293 | 330 | 413 | 495 | 27 |
М20 | 117 | 156 | 260 | 312 | 416 | 468 | 585 | 702 | 30 |
М22 | 158 | 211 | 352 | 422 | 563 | 634 | 792 | 950 | 32 |
М24 | 202 | 270 | 449 | 539 | 719 | 809 | 1011 | 1213 | 36 |
Также представим таблицу момента затяжки для дюймовых видов резьб по стандарту, который применяется в Соединенных Штатах.
Дюймы | Нм | Фунт |
1/4 | 12±3 | 9±2 |
5/16 | 25±6 | 18±4.5 |
3/8 | 47±9 | 35±7 |
7/16 | 70±15 | 50±11 |
1/2 | 105±20 | 75±15 |
9/16 | 160±30 | 120±20 |
5/8 | 215±40 | 160±30 |
3/4 | 370±50 | 275±37 |
7/8 | 620±80 | 460±60 |
Значения усилий затяжки для ленточного хомута с червячным зажимом
Ниже приведенная таблица содержит ряд данных про первоначальную установку ленточных хомутов на новом шланге, а также про повторную затяжку уже обжатых шлангов.
Размер хомута | Нм | Фунт/Дюйм |
16мм — 0,625 дюйма | 7,5±0,5 | 65±5 |
13,5мм — 0,531 дюйма | 4,5±0,5 | 40±5 |
8мм — 0,312 дюйма | 0,9±0,2 | 8±2 |
Усилие затяжки для повторных стяжек | ||
16мм | 4,5±0,5 | 40±5 |
13,5мм | 3,0±0,5 | 25±5 |
8мм | 0,7±0,2 | 6±2 |
Определение момента затяжки
Динамометрическим ключом
Подбор этого инструмента должен осуществляться так, чтобы затяжной момент на крепежном элементе был на 20-30% меньше, нежели значение максимального момента на используемом ключе. Если попытаться превысить допустимый лимит, то инструмент может легко сломаться.
Затяжное усилие и марка материала должны присутствовать на каждом изделии, способы расшифровки маркировки описаны выше.
Чтобы выполнить вторичную протяжку болтов, следует придерживаться следующих рекомендаций:
- Точно знать значение необходимого затяжного усилия.
- Выполняя контрольную проверку затяжки, необходимо выставлять усилие и проверять по кругу каждый крепежный элемент.
- Запрещается пользоваться динамометрическим ключом как обычным, его не стоит использовать для закрутки деталей, гаек и болтов, чтобы получить лишь примерное усилие. Его стоит использовать для выполнения контрольной протяжки.
- У динамометрического ключа должен быть запас для измерения момента усилия.
Без использования динамометрического ключа
Чтобы выполнить проверку нам понадобится наличие:
- накидного или рожкового ключа;
- пружинного кантера или весов, с пределом не менее 30 кг;
- таблицы, которая содержит сведения об усилии затяжки болтов и гаек.
Момент затяжки является усилием, которое необходимо приложить на рычаг размером в 1 метр. К примеру, требуется выполнить затяжку гайки рассчитав для этого усилие в 2 кГс/м:
- Нам потребуется узнать какой длины ключ. Например, длина составляет 20 см или 0,2 метра.
- Разделить единицу на наше полученное значение: 1/0,2 = 5.
- Умножить полученный результат: 5*2кГс/м = 10 кг.
Далее на практическом опыте крепим к ключу крючок и присоединяем его к весам. Выполняем натяжку к нужному значению (которое мы получили в ходе расчетов) и начинаем постепенно закручивать/проверять. Применение такого кустарного метода все же лучше, нежели закручивать болты на «глаз». Погрешность будет присутствовать в любом случае, однако с увеличением усилия она будет уменьшаться. Все зависит от того, какого качества весы. Однако для проведения серьезных и профессиональных работ лучше обзавестись специальным динамометрическим ключом.
com/embed/TJ4EGMYNIv4?autohide=2&autoplay=0&mute=0&controls=1&fs=1&loop=0&modestbranding=0&playlist=&rel=1&showinfo=1&theme=dark&wmode=&playsinline=0″/> Подписывайтесь на наш канал в Яндекс.Дзен. Каждый день свежая и полезная информация. Подписаться Оцените статью! Загрузка…Усилие затяжки болта
Момент затяжки болтов – это сила, которая прикладывается к гайке при навинчивании ее на резьбовой стержень болта. Очень важно правильно ее рассчитать. Если она будет слишком маленькая, то воздействие нагрузок приведет к отвинчиванию гайки. При сильной затяжке произойдет разрушение метиза и, соответственно, всей конструкции.
В наше время значения крутящих моментов для резьбовых сталей рассчитаны и занесены в различные справочники. Чтобы облегчить ваши поиски, ниже приведены таблицы со справочными значениями крутящего момента и предварительных усилий затяжки для высокопрочных болтов с нормальным (крупным) и мелким шагами резьбы.
Существует два метода затяжки болтов:
1. Неконтролируемый – при данном методе используется оборудование или операции, при которых усилия, приложенные к крепежу не могут быть измерены. Нагрузка, действующая на крепление, обеспечивается с помощью молотка и гаечного ключа.
2. Контролируемый метод затяжки – он обеспечивается с помощью использования калиброванного и / или измеряемого оборудования, соблюдения предписанных операций. Данный метод может осуществляться двумя способами:
- Затяжка с помощью динамометрического инструмента – нагрузка на крепежную пару достигается с помощью контролируемого использования инструмента.
- Натяжение болта – необходимая нагрузка на крепежные элементы достигается путем натяжения болта в осевом направлении с использованием специальных инструментов.
Контролируемый метод затяжки имеет ряд преимуществ перед неконтролируемым:
1) Точная нагрузка на крепеж – использование инструментов позволить применить более значительные усилия не опасаясь разрушения крепежа.
2) Равномерность нагрузки – равномерность действия сил очень важна для узлов, в которых применяются уплотнительные прокладки, поскольку для них необходимо равномерное сжатие.
3) Безопасность работы – использование инструментов позволяет уменьшить риск травм, так как работники должны иметь соответствующую подготовку, перед работой с оборудованием.
4) Повышение производительности – время выполнения затяжки с помощью инструмента намного меньше, чем вручную, соответственно, снижается утомляемость рабочих и повышается производительность.
5) Достижение нужного результата с первого раза.
Все приведенные выше параметры предназначены для новых соединений. Необходимо помнить, что ранее использованные крепежи при повторной затяжке будут создавать дополнительное «паразитное» трение. Даже если гайковерт покажет нужный момент затяжки, не будет достигнуто требуемое сжатие и, как следствие, при эксплуатации повысится риск разрушения или самоослабления соединения, что может привести к аварии.
Момент затяжки колесных болтов (таблица). Какая сила и момент затяжки должна быть для гаек колес автомобиля?
Для того, чтобы правильно установить колеса, необходимо при помощи динамометрического ключа равномерно ослабить колесные болты и гайки до рекомендованного момента затяжки. Каждый автопроизводитель устанавливает собственное усилие затяжки колесных болтов, измеряемое в Ньютон-метрах (НМ). Момент затяжки колесных болтов автомобиля можно узнать из нижеприведенной таблицы.
Момент затяжки колесных болтов – таблица:
Производитель автомобиля |
Модель |
Момент затяжки (Нм) |
Alfa Romeo |
Alfa 145/146/147 Alfa 156 Alfa 159 Alfa 166 Alfa Briera/Spider |
93+/-10 98 120 +/- 12 86 +/-8 120 +/- 12 |
Audi |
A1/A2/A3/A4/A5/A6/A7/A8/TT Q5 Q7 |
120 140 160 |
BMW |
1 серия/3 серия/5 серия M5 Z3 X3,X5,X6 |
120 100 100+/-10 140 |
Chevrolet |
Сruze Captiva Spark |
140 125 120 |
Chrysler |
300C 200C Grand Voyager |
150 120 135 |
Citroen |
Xsara Picasso/Saxo C4/C5 Berlingo AX10/AX11/AX14/Sport |
85 80-100 85 90 |
Ford |
KA/Mondeo/Scorpio/Puma Cougar Fiesta (2002-2008) Fiesta Fusion Probe Transit Connect |
85 128 90 110 110 90-120 90 |
Fiat |
500 Grande Punto/Punto Evo Ducato/Talento Ducato Maxi |
86 120 160 180 |
Hyundai |
Все модели Starex |
110 130 |
Honda |
Все модели |
108-110 |
Jeep |
Cherokee Compass Patriot/Wrangler |
136 135 135 |
Jaguar |
XKR S-Type XJ6 XJR/XJ12 XJ8/XJ-S |
125 128 65-85 88-102 66-82 |
KIA |
Sorento/Picanto/ Rio/Shuma Carnival Margentis |
100 103 100 98 |
LADA |
Samara/Riva Niva |
70-78 88-91 |
Land Rover |
Freelander 2 Defender Discovery/Range Rover (02-11) |
133 108 140 |
LEXUS |
Все модели |
103 |
Mercedes-Benz |
A class/SLK/CLK B class/E class S class/M class |
110 103 150 |
Mini |
Mini/Mini Clubman |
140 |
Mitsubishi |
Colt/Almara/Cube/Serena Lancer/Grandis/Outlander |
108 98 |
Nissan |
Micra/Note Teana Patrol/Terrano/Qashqai |
105 110 133 |
Opel |
Frontera Astra Insignia Другие модели |
118 140 150 110 |
Porsche |
Все модели |
130 |
Peugeot |
106 107/308/3008/207/407/807 307/607 |
85 100 90 |
Renault |
Logan Megan II/Scenic II Laguna III/Escape IV |
105 110 130 |
Seat |
Ibiza/Toledo/Leon Alhambra |
120 140 |
Skoda |
Fabia/Octavia/SuperB/Yeti |
120 |
Suzuki |
Swift/Spash Grand Vitara |
85 100 |
Volvo |
XC90/XC60/XC70/S60/S80 XC60/C70/S40 |
140 110 |
Volkswagen |
Polo/Golf/Passat Sharan Touareg |
120 170 180 |
Toyota |
Avensis/Corolla/Jaris Land Cruiser |
103 209 |
Если вам нужна высококвалифицированная помощь в ремонте дисков и шин, снятии и установке колес, утилизации старых покрышек, балансировке — обращайтесь в шиномонтаж в Санкт-Петербурге «Spbkoleso». Здесь обслуживают и легковые автомобили, и джипы, и малые грузовики.
Затяжка резьбовых соединений
Технический уровень и качество крепёжных деталей и соединений имеют важное значение для обеспечения высоких потребительских характеристик машин, механизмов, строительных конструкций, бытовой техники, другой продукции. Известно, что большинство отказов в автотранспортных средствах так или иначе связано с крепёжными деталями, ослаблением соединений, а любые ремонты и обслуживание – с отвинчиванием и завинчиванием болтов, гаек, винтов и т.д.
Надёжность соединений узлов зависит от технического уровня конструкции в целом, качества крепёжных деталей и качества сборки [1].
Надёжность резьбовых соединений — это, в первую очередь, гарантия длительного сохранения усилия предварительной затяжки в период эксплуатации. Как обеспечить это?
Силовые параметры резьбовых соединений. Надёжность крепежа.
Чтобы ответить на поставленный вопрос, сначала назовём основные силовые параметры резьбовых соединений. ГОСТ 1759.4 устанавливает для крепёжных деталей минимальную разрушающую нагрузку(Рр, Н) и пробную нагрузку(N, Н), которая для классов прочности 6.8 и выше составляет 74-79% от минимальной разрушающей нагрузки. Пробная нагрузка является контрольной величиной, которую стержневая крепёжная деталь должна выдержать при испытаниях.
Усилие предварительной затяжки (далее – усилие затяжки – Q, Н), на которое производится затяжка резьбового соединения, обычно принимаетсяв пределах 75-80%, в отдельных случаях и 90%, от пробной нагрузки[1]. Нередко возникает вопрос почему «предварительной»? Дело в том, что затяжка соединений подразумевает создание во всех деталях – и крепёжных, и соединяемых, некоторых напряжений. При этом в упруго напряжённых телах проявляются некоторые механизмы пластических деформаций, ведущие к убыванию напряжений во времени (явление релаксации напряжений). Поэтому по истечении некоторого времени усилие затяжки соединения несколько снижается без каких либо дополнительных силовых воздействий на него. В табл. 1 для справок приведены значения усилий затяжки нескольких размеров соединений.
Таблица 1
Значения усилий затяжки,Q, Н | |||
Размер резьбы болта | Класс прочности 6.8 | Класс прочности 8.8 | Класс прочности 10.9 |
М6 | 7540 | 8700 | 12530 |
М8 | 12750 | 15900 | 22800 |
М10 | 19130 | 25280 | 36080 |
М12 | 27230 | 36680 | 52500 |
Существует несколько способов затяжки резьбовых соединений: затяжка до определённого момента, затяжка до определённого угла, затяжка до предела упругости, затяжка в области пластических деформаций и другие.
Затяжка соединений до определённого момента
В отечественной практике чаще всего применяется затяжка путём приложения к крепёжной детали необходимого крутящего момента затяжки (далее – момента затяжки, Мкр, Н*м), который обычно указывается в чертежах или технологии сборки. В автомобильной промышленности для назначения моментов затяжки используются отраслевые стандарты [2; 3] и руководящий документ [4], которые распространяются на резьбовые соединения с болтами, шпильками и гайками с цилиндрической метрической резьбой номинальным диаметром от М3 до М24 в зависимости от размеров, класса прочности крепёжной детали и класса соединения.
В зависимости от степени ответственности соединений назначаются классы резьбовых соединений и соответствующие им величины максимальных и минимальных моментов затяжки, объёма их контроля (проверки), приведенные в табл.2.
Таблица 2. Классы резьбовых соединений по [3]
Класс соедин. | Наименование | Допускаемое отклон. от расчетного Мкр, % | Объем контроля затяжки | |
Максим. | Минимум | |||
I | Особо ответственные | +5 | -5 | 100% соединений |
II | Ответственные | +5 | -15 | |
III | Общего назначения | +5 | -35 | Периодически, согласно техдок. |
IV | Малоответственные | +5 | -65 |
Несколько иные, но во многом аналогичные классы резьбовых соединений приводит, например, стандарт фирмы Renault[5], называя их классами точности прилагаемого момента:
класс А | имеет поле допуска Мкр на инструменте | ±5% |
класс В | имеет поле допуска Мкр на инструменте | ±10% |
класс М | имеет поле допуска Мкр на инструменте | ±15% |
класс С | имеет поле допуска Мкр на инструменте | ±20% |
класс D | имеет поле допуска Мкр на инструменте | ±35% |
класс Е | имеет поле допуска Мкр на инструменте | ±45% |
Видно, что классы А, В, С, D соответствуют по полю допуска классам по табл. 2.
Номинальный крутящий момент рассчитывается по известной формуле [1; 4;7]:
Мкр = 0,001 Q[0,16 Р + µр 0,58 d2 + µт 0,25 (dт + d0) ],
где µр– коэффициент трения в резьбе;
µт — коэффициент трения на опорном торце;
dт – диаметр опорной поверхности головки болта или гайки,мм;
d0 – диаметр отверстия под крепёжную деталь, мм;
Р – шаг резьбы, мм;
d2– средний диаметр резьбы, мм.
Существенное влияниена затяжку крепёжных соединений оказывают условия контактного трения в резьбе и на опорной поверхности, зависящие от таких факторов, как состояние контактных поверхностей, вид покрытия, наличие смазочного материала, погрешности шага и угла профиля резьбы, отклонение от перпендикулярности опорного торца и оси резьбы, скорость завинчивания и др. Значения коэффициента трения в реальных условиях сборки можно лишь прогнозировать. Как показывают многочисленные эксперименты, они не стабильны. В табл. 3 приведены их справочные значения [6].
Таблица 3. Значения коэффициентов трения в резьбе µри на опорном торце µт
Вид покрытия | Коэффициент трения | Без смазочного материала | Машинное масло | Солидол синтетический | Машинное масло с МоS2 |
Без покрытия | µр | 0,32-0,52 | 0,19-0,24 | 0.16-0,21 | 0,11-0,15 |
µт | 0,14-0,24 | 0,12-0.14 | 0,11-0,14 | 0,07-0,10 | |
Цинкование | µр | 0,24-0,48 | 0,15-0,20 | 0,14-0,19 | 0,14-0,19 |
µт | 0,07-0. | 0.09-0,12 | 0,08-0,10 | 0,06-0,09 | |
Фосфатирование | µр | 0,15-0,50 | 0,15-0,20 | 0,15-0.19 | 0.14-0,16 |
µт | 0,09-0,12 | 0,10-0,13 | 0,09-0,13 | 0,07-0,13 | |
Оксидирование | µр | 0.50-0,84 | 0,39-0.51 | 0,37-0,49 | 0.15-0,21 |
µт | 0,20-0,43 | 0,19-0.29 | 0.19-0,29 | 0,07-0,11 |
Для упрощения расчётов Мкр коэффициенты трения обычно усредняют. В качестве примера в табл. 4 приведены результаты сравнительного расчёта моментов затяжки соединения болт-гайка размером М8, класса прочности 8. 8-8. Значения коэффициентов трения µриµт взяты средними от приведённых в табл.3. Конечные результаты расчётов достаточно близки.
Таблица 4. Результаты сравнительного расчёта момента затяжки крепежа
Вид смазки и покрытия | Разные коэффициенты трения | Усреднен. к-ты трения | |||
µр | µт | Мкр.разд, Н?м | µ=0,5(µр+µт) | Мкр.сред, Н?м | |
6Ц хр | 0,36 | 0,09 | 34,9 | 0,22 | 36,8 |
6Ц хр, солидол | 0,165 | 0,09 | 21,9 | 0.13 | 23,0 |
Без смазки и покрытия | 0,42 | 0,19 | 47,6 | 0,30 | 48,9 |
Для понимания и правильного назначения режимов сборки резьбовых соединений важно знать на что расходуется Мкр. В табл. 5 приведены результаты расчёта момента затяжки в целом и по составляющим. Три составляющие момента затяжки (см. формулу) отражают их доли, идущие на создание усилия затяжки (12-15%), на преодоление сил трения в резьбе (32-39%) и на преодоление сил трения под головкой болта или под гайкой (47-54%) [1].
Как видим на создание усилия затяжки расходуется лишь до 15% Мкр.
Таблица 5. Моменты затяжки соединений и их составляющие, Мкр, Н*м
Размер резьбы ишестигр., мм | Всего | На создание усилия затяжки | На трение в резьбе | На трение под головкой | ||||
Класс прочности | ||||||||
6.8 | 8.8 | 6.8 | 8.8 | 6.8 | 8.8 | 6.8 | 8.8 |
М6; S=10 | 8. | 9,6 | 1.2 | 1,4 | 3,0 | 3,5 | 4,1 | 4,7 |
М8; S=13 | 18,4 | 23 | 2.6 | 3,2 | 6.9 | 8.6 | 8,9 | 11,2 |
М10; S=17 | 35 | 46,3 | 4,6 | 6,0 | 13,0 | 17,2 | 17,4 | 23,5 |
При применении соединений с фланцевыми болтами и гайками важно учитывать влияние на момент затяжки увеличенной опорной поверхности под головкой. Момент требуется на 10-15% выше, чем без фланца.
Крепёж. Точность способа затяжки по моменту
Итак, все действия разработчиков крепёжных соединений в машинах и механизмах сводится к назначению Мкр. Но обеспечит ли этот момент получение необходимого усилия затяжки? Зная сильное влияние условий трения и класса соединения на зависимость между усилием и моментом затяжки, покажем каков может быть разброс достигаемых значений Q при сборке. В качестве примера рассмотрим соединение болт-гайка М8 класса прочности 8.8-8, покрытие цинковое с хроматированием без смазочного материала. Номинальное усилие затяжки Q= 15900 Н.По [4] имеемМкр макс = 24,4 Н*м.
Близкие значения Q и Мкр приводятся в материалах фирм Renault, Gedore, Facom и других.
Рассчитаемпри возможных значениях коэффициентов трения 0,3, 0,14 и 0,10 величины достигаемого усилия затяжки при названных моментах затяжки для соединений II и III классов (табл. 6) и построим диаграмму в координатах Q– Мкр (рис. 1). Виден весьма существенный разброс достигаемых значений усилия затяжки (заштрихованная четырехугольная зона) при заданных крутящих моментах. Для соединений II класса это А2ВСD2, а III класса – А3ВСD3.
Минимально достигаемое усилие затяжки Qминполучается при приложении минимального крутящего момента затяжки Мкр. мин при максимальном коэффициенте трения µмакс(точки А2 и А3 на диаграмме).
Таблица 6. Результаты расчётов усилия затяжки, Q, Н
Момент затяжки, Н/м | Коэффициент трения, µ | ||
0,3 | 0,14 | 0,10 | |
Мкр. макс = 24,4 | 7870 | 15900 | 21030 |
Мкр.мин = 19,8;11 класс | 6390 | 12860 | 17070 |
Мкр. мин = 15,1; 111класс | 4870 | 9800 | 13020 |
Максимальное усилие затяжки Qмакс достигается при приложении максимального крутящего момента Мкр. макс при наименьшем коэффициенте трения µмин (точка С на диаграмме).
Подобные графические изображения могут быть построены для каждого конкретного резьбового соединения. Точка соответствующего соотношения Мкр – Q находится внутри четырёхугольника.
Еще одна характеристика резьбовых соединений, влияющая на точность затяжки по моменту, назовём её «плотность» или «герметичность» стыка соединяемых деталей. Чем больше в пакете деталей (слоев), тем сильнее влияние заусенцев, неровностей, шероховатости контактных поверхностей.
Минимальное удельное усилие на контактных поверхностях должно устанавливаться из условия плотности стыкови не должно быть меньше s0 мин=(0,4 – 0,5)sт. Максимальное значение удельных усилий, обеспечивающих надёжность затяжки должно быть s0 макс=(0,8 – 0,9)sт.
Ранее мы приводили данные [1] о нежелательности применения плоских и пружинных шайб в соединениях и приводили варианты перехода, в частности, на фланцевый крепёж, что существенно повышает надёжность. Там же показаны отрицательные стороны применения болтов с шестигранной уменьшенной головкой, у которых контактные напряжения под головкой превышают sт.
Как видно способ затяжки с контролем момента даже при его точной фиксации не обладает необходимой надёжностью, далеко не всегда обеспечивает нужное усилие затяжки.
Методы контроля затяжки крепежа
Наиболее распространен метод контроля при помощи динамометрических ключей, имеющих точность в пределах ±5%. Ошибка в измерении величины момента зависит от принятого метода его определения. В [4] предусматриваются следующие методы.
Метод А. Момент измеряется непосредственно в начале вращения болта или гайки в направлении затягивания, измеренный таким образом момент называется «моментом страгивания с места». Метод применяется для быстрого контроля и осуществляется не позднее 30 минут после затяжки.
Метод В. Момент измеряется во время вращения при повороте на 10о – 15о в направлении завинчивания. Момент, полученный при этом, называется «моментом вращения». Метод применяется для периодического, но более точного контроля.
Метод С. Соединение освобождается и снова затягивается в прежнем положении, которое должно быть отмечено риской. Этот момент называется «моментом повторной затяжки» и применяется для контроля соединений, имеющих оксидные пленки, окраску, загрязнения.
Величины моментов затяжки при контрольных измерениях должны находитьсяв следующих диапазонах :
| Метод А | Метод В | Метод С |
От | 1,25 Мкр. макс | 1,08 Мкр. макс | 1,05 Мкр. макс |
До | 1,05 Мкр.мин | 0,92 Мкр.мин | 0,88 Мкр. |
В случае недостаточной величины момента затяжки производится подтяжка резьбового соединения до заданной величины момента. Заметим, что контроль качества затяжки особо ответственных соединений (класс 1 ) с допускаемым отклонением момента ±5% динамометрическим ключом, имеющим такую же точность, едва ли корректен.
Таким образом, показано, что как затяжка резьбовых соединений, так и её контроль базируются на косвенных методах путём приложения к крепёжной детали крутящего момента, но это далеко не всегда обеспечивает получение необходимого усилия затяжки.
Поэтому разработчики конструкции вынуждены для обеспечения требуемого усилия сжатия соединяемых деталей применять большее количество недозатянутых крепёжных деталей и увеличивать их диаметр.
Приведем примеры ошибок, которые стали возможными из-за указания в техдокументации только момента затяжки.
На автомобилях семейства ГАЗель при сборке крепления задней опоры двигателя имели место случаи разрушения болтов М10х6gх30 (210406) с полукруглой головкой и квадратным подголовком. Испытания болтов показывали, что они соответствуют требованиям ОСТа и имеют класс прочности 4.8. Оказалось, что, указанный в чертежах узла крутящий момент затяжки Мкрравнялся 28-36 Нм. Это соответствует соединению класса прочности 6.8.в результате усилие затяжки при Мкр. минзавышалось в 1,4 раза, а при Мкр.макс в 1,9 раза! После замены класса прочности болта на 6.8 дефекты сборки были исключены.
При сборке суппорта переднего тормоза автомобилей ВАЗ 2108(09) разрушался болт 2108-3501030 М12х1,25х30, имеющий класс прочности 10.9. Болт, имеющий покрытие фосфат с промасливанием, опирается на шайбу с таким же покрытием и закручивается в чугунный суппорт с цинковым покрытием. По чертежу Мкр.макс=118,4 Нм. В стандартах ВАЗа не было данных по коэффициенту трения для данного сочетания контактных поверхностей. По разным источникам отклонение Мкр могут составлять от ±10% до ±30%. Проведённые исследования этого резьбового соединения и условий его сборки на конвейере позволили выявить, объяснить и устранить причины разрушения болтов[1]. На рис. 2 показана диаграмма Q– Мкр, рассчитанная по методике Фиат-ВАЗ, где n — коэффициент использования предела текучести (n=s:sт, где s — суммарное напряжение в болте, создаваемое при затяжке). Для ответственного соединения (11 класса) коэффициент трения в резьбе и на опорной поверхности варьировался в пределах 0,1–0,18. Было определено, что при m=0,1 момент Мкр.мин=96,5 Нм, а усилие затяжки Q=59536 Н. При Мкр.макс=118,4 Нм усилие Q=73130 Н, что выше нагрузки до предела пропорциональности Qупр=72750 Н, то есть возможна пластическая деформация болта или его разрушение при сборке. Известно, что при случайном попадании масла и колебаниях толщины покрытий коэффициент трения может уменьшится до значения 0,08 и даже 0,06. В то же время было выявлено,что перед сборкой болты проходили операции мойки и промасливания, что недопустимо, ибо ещё больше увеличивало усилие затяжки.
Результаты исследований показали также целесообразность замены цилиндрической головки с внутренним шестигранником у болтана головку с волнистым приводом (типа ТОRХ) и 2-х радиусной поднутренной галтелью под головкой. За счёт этого удалось снизить напряжения под головкой и еще больше повысить надёжность крепления.
Приведённые примеры показывают, что исследования конструкций узлов и технологии сборки позволяют выяснить и исключить возможные дефекты, а также подтверждают необходимость перенесения внимания с момента на усилие затяжки.
О затяжке крепёжных соединений с контролем усилий
В мировой практике используются методы и инструменты, которые непосредственно контролируют усилие затяжки в ходе сборки. Осуществить затяжку резьбового соединения с контролем по усилию в лабораторных условиях несложно. Исследования показывают, что наибольшая точность обеспечения усилий затяжки в производственных усло
23990-13: МТ Ключи динамометрические — Производители, поставщики и поверители
Назначение
Ключи динамометрические МТ (далее ключи) предназначены для измерений крутящего момента силы при затяжке резьбовых соединений.
Описание
Принцип работы ключа заключается в преобразовании усилия, приложенного к ключу и создающего крутящий момент силы, в пропорциональную этому моменту силы угловую деформацию упругого тела (торсиона).
Ключ состоит из торсиона, на одном конце которого закреплён трибко-секторный механизм. Второй конец торсиона выполнен в виде присоединительного квадрата, который через установленную на этом конце трубку и тягу соединен со входом механизма.
Угловая деформация торсиона преобразуется в линейное перемещение конца тяги и далее в трибко-секторном механизме в перемещение стрелки относительно шкалы.
Ключи имеют следующее обозначение в зависимости от направления действия:
— МТ-1, ключи двухстороннего действия для винтов и гаек с правой и левой резьбой;
— МТ-2, ключи одностороннего действия для винтов и гаек с правой резьбой. Условное обозначение ключей и их основные технические характеристики приведены в таблице 1.
Внешний вид ключей представлен на рисунке 1.
Место нанесения знака поверки (клеймо-наклейка) указано на рисунке 2
Место нанесения знака поверки (клеймо-наклейка)
Технические характеристики
Метрологические и технические характеристики приведены в таблице 1. Таблица 1
Условное обозначение ключа |
Диапазон измерений крутящего момента силы, Нм *** |
Цена деле ния шка лы, Нм |
Пределы допус каемой относи тельной погреш ности, % |
Форма и размеры присоединительных элементов |
Масса ключа, кг, не более |
Габаритные размеры, мм, не более: длина x ширина x высота |
Наработка на отказ, циклов, не менее | |
Диаметр отверстия под рукоятку (вороток), мм** |
Размер присоедини-тельного квадрата, мм* | |||||||
МТ-1- 25 |
от 5 до 25 |
1 |
± 4 |
10 |
10,0 |
0,3 |
90x90x60 |
5000 |
МТ-1- 60 |
от 12 до 60 |
2. |
± 4 |
14,0 |
12,5 |
0,3 | ||
МТ-1- 120 |
от 25 до 125 |
5 |
± 4 |
14,0 |
12,5 |
0,3 | ||
МТ-1- 150 |
от 30 до 150 |
5 |
± 4 |
14,0 |
12,5 |
0,3 | ||
МТ-1- 240 |
от 50 до 250 |
10 |
± 4 |
14,0 |
12,5 |
0,3 | ||
МТ-1- 500 |
от 100 до 500 |
20 |
± 4 |
25,0 |
20,0 |
1,0 |
155x115x70 | |
МТ-1- 800 |
от 160 до 800 |
40 |
± 6 |
25,0 |
20,0 |
1,0 |
165x115x70 | |
МТ-1- 1500 |
от 300 до 1500 |
100 |
± 6 |
40,0 |
25,0 |
2,5 |
195x130x75 | |
МТ-2- 60 |
от 12 до 60 |
2,5 |
± 4 |
14,0 |
12,5 |
0,5 |
90x90x60 | |
МТ-2- 120 |
от 25 до 125 |
5 |
± 4 |
14,0 |
12,5 |
0,5 | ||
МТ-2- 240 |
от 50 до 250 |
10 |
± 4 |
14,0 |
12,5 |
0,5 | ||
МТ-2- 500 |
от 100 до 500 |
10 |
± 4 |
25,0 |
20,0 |
1,2 |
185x115x70 |
* — Допуски на присоединительные квадраты — по ГОСТ 24372.
**- Возможно изготовление ключа МТ-1-240М с габаритными размерами 120x90x60 и диаметром отверстия под вороток 18мм.
*** — Все ключи имеют нулевую отметку и оцифрованы от нуля.
Знак утверждения типа
наносится на титульный лист руководства по эксплуатации типографским способом.
Комплектность
Наименование |
Кол-во |
Ключ динамометрический МТ |
1 |
Руководство по эксплуатации |
1 |
Индивидуальная упаковка |
1 |
Поверка
осуществляется по документу МИ 2593-2000 «Рекомендация. Государственная система обеспечения единства измерений. Ключи моментные. Методика поверки».
Эталоны, применяемые при поверке: эталоны 2-го разряда по ГОСТ Р 8.752-2011, диапазон от 5 до 2000 Нм, относительная погрешность ±1 %.
Сведения о методах измерений
Методика измерений приведена в документе «Ключ моментный шкальный (динамометрический) модели МТ. Руководство по эксплуатации. Э.НФ.000.001 РЭ».
Нормативные и технические документы, устанавливающие требования к ключам динамометрическим МТ
1 ГОСТ Р 8.752-2011 «ГСИ. Государственная поверочная схема для средств измерений крутящего момента силы»
2 ТУ РБ 14741830.001-2000. «Ключи моментные шкальные (динамометрические) модели МТ. Технические условия»
Рекомендации к применению
Область применения ключей находится вне сферы государственного регулирования обеспечения единства измерений.
Парковый инструмент | Спецификации и концепции крутящего момента
В этой статье обсуждаются основы использования динамометрического ключа и динамометрического ключа. См. также соответствующую статью об основных понятиях потоков. Эта статья включает в себя таблицу с различными рекомендациями по крутящему моменту.
1Введение в Torque
Резьбовые крепления, такие как гайки и болты, используются для крепления многих компонентов велосипеда. Когда застежка затягивается, застежка фактически изгибается и растягивается, подобно резиновой ленте.Это растяжение не является постоянным, но оно дает суставной силе удерживать вместе, что называется «предварительной нагрузкой» или напряжением. Каждое крепление рассчитано на определенный диапазон натяжения. Слишком сильное затягивание приведет к деформации резьбы или деталей. Слишком маленькая предварительная нагрузка будет означать, что застежка ослабнет при использовании. Это может привести к повреждению компонентов, таких как кривошип с ослабленным крепежным болтом. Ослабленные болты и гайки также обычно являются источником различных скрипов на велосипеде.
Натяжение крепежной детали во многом зависит от крутящего момента, степени затяжки и размера резьбы.Как правило, инженеры указывают размер резьбы, достаточно большой, чтобы выдерживать ожидаемые нагрузки. Например, болт M5 сепаратора бутылки с водой не будет хорошим выбором для удержания рукоятки. Даже если бы болт был максимально затянут, его силы не хватило бы для надежной фиксации рычага на шпинделе. Интерфейс кривошип-шпиндель подвергается довольно большой нагрузке, что делает более крупные резьбы (M8, M12, M14) лучшим выбором. Величина давления, прилагаемого резьбой, может быть существенной, чтобы надежно удерживать соединение.Например, полностью затянутый болт кривошипа может обеспечить усилие более 14 000 ньютонов (сила 3000 фунтов), поскольку он удерживает рычаг на месте.
Принято считать, что болты и гайки часто откручиваются «само по себе», без видимой причины. Однако распространенной причиной ослабления резьбовых соединений является просто отсутствие натяжения при первоначальной сборке. Вибрация, нагрузка, использование или неправильное обращение обычно не могут преодолеть силу зажима в правильно подобранном и надежном резьбовом креплении. Согласно простому эмпирическому правилу, любой крепеж должен быть затянут как можно туже без повреждения резьбы или составных частей.Это означает, что самая слабая часть сустава определяет пределы напряжения и, следовательно, крутящего момента.
Измерение крутящего момента
Крутящий момент для механиков — это просто крутящее или вращательное движение вокруг оси резьбы. Это сопротивление может быть соотнесено с натяжением крепежа, но не является его прямым измерением. Как правило, чем выше сопротивление вращению, тем больше натяжение в резьбовом креплении.Другими словами, чем больше усилий требуется, чтобы затянуть болт, тем сильнее он затянут.
Крутящий момент измеряется как единица силы, действующей на вращающийся рычаг определенной длины. В велосипедной промышленности и в других местах общепринятой единицей измерения крутящего момента является Ньютон-метр (сокращенно Нм). Один ньютон-метр — это сила в один ньютон на рычаге длиной один метр. Другая единица измерения, которую иногда можно увидеть, — это килограмм-сантиметр (сокращенно кгс-см), который представляет собой килограмм силы, действующей на рычаг длиной один сантиметр.Можно конвертировать между различными системами.
Также иногда в Соединенных Штатах используется дюйм-фунт (сокращенно in-lb). Это сила в один фунт, действующая на конец рычага (гаечного ключа) длиной в один дюйм. Другой единицей крутящего момента, используемой в США, является футо-фунт (сокращенно фут-фунт), который представляет собой силу в фунтах, воздействующую на рычаг длиной в один фут. Можно преобразовать между двумя единицами, умножив или разделив на двенадцать. Поскольку это может привести к путанице, лучше придерживаться одного обозначения.Единицы, указанные в таблице крутящего момента здесь, будут в дюйм-фунтах.
Можно конвертировать между различными системами:
- Нм = дюйм-фунт x 0,113
- Нм = фут-фунт x 1,356
- Нм = кг-см x 0,0981
Динамометрические ключи Типы
Динамометрические ключи — это просто инструменты для измерения сопротивления вращению. Существует корреляция между натяжением болта и усилием, которое требуется для его поворота. Любой инструмент, даже динамометрический ключ, следует использовать со здравым смыслом. Болт с крестообразной резьбой не будет должным образом затянут даже динамометрическим ключом. Механик должен знать назначение крутящего момента, а также то, как крутящий момент и предварительная нагрузка крепежа влияют на соединение компонентов. Также важно учитывать подготовку резьбы, которая подробно рассмотрена в этой статье.
Тип балки
Park Tool предлагает динамометрические ключи балочного типа двух типов.Оба ключа используют квадратный хвостовик 3/8″ для установки стандартных бит 3/8″.
TW-1.2 имеет диапазон 0–14 Нм (0–140 дюймов-фунтов). TW-2.2 имеет диапазон 0–60 Нм (0–50 футо-фунтов).
Конструкция балки относительно проста и подходит как для левой, так и для правой резьбы. Головка с гнездом удерживает две стальные балки, основную балку и индикаторную или стрелочную балку. Первичный луч отклоняется при вытягивании рукоятки. Отдельный указательный луч остается неотклоненным, а основной луч под ним изгибается и перемещается вместе с рукояткой. Показания снимаются на конце указателя, на считывающей пластине на первичном луче. Ручка перемещается до тех пор, пока не будет достигнуто желаемое значение. Эти ключи редко требуют повторной калибровки. Если стрелка указателя не указывает на ноль, когда инструмент находится в состоянии покоя, она просто отгибается назад до тех пор, пока не выровняется. Усталость стали не проблема.
Click Type
Park Tool предлагает динамометрические ключи с защелкой двух типов.Оба ключа используют квадратный хвостовик 3/8″ для установки стандартных бит 3/8″.
TW-5.2 имеет диапазон 2–14 Нм (18–124 дюйм-фунт). TW-6.2 имеет диапазон 10–60 Нм (88–530 дюймов-фунтов).
Термин «тип щелчка» может ввести в заблуждение. В данной конструкции динамометрических ключей используется поворотная головка. Есть пружина, которая сжимается при повороте рукоятки. При более высоких настройках пружина сжимается сильнее, что позволяет головке поворачиваться только при более высоком сопротивлении и более высоком крутящем моменте. При высокой настройке слышен щелчок.Но при более низких настройках шум может быть незначительным или вообще отсутствовать, поскольку головка перемещается при повороте. Поворот головки указывает на достижение сопротивления или крутящего момента, а не на щелчок.
Характеристики крутящего момента для велосипеда
Ниже приведена таблица эквивалентов крутящего момента, а формулы для преобразования соответствуют таблице крутящего момента.Таблица также доступна в виде файла PDF.
Все цифры в таблице ниже даны в ньютон-метрах и дюйм-фунтах. Обратите внимание, что некоторые компании не указывают крутящий момент для определенных компонентов или деталей. Свяжитесь с производителем для получения самых последних спецификаций.
Колесо, ступица, зона заднего зубчатого колеса
Компонент | Тип/Марка | Ньютон-метры | Дюйм-фунты |
---|---|---|---|
Натяжение спицы | Крутящий момент обычно не используется в колесах.![]() | ||
Ось | Быстросъемный: закрытый кулачок, тип | Измеренный крутящий момент обычно не используется. Общепринятой отраслевой практикой является сопротивление рычага на полпути от открытого положения до полного закрытия. Дополнительную информацию см. в разделе «Снятие и установка шин и камер». | |
Гайки сплошной оси (колеса небыстросъемного типа) | 29.4–44 | 266–390 | |
Стопорное кольцо звездочки кассеты | Шимано® | 29,4–49 | 260–434 |
СРАМ® | 40 | 354 | |
Кампаньоло® | 50 | 442 | |
Стопорная гайка конуса ступицы | Бонтрагер® | 17 | 150 |
Крис Кинг® | 12.![]() | 100 | |
Шимано® | 9,8–24,5 | 87–217 | |
Корпус втулки | Бонтрагер® | 45 | 400 |
Shimano® | 35–50 | 305–434 | |
Shimano® XTR с шестигранником 14 мм | 45–50 | 392–434 |
Гарнитура, руль, сиденье и стойка сиденья
Компонент | Тип/марка | Ньютон-метры | Дюйм-фунты |
---|---|---|---|
Контргайка гарнитуры с резьбой | Зажимная гайка Chris King®, тип | 14.6–17 | 130–150 |
Танге-Сейки® | 24,5 | 217 | |
Болт крепления штока: пинольный для резьбовых гарнитур | Шимано® | 19,6–29,4 | 174–260 |
Общий ассортимент | 16-18 | 144–168 | |
Болты крепления рулевой колонки без резьбы | Деда® | 8 | 71 |
Углерод FSA® | 8.![]() | 78 | |
Шплинт Syncros®, тип | 10,1 | 90 | |
Томсон® | 5,4 | 48 | |
Монолинк Time® | 5 | 48 | |
Race Face® | 6,2 | 55 | |
Крепление выноса руля: 1 или 2 болта крепления | Шимано® | 19,6–29,4 | 174–260 |
Control Tech® | 13.6–16,3 | 120–144 | |
Крепление выноса руля: лицевая панель с 4 болтами | Контрольная технология® | 13,6–16,3 | 120–144 |
Deda® магний | 8 | 71 | |
FSA® OS-115 углерод | 8,8 | 78 | |
Race Face® | 6,2 | 55 | |
Томсон® | 5,4 | 48 | |
Монолинк Time® | 6 | 53 | |
Концевые удлинители руля MTB | Кейн Крик® | 7.![]() | 70 |
Control Tech® | 16,3 | 144 | |
Крепление для направляющих сиденья | Шимано® | 20–30 | 174–260 |
Кампаньоло® | 22 | 194 | |
Control Tech® с двумя болтами, тип | 16,3 | 144 | |
Control Tech® с одним болтом, тип | 33,9 | 300 | |
Синкрос® | по 5 болтов | 44.по 2 болта | |
Монолинк Time® | 5 | 44,2 | |
Труватив® | Болт M8: 22–24 Болт M6: 6–7,1 | Болт M8: 195–212 Болт M6: 53–63 | |
Держатель стойки сиденья* | Кампаньоло® | 4–6,8 | 36–60 |
*ПРИМЕЧАНИЕ. Стойки сиденья требуют лишь минимального затягивания, чтобы они не соскальзывали вниз. Избегайте чрезмерного затягивания.
Система шатунов, каретка и область педалей
Компонент | Тип/Марка | Ньютон-метры | Дюйм-фунты |
---|---|---|---|
Педаль в кривошип | Шимано® | 35 минимум | 309.7 минимум |
Кампаньоло® | 40 | 354 | |
Ричи® | 34,7 | 307 | |
Труватив® | 31,2–33,9 | 276–300 | |
Стяжные болты кривошипа со шлицем | Shimano® Hollowtech® II | 9,9–14,9 | 88–132 |
FSA® MegaExo™ | 9,8–11,3 | 87–100 | |
Колпачок регулировки кривошипа | Shimano® Hollowtech® II | 0.5–0,7 | 4–6 |
FSA® MegaExo™ | 0,5–0,7 | 4–6 | |
Болт шатуна (включая шатуны со шлицами и шатуны с квадратным валом) | Шимано® | 34–44 | 305–391 |
Shimano® Octalink® XTR® (резьба M15) | 40,3–49 | 357–435 | |
Кампаньоло® | 32–38 | 282–336 | |
Кампаньоло® Ultra-Torque® | 42 | 371 | |
Болт FSA® M8 | 34–39 | 304–347 | |
Сталь FSA® M14 | 49–59 | 434–521 | |
Race Face® | 54 | 480 | |
Синкрос® | 27 | 240 | |
Truvativ® ISIS Drive | 43–47 | 384–420 | |
Квадратный стержень Truvativ® | 38–42 | 336–372 | |
Уайт Индастриз™ | 27–34 | 240–300 | |
Колпачок шатуна с одним ключом | Шимано® | 5–6.![]() | 44–60 |
Труватив® | 12–14 | 107–124 | |
Кассета звездочки к шатуну (стопорное кольцо) | Шимано® | 50–70 | 443–620 |
Болт передней звезды: сталь | Шимано® | 7,9–10,7 | 70–95 |
Кампаньоло® | 8 | 71 | |
Race Face® | 11.3 | 100 | |
Труватив® | 12.1–14 | 107–124 | |
Болт звездочки: алюминий | Шимано® | 5–10 | 44–88,5 |
Кампаньоло® | 8 | 70,8 | |
Труватив® | 8–9 | 70,8–79,6 | |
Нижний кронштейн: картриджного типа | Шимано® | 49.1–68,7 | 435–608 |
Shimano® Hollowtech® II | 34,5–49,1 | 305–435 | |
Campagnolo® (трехкомпонентный) | 70 | 612 | |
Чашки Campagnolo® Ultra-Torque® | 35 | 310 | |
ФСА® | 39,2–49 | 347–434 | |
Race Face® | 47,5 | 420 | |
Труватив® | 33.![]() | 300–360 | |
Уайт Индастриз™ | 27 | 240 |
Зона переключателя и рычага переключения передач
Компонент | Тип/Марка | Ньютон-метры | Дюйм-фунты |
---|---|---|---|
Зажимной болт рычага двойного управления тормозом/переключателем | Шимано® СТИ™ | 6–8 | 53–70 |
Кампаньоло® | 10 | 89 | |
СРАМ® | 6–8 | 53–70 | |
Рычаг переключения: вертикальный/плоский | Шимано® СТИ™ | 5–7.4 | 44–69 |
Рычаг переключения передач: поворотная рукоятка | Шимано® Ревошифт® | 6–8 | 53–70 |
СРАМ® | 17 | 150 | |
Рычаг переключения передач: MTB с большим пальцем | Шимано® СТИ™ | 2,4–3 | 22–26 |
Хомут переднего переключателя | Кампаньоло® | 5 | 44 |
Кампаньоло® | 7 | 62 | |
Шимано® | 5–7 | 44–62 | |
СРАМ® | 4.![]() | 39,8 | |
СРАМ® | 5–7 | 44–62 | |
Стяжной болт троса переднего переключателя | Шимано® | 5-6,8 | 44–60 |
Кампаньоло® | 5 | 44 | |
Мавик® | 5–7 | 44–62 | |
СРАМ® | 4,5 | 40 | |
Болт крепления заднего переключателя | Шимано® | 8–10 | 70–86 |
СРАМ® | 8–10 | 70–86 | |
Кампаньоло® | 15 | 133 | |
Стяжной болт троса заднего переключателя | Шимано® | 5–7 | 44–60 |
СРАМ® | 4–5 | 35.4–44,2 | |
Кампаньоло® | 6 | 53 | |
Болт шкива заднего переключателя | Шимано® | 2,9–3,9 | 27–34 |
Тормозной суппорт и область рычага
Компонент | Тип/Марка | Ньютон-метры | Дюйм-фунты |
---|---|---|---|
Рычаги тормоза стойки | Шимано® | 6–8 | 53–69 |
Авид® | 5–7 | 44–62 | |
Кампаньоло® | 10 | 89 | |
Крепление тормозного суппорта к раме: боковая тяга, двойная ось, центральная тяга | Шимано® | 7.![]() | 70–86 |
Кампаньоло® | 10 | 89 | |
Кейн Крик® | 7,7–8,1 | 68–72 | |
Тектро® | 8–10 | 69–89 | |
Крепление тормозного суппорта к раме: линейное или консольное | Шимано® | 8–10 | 69–89 |
СРАМ® | 5–6,8 | 45–60 | |
Авид® | 4.9–6,9 | 43–61 | |
Control Tech® | 11,3–13,6 | 100–120 | |
Тектро® | 6–8 | 53–69 | |
Тормозная колодка: Резьбовая шпилька | Авид® | 5,9–7,8 | 53–69 |
Кампаньоло® | 8 | 71 | |
Кейн Крик® | 6,3–6,7 | 56–60 | |
Тектро® | 5–7 | 43–61 | |
Шимано® | 5–7 | 43–61 | |
СРАМ® | 5.![]() | 50–70 | |
Тормозная колодка: гладкая шпилька | Шимано® | 7,9–8,8 | 70–78 |
Тормозная колодка: Боковые и двухшарнирные болты | Кампаньоло® | 8 | 72 |
Кейн Крик® | 6,3–6,7 | 56–60 | |
Шимано® | 6–8 | 53–69 | |
Тектро® | 5–7 | 43–61 | |
Стяжной болт тормозного троса: линейная тяга и консоль | Контрольная технология® | 4.5–6,8 | 40–60 |
Шимано® | 6–7,8 | 53–69 | |
СРАМ® | 5,6–7,9 | 50–70 | |
Тектро® | 6–8 | 53–69 | |
Стяжной болт тормозного троса: боковая тяга/двойная ось/центральная тяга | Кампаньоло® | 5 | 44 |
Кейн Крик® | 7,7–8,1 | 68–72 | |
Мавик® | 7–9 | 62–80 | |
Шимано® | 6–8 | 53–69 | |
Тектро® | 6–8 | 53–69 |
Дисковые тормозные системы
Компонент | Тип/Марка | Ньютон-метры | Дюйм-фунты |
---|---|---|---|
Дисковый ротор к ступице: стопорное кольцо | Авид® | 40 | 350 |
Шимано® | 40 | 350 | |
Дисковый ротор к ступице: болты M5 | Авид® | 6.![]() | 55 |
Хейс® | 5,6 | 50 | |
Магура® | 3,8 | 34 | |
Шимано® | 2–4 | 18–35 | |
Крепление корпуса суппорта | Авид® | 9–10,2 | 80–90 |
Хейс® | 12,4 9 с вилками Manitou | 110 80 с вилками Manitou | |
Магура® | 5.7 | 51 | |
Шимано® | 6–8 | 53–69 | |
Тектро® | 6–8 | 53–69 | |
Фитинги для гидравлических шлангов | Хейс® | 6,2 | 55 |
Формулы для преобразования других обозначений крутящего момента в ньютон-метры (Нм) и дюйм-фунты (дюйм-фунт):
- Нм = дюйм-фунт x 0.113
- Нм = фут-фунт x 1,356
- Нм = кг-см x 0,0981
- дюйм-фунт = фут-фунт x 12
- дюйм-фунт = Нм x 8,851
- дюйм-фунт = кгс-см x 0,87
Эквиваленты крутящего момента
Ньютон-метр (Нм) | Приблизительное значение дюйм-фунт (дюйм-фунт) | Приблизительное значение фут-фунт (фут-фунт) |
---|---|---|
1 | 8,9 | 0.![]() |
2 | 17,7 | 1,5 |
3 | 26,6 | 2,2 |
4 | 35,4 | 3,0 |
5 | 44,3 | 3,7 |
6 | 53,1 | 4,4 |
7 | 62,0 | 5,2 |
8 | 70,8 | 5,9 |
9 | 79.7 | 6,6 |
10 | 88,5 | 7,4 |
11 | 97,4 | 8.1 |
12 | 106,2 | 8,9 |
13 | 115,1 | 9,6 |
14 | 123,9 | 10,3 |
15 | 132,8 | 11.1 |
16 | 141,6 | 11.8 |
17 | 150,5 | 12,5 |
18 | 159,3 | 13,3 |
19 | 168,2 | 14,0 |
20 | 177,0 | 14,8 |
21 | 185,9 | 15,5 |
22 | 194,7 | 16,2 |
23 | 203,6 | 17,0 |
24 | 212.![]() | 17,7 |
25 | 221,3 | 18,4 |
26 | 230,1 | 19,2 |
27 | 239,0 | 19,9 |
28 | 247,8 | 20,7 |
29 | 256,7 | 21,4 |
30 | 265,5 | 22,1 |
31 | 274,4 | 22.9 |
32 | 283,2 | 23,6 |
33 | 292,1 | 24,3 |
34 | 300,9 | 25,1 |
35 | 309,8 | 25,8 |
36 | 318,6 | 26,6 |
37 | 327,5 | 27,3 |
38 | 336,3 | 28,0 |
39 | 345.2 | 28,8 |
40 | 354,0 | 29,5 |
41 | 362,9 | 30,2 |
42 | 371,7 | 31,0 |
43 | 380,6 | 31,7 |
44 | 389,4 | 32,5 |
45 | 398,3 | 33,2 |
46 | 407,1 | 33.![]() |
47 | 416,0 | 34,7 |
48 | 424,8 | 35,4 |
49 | 433,7 | 36,1 |
50 | 442,6 | 36,9 |
Bolt Torque Calculator
Соотношение между приложенным крутящим моментом и осевой силой или нагрузкой на болт можно рассчитать по этому общему уравнению как где
T = момент затяжки (Нм, фунт f фут)
K = константа, зависящая от материала и размера болта
F = осевое усилие болта (Н, фунт f )
l = коэффициент смазки (%)
Типовые значения K для болтов из мягкой стали в диапазоне от 1/4″ до 1″:
- нормальный сухой: K = 0.2
- Nanced Black Finith: K = 0.3
- k = 0.2
- слегка смазанный: K = 0.
- Cadmium Closed: K = 0.16
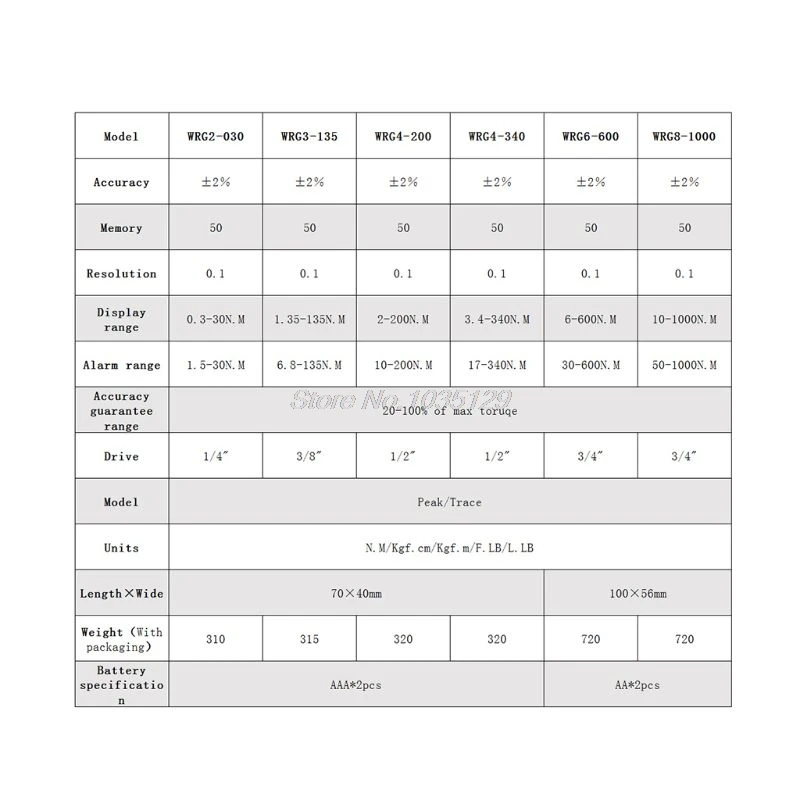
Примечание. ! — имейте в виду, что это грубый расчет, в который не включен шаг винта. Типичные моменты затяжки болтов в метрической и британской системе мер указаны по ссылкам ниже:
Производственные данные всегда следует проверять перед использованием.
Кроме того, точность динамометрического ключа обычно не выше +-25%.
Типовой метрический и британский крутящий момент для болтов
Калькулятор крутящего момента для болтов
Приведенный ниже калькулятор можно использовать для расчета крутящего момента, необходимого для достижения заданного осевого усилия болта или нагрузки. Калькулятор является универсальным и может использоваться для имперских и метрических единиц, если использование единиц согласовано.
K — K — k — C — Константа
D — диаметр болта (м, футов)
F — осевая сила болта или нагрузка (N, LB F )
Снижение крутящего момента из-за смазки (%)
Обратите внимание, что стандартные крутящие моменты всухую обычно рассчитываются для создания растягивающего напряжения — или осевой силы, или зажимной нагрузки — в болте, равном 70 % минимального предела прочности на растяжение или 75 % условного предела прочности.
Пример. Требуемый крутящий момент для затяжки британского болта
Требуемое усилие зажима болта для соединения составляет 20000 фунтов . Крутящий момент, необходимый для сухого стального болта 3/4 дюйма со смазкой 0% для достижения этого натяжения, можно рассчитать как 12 фут/дюйм) (1 — (0%) / (100%))
= 250 (фунт f фут)
Пробная нагрузка для метрического болта
M30 класса 8.8 это 337000 N . Крутящий момент, необходимый для достижения этого натяжения с сухим болтом со смазкой 0% , можно рассчитать как T сухой = (0,2) ( 337000 Н ) (30 мм) (10 -3 м/ мм)
= 2022 (Нм)
Смазывание болта маслом SAE 30 снижает крутящий момент, необходимый для достижения того же натяжения, примерно на 40 %. Уменьшенный крутящий момент можно рассчитать как
T SAE30 = (2022 Нм) (1 — (40%) / (100%))
= 1213 Нм
Усилие болта по сравнению сКрутящий момент
Экв. 1 можно преобразовать, чтобы выразить силу болта как
F = T / (K d (1 — l / 100)) (1a)
Пример — сухой болт по сравнению со смазанным болтом
Пробная нагрузка для 90 9076 M3 метрический болт класса 8.8 337000 N . Крутящий момент, необходимый для достижения этой силы с помощью сухого болта , рассчитывается как 2022 Нм .
При выходе из строя болт смазывается смазкой и затягивается с тем же моментом 2022 Нм .Сила, действующая в смазанном болте, может быть рассчитана как
F смазанный = (2022 Нм) / (0,2 (0,03 м) (1 — (40%) / (100%))))
= 561667 N
Это намного больше, чем может выдержать болт, и вероятен фатальный сбой .
Калькулятор силы болта
Этот калькулятор можно использовать для расчета силы, действующей на болт.
T — крутящий момент (NM, LB F FT)
K — Константа
D — Диаметр болта (M, Ft)
Уменьшение крутящего момента из-за смазки (%)
Награда за вращательную кинематику
Крутящий момент
Крутящий момент (τ) — это сила, которая заставляет объект вращаться. Если вы думаете об использовании гаечного ключа для затягивания болта, то чем ближе к болту вы прикладываете усилие, тем труднее повернуть ключ, а чем дальше от болта вы прикладываете усилие, тем легче поворачивать ключ. . Это связано с тем, что вы создаете больший крутящий момент, когда прикладываете силу на большем расстоянии от оси вращения.
Давайте посмотрим на пример гаечного ключа, поворачивающего болт. Сила приложена на расстоянии от оси вращения.Назовите это расстояние r. Когда вы прикладываете силы под углом 90 градусов к воображаемой линии, идущей от оси вращения к точке приложения силы (известной как линия действия), вы получаете максимальный крутящий момент. По мере того, как угол, под которым прикладывается сила, уменьшается (θ), уменьшается и крутящий момент, заставляющий болт поворачиваться. Следовательно, вы можете рассчитать прилагаемый крутящий момент как:
В некоторых случаях физики называют rsinθ плечом рычага или плечом момента системы. Плечо рычага — это перпендикулярное расстояние от оси вращения до точки приложения силы. С другой стороны, вы можете думать о крутящем моменте как о компоненте силы, перпендикулярной рычагу, умноженной на расстояние r. Единицами крутящего момента являются единицы силы × расстояние или ньютон-метры (Н·м).
Вопрос: Пиратский капитан берет штурвал и поворачивает штурвал своего корабля, прикладывая к спице колеса силу в 20 ньютонов.Если он приложит силу в радиусе 0,2 м от оси вращения под углом 80° к линии действия, какой крутящий момент он приложит к колесу?
Ответ:
Вопрос: Механик затягивает выступы на шине, прилагая крутящий момент 110 Н·м под углом 90° к линии действия. Какая сила приложена, если ключ равен 0.
4 метра в длину?
Ответ:
Вопрос: Какой длины должен быть ключ, если механик способен приложить усилие только 200 Н?
Ответ:
Говорят, что объекты, которые не имеют вращательного ускорения или чистого крутящего момента равны нулю, находятся в равновесии вращения. Это означает, что любой чистый положительный (против часовой стрелки) крутящий момент уравновешивается равным чистым отрицательным крутящим моментом (по часовой стрелке).
Момент инерции
Ранее инерционная масса объекта (его поступательная инерция) определялась как способность этого объекта сопротивляться линейному ускорению. Точно так же вращательная инерция объекта или момент инерции описывает сопротивление объекта вращательному ускорению. Символ момента инерции объекта I.
Объекты, большая часть массы которых находится вблизи оси вращения, имеют небольшую инерцию вращения, в то время как объекты, масса которых находится дальше от оси вращения, имеют большую инерцию вращения.
Для обычных объектов вы можете найти формулу их момента инерции. Для более сложных объектов момент инерции можно рассчитать, взяв сумму всех отдельных частиц массы, составляющих объект, умноженную на квадрат их радиуса от оси вращения. Это может быть довольно обременительно с использованием алгебры, и поэтому обычно предоставляется курсам, основанным на исчислении, или числовым приближениям с использованием вычислительных систем.
Вопрос: Рассчитайте момент инерции твердого шара массой 10 кг и радиусом 0.2 м.
Ответ:
Вопрос: Рассчитайте момент инерции полого шара массой 10 кг и радиусом 0,2 м.
Ответ:
Второй закон Ньютона для вращения
В главе о динамике вы узнали о силах, заставляющих объекты ускоряться. Чем больше результирующая сила, тем больше линейное (или поступательное) ускорение, и чем больше масса объекта, тем меньше поступательное ускорение.
Вращательный эквивалент этого закона, 2-й закон Ньютона для вращения, связывает крутящий момент объекта с его результирующим угловым ускорением. Чем больше чистый крутящий момент, тем больше ускорение вращения, и чем больше инерция вращения, тем меньше ускорение вращения:
Вопрос: Какое угловое ускорение испытывает однородный твердый диск массой 2 кг и радиусом 0.1 м при приложении чистого крутящего момента 10 Н·м? Предположим, что диск вращается вокруг своего центра.
Ответ:
Вопрос: Карусель на игровой площадке с моментом инерции 100 кг·м 2 начинается с состояния покоя и ускоряется силой 150 Н в радиусе 1 м от его центра.
Если эта сила приложена под углом 90° к линии действия в течение времени 0.5 секунд, какова конечная скорость вращения Round-A-Bout?
Ответ: Начните с создания нашей таблицы кинематики вращения:
Поскольку вы знаете только два элемента на столе, вы должны найти третий, прежде чем решать это с помощью уравнений кинематики вращения. Поскольку вам дан момент инерции Round-A-Bout, а также приложенная сила, вы можете найти угловое ускорение, используя 2-й закон Ньютона для вращательного движения.
Теперь, используя свою кинематику вращения, определите конечную угловую скорость кругового движения.
Калькулятор динамометрического ключа для удлиненного адаптера с формулами
Калькулятор динамометрического ключа для удлиненного адаптера с формулами
Меню разработки и проектирования крутящего момента
Адаптер динамометрического ключа Расширенные уравнения и калькулятор
Ниже приведены расчеты, которые можно использовать для определения фактического крутящего момента при использовании удлинителя или гусиной лапы. Для расширенного калькулятора адаптера динамометрического ключа требуется браузер с поддержкой Java.
При использовании адаптера динамометрического ключа, который уменьшает расстояние от привода динамометрического ключа до места приложения силы (места рукоятки), используйте следующие формулы для получения правильного показания или настройки динамометрического ключа.
ОТКРЫТИЕ: Динамометрический ключ Калькулятор адаптера «гусиная лапка»
OPEN: Переходник для динамометрического ключа Расширенные формулы и калькулятор
Где:
T = требуемый или фактический требуемый крутящий момент (фунт-дюйм),
Y = установка или показание крутящего момента для получения желаемого крутящего момента «T» (дюйм-фунт),
L = расстояние между приложенной силой и центром привода динамометрического ключа (дюйм),
E = Расстояние между центром привода динамометрического ключа и центром привода гусиной лапки (дюймы),
F = Приложенное усилие (фунты).
Примечание. Единицами длины могут быть миллиметры, футы или другие единицы, если при расчете используются одинаковые единицы измерения:
Защита от крутящего момента
Из-за разницы в длине от приложенной силы F до адаптера крепежа показание или настройка крутящего момента на динамометрическом ключе изменяется на Y для получения желаемого крутящего момента T.
Поэтому:
Y = F · L (установка или показания динамометрического ключа)
Фактический крутящий момент, приложенный к приводному центру удлинителя:
T = F · ( L + E )
Переставить для F:
F = Y / L
и
F = T / ( L + E )
F = F поэтому подставляя получаем:
Y / L = T / ( L + E )
или
Y = T · L / ( L + E )
Связанные:
Шпильки— Таблицы моментов затяжки — Таблица 2 Шпильки
— Таблицы моментов затяжки — Таблица 2 — Шпильки ASTM 193, класс B7 и ASTM 193, класс B16
Таблицы крутящих моментов построены на конкретных предположениях относительно коэффициента болта и гайки. Прежде чем использовать данную таблицу крутящих моментов, эти допущения следует проверить, чтобы убедиться, что они подходят для конкретного применения.
Даже если все допущения верны, результаты могут отличаться в зависимости от реальных условий. Многие факторы вызывают разброс результатов или увеличивают присущую процессу болтового соединения изменчивость. К ним относятся вариации орехового фактора; состояние болтов, фланцев и гаек; калибровка и состояние оборудования; перпендикулярность болта, гайки и фланца; и Т. Д.
Значения в таблицах основаны на уравнении.
T = значение крутящего момента, (фут-фунты) F = предварительная нагрузка болта, (фунты) k = коэффициент гайки, основанный на используемой смазке d = номинальный диаметр болта, (дюймы) |
Фактор гайки не является коэффициентом трения.
Экспериментально полученная константа, учитывающая влияние трения.
ft-lbs в нм = 0,737562149277
нм в ft-lbs = 1. 3558179
Таблица 2 / Момент затяжки FT-LBS — Шпильки по ASTM 193, класс B7 и ASTM 193, класс B16 | |||
БОЛТ ДИАМ. | Крутящий момент FT-LBS | ||
30% Начальный Крутящий момент | 70% Крутящий момент | 100% Окончательный Крутящий момент | |
1/2 | 17 | 39 | 55 |
16 сентября | 24 | 55 | 80 |
5/8 | 33 | 77 | 110 |
3/4 | 59 | 137 | 195 |
7/8 | 93 | 217 | 310 |
1 | 140 | 325 | 465 |
1.1/8 | 205 | 480 | 685 |
1,1/4 | 288 | 672 | 960 |
1,3/8 | 391 | 915 | 1305 |
1,1/2 | 518 | 1208 | 1725 |
1,9/16 | 588 | 1372 | 1960 |
1,5/8 | 668 | 1558 | 2225 |
1.![]() | 840 | 1960 | 2800 |
1,7/8 | 1044 | 2436 | 3480 |
2 | 1280 | 2985 | 4265 |
2,1/4 | 1850 | 4315 | 6165 |
2,1/2 | 2565 | 5985 | 8550 |
2,3/4 | 3121 | 7282 | 10400 |
3 | 4080 | 9520 | 13600 |
Таблица 2 / Крутящий момент, Н·м — шпильки по ASTM 193, класс B7 и ASTM 193, класс B16 | |||
БОЛТ ДИАМ. | Крутящий момент, Н·м | ||
30% Начальный Крутящий момент | 70% Крутящий момент | 100% Окончательный Крутящий момент | |
1/2 | 23 | 53 | 75 |
16 сентября | 33 | 75 | 108 |
5/8 | 45 | 104 | 149 |
3/4 | 80 | 186 | 264 |
7/8 | 126 | 294 | 420 |
1 | 190 | 441 | 630 |
1.![]() | 278 | 651 | 929 |
1,1/4 | 390 | 911 | 1302 |
1,3/8 | 530 | 1241 | 1769 |
1,1/2 | 702 | 1638 | 2339 |
1,9/16 | 797 | 1860 | 2657 |
1,5/8 | 906 | 2112 | 3017 |
1.3/4 | 1139 | 2657 | 3796 |
1,7/8 | 1415 | 3303 | 4718 |
2 | 1735 | 4047 | 5783 |
2,1/4 | 2508 | 5850 | 8359 |
2,1/2 | 3478 | 8115 | 11592 |
2,3/4 | 4232 | 9873 | 14101 |
3 | 5532 | 12907 | 18439 |
Примечания. .
- Момент затяжки болта для достижения предела текучести болта 50% при коэффициенте гайки, K=0,16
- Эта таблица применима к пасте Never-Seize и смазке Fel-Pro, K=0,16.
- Приведенная выше таблица применима только к шпилькам ASTM A320 класса L7, A193 класса B7 и A193 класса B16.
- Значения крутящего момента утверждены для спирально-навитых графитовых и политетрафторэтиленовых прокладок, графитовых листовых прокладок типов GHE и GHR, кольцевых соединений, прокладок с двойной оболочкой и прокладок Camprofile с графитовой и тефлоновой футеровкой.
- Окончательное значение крутящего момента учитывает ослабление болта на 10 %.
- Эта таблица неприемлема для шпилек и гаек с покрытием из ПТФЭ, см. Таблицу 5.
ДРУГИЕ ТАБЛИЦЫ МОМЕНТА ЗАТЯЖКИ БОЛТОВ
ТАБЛИЦА МОМЕНТА ЗАТЯЖКИ БОЛТОВ 1 — ASTM A193 И ASTM A320 КЛАССА B8, CL2 ШПИЛЬКИ
ТАБЛИЦА МОМЕНТА ЗАТЯЖКИ БОЛТОВ 1A — ХОЛОДНАЯ РАБОТА ASTM A193 И ASTM A320 КЛАССА B8, CL2 ШПИЛЬКИ
МОМЕНТ ЗАТЯЖКИ ТАБЛИЦА 2 — ШПИЛЬКИ ASTM 193, МАРКА B7 И ASTM 193, МАРКА B16
ТАБЛИЦА МОМЕНТА ЗАТЯЖКИ БОЛТОВ 2A — ХОЛОДНЫЕ БОЛТЫ ASTM A320 GRADE L7
МОМЕНТ ЗАТЯЖКИ ТАБЛИЦА 3 — ИСПОЛЬЗОВАТЬ ТОЛЬКО С БОЛТАМИ A193 B8, CL1 ПРИ 540°C — 650°C НА НЕИЗОЛИРОВАННЫХ ФЛАНЦАХ
МОМЕНТ ЗАТЯЖКИ ТАБЛИЦА 4 — ИСПОЛЬЗОВАТЬ ТОЛЬКО С АЛЮМИНИЕВЫМИ ФЛАНЦАМИ 6061-T6
МОМЕНТ ЗАТЯЖКИ ТАБЛИЦА 5 — ШПИЛЬКИ ASTM A193 B7 и ASTM 193 B16 С ПТФЭ ПОКРЫТИЕМ
ТАБЛИЦА МОМЕНТА ЗАТЯЖКИ БОЛТОВ 5A — ШПИЛЬНЫЕ БОЛТЫ С ПТФЭ-ПОКРЫТИЕМ ASTM A320 GRADE L7
Момент затяжки | Инженерная библиотека
На этой странице представлены разделы о правильном моменте затяжки болтов из Barrett, «Fastener Design Manual», справочной публикации НАСА 1228, 1990.
Другие связанные главы из «Руководства по проектированию крепежа» НАСА можно увидеть справа.
Момент затяжки
Определение правильного крутящего момента для крепежа является самой большой проблемой при установке крепежа. Некоторые из многих переменных, вызывающих проблемы,
- Коэффициент трения между сопрягаемыми нитями
- Коэффициент трения между головкой болта (или гайки) и его сопрягаемой поверхностью
- Влияние покрытий болтов и смазок на коэффициенты трения
- Процент прочности болта на растяжение, используемый для предварительного натяга
- Как только будет достигнуто соглашение по пункту 4, как точно определить это значение
- Относительная жесткость конструкции и болтов
- Формулы взаимодействия, которые следует использовать для объединения одновременных сдвигающих и растягивающих нагрузок на болт (следует ли включать в расчеты взаимодействия нагрузки трения из-за действия зажима болта?)
- Должен ли «рабочий крутящий момент» для запорного устройства добавляться к обычному крутящему моменту
Разработка таблиц крутящего момента
Коэффициент трения может варьироваться от 0. 04 до 1.10, в зависимости от материалов и смазок, используемых между сопрягаемыми материалами. (В таблице IV из ссылки 2 приведены различные коэффициенты трения.) Поскольку расчетные значения крутящего момента являются функцией коэффициентов трения между сопрягаемой резьбой и между головкой болта или гайкой и ее сопрягаемой поверхностью, жизненно важно, чтобы используемые значения крутящего момента в таблице корректируются, чтобы отразить любые различия в коэффициентах трения между теми, которые использовались для расчета таблицы, и значениями пользователя.Крутящий момент должен быть включен в значения, указанные в таблицах, потому что любой крутящий момент создает срезывающую нагрузку на болт.
Значения крутящего момента в таблице V были рассчитаны, как указано в сносках, с использованием формул из ссылки 3. (Аналогичная таблица была опубликована в Product Engineering Артуром Корном примерно в 1944 г.)
Более высокие крутящие моменты (вплоть до теоретического предела текучести) иногда используются для болтов, которые нельзя зафиксировать, чтобы противостоять вибрации. Более высокая нагрузка повысит виброустойчивость болта, но болт будет деформироваться и разгружаться, если его предел текучести будет непреднамеренно превышен.Поскольку точный крутящий момент текучести не может быть определен без обширного инструментария, не рекомендуется закручивать болт близко к пределу текучести.
Допустимая нагрузка на крепеж иногда указывается в литературе. Это значение обычно составляет 75 процентов от теоретического предела текучести, чтобы предотвратить непреднамеренный выход крепежа из-за неточности измерения крутящего момента.
Размер | Корневая зона, дюймов 2 | Диапазон крутящего момента (класс 8, 150 тысяч фунтов/кв. ![]() |
---|---|---|
10-24 | 0,0145 | от 23 до 34 дюймов на фунт |
10-32 | 0,0175 | от 29 до 43 фунтов на дюйм |
1/4-20 | 0.0269 | от 54 до 81 фунт-дюйм |
1/4-28 | 0,0326 | от 68 до 102 фунтов на дюйм |
16-18 5/18 | 0,0454 | от 117 до 176 дюймов-фунтов |
16-24 мая | 0,0524 | от 139 до 208 дюймов-фунтов |
3/8-16 | 0,0678 | от 205 до 308 дюймов-фунтов |
3/8-24 | 0,0809 | от 230 до 345 дюймов-фунтов |
16-14 июля | 0.0903 | от 28 до 42 футов-фунтов |
16-20 июля | 0,1090 | от 33 до 50 футофунтов |
1/2-13 | 0,1257 | от 42 до 64 футофунтов |
1/2-20 | 0,1486 | от 52 до 77 футофунтов |
16-12 сентября | 0,1620 | от 61 до 91 фут-фунт |
16-18 сентября | 0,1888 | от 73 до 109 футофунтов |
5/8-11 | 0.![]() | от 84 до 126 футофунтов |
5/8-18 | 0,2400 | от 104 до 156 футофунтов |
3/4-10 | 0,3020 | от 117 до 176 ft-lb (Примечание 2) |
3/4-16 | 0,3513 | от 139 до 208 футо-фунтов (Примечание 2) |
7/8-9 | 0,4193 | от 184 до 276 ft-lb (Примечание 2) |
7/8-14 | 0.4805 | от 213 до 320 ft-lb (Примечание 2) |
1-8 | 0,5510 | от 276 до 414 ft-lb (Примечание 2) |
1-14 | 0,6464 | от 323 до 485 ft-lb (Примечание 2) |
1 1/8-7 | 0,6931 | от 390 до 585 ft-lb (Примечание 2) |
1 1/8-12 | 0,8118 | от 465 до 698 ft-lb (Примечание 2) |
1 1/4-7 | 0.![]() | от 559 до 838 ft-lb (Примечание 2) |
1 1/4-12 | 1.0238 | от 655 до 982 футо-фунтов (Примечание 2) |
Примечание 1: Приведенные значения представляют собой 50 и 75 процентов от теоретического предела текучести материала болта с пределом текучести 120 тысяч фунтов на квадратный дюйм. Соответствующие значения для материалов с различным пределом текучести можно получить, умножив эти табличные значения на отношение соответствующих пределов текучести материалов. | ||
Примечание 2. Болты 0,75 дюйма. диаметр и больше имеют пониженные допустимые пределы (75 процентов от нормальной прочности) из-за невозможности термической обработки такого большого поперечного сечения до равномерной твердости. |
Альтернативная формула крутящего момента
Популярной формулой для быстрого расчета момента затяжки болтов является T = KFd, где T обозначает крутящий момент, F обозначает осевую нагрузку, d обозначает диаметр болта, а K (коэффициент крутящего момента) является расчетным значением по формуле:
$$ K = \left({ d_m \over 2d }\right) { \tan{\psi} + \mu \sec{\alpha} \over 1 — \mu \tan{\psi} \sec{\alpha} } + 0.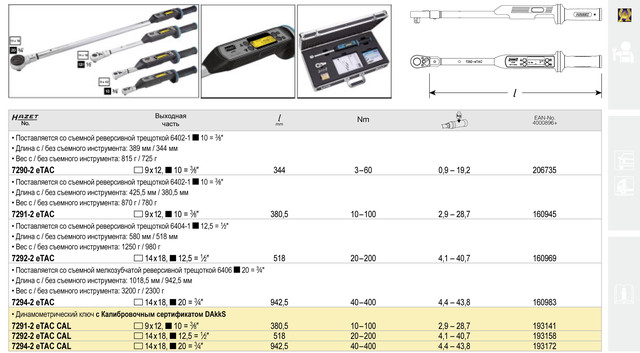
как указано в ссылке 4 (стр. 378), где
д м | средний диаметр резьбы |
ψ | Угол винтовой линии |
μ | коэффициент трения между витками |
α | угол резьбы |
мк с | коэффициент трения между головкой болта (или гайки) и зажимной поверхностью |
Обычно предполагается, что значение K равно 0.2, но это значение не следует использовать вслепую. В таблице VI приведены некоторые расчетные значения К для различных коэффициентов трения. Более реалистичным «типичным» значением K было бы 0,15 для стали по стали. Обратите внимание, что µ и µ c не обязательно равны, хотя для расчетных значений в таблице VI использовались одинаковые значения.
Коэффициент трения | Крутящий момент Коэффициент, К | |
---|---|---|
Между резьбой , мкм | Между головкой болта (или гайкой) и зажимной поверхностью , μ c | |
0.![]() | 0,05 | 0,074 |
0,10 | 0,10 | 0,133 |
0,15 | 0,15 | 0,189 |
0,20 | 0,20 | 0,250 |
Методы измерения крутящего момента
Существует ряд методов измерения крутящего момента, начиная с «ощущения» механика и заканчивая установкой тензодатчиков на болт. Точность определения прикладываемых значений крутящего момента зависит от стоимости.Таблицы VII и VIII составлены двумя разными «экспертами», и их номера различаются. Тем не менее, они оба показывают одинаковые тенденции стоимости в зависимости от точности крутящего момента.
Метод измерения предварительного натяга | Точность, % | Относительная стоимость |
---|---|---|
На ощупь (оценка оператора) | ±35 | 1 |
Динамометрический ключ | ±25 | 1.![]() |
Поворот гайки | ±15 | 3 |
Шайбы указатели нагрузки | ±10 | 7 |
Удлинитель крепежа | ± от 3 до 5 | 15 |
Тензодатчики | ±1 | 20 |
Тип инструмента | Управляемый элемент | Типовой диапазон точности, процентов полной шкалы |
---|---|---|
Накидной ключ | Повернуть | 1 Плоский |
Динамометрический ключ для штанг | Крутящий момент | ±3 до 15 |
Поворот | Плоский 1/4 | |
Ударный гайковерт | Крутящий момент | ±от 10 до 30 |
Поворот | ±10 до 20° | |
Гидравлический ключ | Крутящий момент | от ±3 до ±10 |
Поворот | ±5 до 10° | |
Пневматический ключ для редуктора | Крутящий момент | ±10 до ±20 |
Поворот | ±5 до 10° | |
Механический умножитель | Крутящий момент | ±от 5 до 20 |
Поворот | ±2 до 10° | |
Динамометрический ключ с червячной передачей | Крутящий момент | ±0.![]() |
Поворот | ±1 до 5° | |
Цифровой динамометрический ключ | Крутящий момент | ±1/4 до 1 |
Поворот | Плоский 1/4 | |
Ключ с ультразвуковым контролем | Удлинение болта | ±1 до 10 |
Гидравлический натяжитель | Начальное растяжение болта | ±1 до 5 |
Натяжение с компьютерным управлением | Одновременный крутящий момент и поворот | ±0.от 5 до 2 |
Управляемый элемент | Точность предварительного натяга, % | Для максимальной точности |
---|---|---|
Момент затяжки | ±15 до ±30 | Контроль твердости болта, гайки и шайбы, размеров и отделки. Имейте согласованные условия смазки, количества, области применения и типы. |
Поворот | ±15 до ±30 | Используйте постоянный плотный крутящий момент.![]() |
Затяжка и поворот | ±10 до ±25 | Постройте крутящий момент в зависимости от поворота и сравните с полученным ранее набором кривых. Управляйте твердостью болта, отделкой и геометрией. |
Крутящий момент выше предела текучести | от ±3 до ±l0 | Используйте «мягкие» болты и затягивайте их после предела текучести. Используйте постоянный затягивающий крутящий момент. Контролируйте твердость и размеры болтов. |
Растягивающий болт | от ±1 до ±8 | Используйте болты с плоскими параллельными концами. Оставьте датчик включенным во время операции затяжки. Установите датчик на осевой линии болта. |
Каталожные номера
- Стандарты крепежа. 5-е изд., Институт промышленных крепежных изделий, Кливленд, Огайо, 1970 г.
- Баумайстер и др.: Стандартный справочник Марка для инженеров-механиков.
8-е изд., Макгроу-Хилл, 1978.
- Сили, Ф.Б.: Сопротивление материалов. 3-е изд., Wiley & Sons, 1947.
- Шигли, Дж. Э.; и Митчелл, Л.Д.: Проектирование машиностроения. 4-е изд., Макгроу-Хилл, 1983.
- Машиностроение, 19 ноября 1981 г.
Костный ключ — обзор
Величина крутящего момента
Величина усилия, прилагаемого для затягивания резьбового соединения, зависит от того, насколько успешно компоненты остаются соединенными. Крутящие силы вращения винта могут быть измерены в ньютон-сантиметрах (Н-см).Слишком малый крутящий момент приводит к низким усилиям зажима, что увеличивает риск ослабления. Силы зажима на компоненте винта «металл-металл» являются одним из наиболее важных соображений для долгосрочной фиксации винта. Прочность соединения улучшается в большей степени за счет увеличения силы зажима, чем при любом другом условии, непосредственно связанном с винтом. Сила зажима прямо пропорциональна силе, используемой для затягивания винта. Величина предварительного натяга напрямую связана с усилием зажима.
Крутящий момент, прикладываемый к винтовому компоненту, влияет как на сжимающие усилия в резьбе, так и на сжимающее усилие, прикладываемое к головке винта принимающего компонента.Крутящий момент, приложенный к винту, также приводит к растягивающим усилиям внутри охватываемого компонента винта. Силы сжатия и растяжения от сил крутящего момента увеличиваются, поскольку они приложены к наклонной плоскости винтовых компонентов (рис. 28-3). Силы растяжения пытаются удлинить (напрячь) винт, когда приложен достаточный крутящий момент. Деформация (изменение длины, деленная на первоначальную длину) винта также напрямую связана с величиной крутящего момента. Чем выше сила, тем больше напряжение. 27 Слишком большое крутящее усилие вызывает пластическую или необратимую деформацию или необратимое изменение материала, после чего винт становится неизвлекаемым, а дополнительное усилие вызывает разрушение винта. Другими словами, слишком большой крутящий момент приводит к поломке винта или сдиранию компонентов резьбы. Предлагаемая величина крутящего момента для предварительного натяга должна составлять 75% от значения, чтобы достичь остаточной деформации винта и обеспечить предохранительный клапан для резьбового соединения. 28
Величина предварительной нагрузки, прикладываемой к резьбовому соединению, должна быть постоянной и достаточно большой, чтобы вызвать деформацию (деформацию) резьбы.В оригинальной винтовой ретенционной системе Nobelpharma с 1980 по 1990 год для затягивания винтов использовалось только усилие пальца ручной отвертки. Ручная отвертка не может обеспечить постоянное значение крутящего момента. 29,30 В исследовании, проведенном Мишем с участием 136 стоматологов, средний крутящий момент, приложенный к резьбовому соединению с помощью ручной отвертки, составил 11 Н-см и варьировался от 5 до 21 Н-см. Как следствие, расшатывание абатмента и винта в этот период наблюдалось почти в 50% реставраций.
В начале 1990-х для создания этих зажимных усилий использовался динамометрический ключ. Динамометрический ключ использует преимущества рычага для приложения силы. Длина рычага динамометрического ключа может увеличить величину крутящего момента до силы зажима винта более 100 Н-см, что значительно превышает предел упругости материала. Следовательно, ключ имеет предохранительный клапан, который ограничивает значение крутящего момента до постоянного предела. Динамометрический ключ с высоким крутящим моментом растягивает винт абатмента. Эта концепция уменьшила ослабление винтов абатмента до менее чем 16% в течение первого года нагрузки. 31
Для получения постоянного значения крутящего момента требуется динамометрический ключ.Тем не менее, несколько отчетов показали, что динамометрические ключи не совсем точны, и компоненты могут подвергнуться коррозии после многократной обработки в автоклаве, что может увеличить крутящий момент, прилагаемый к системе. 29,32,33 Поэтому рекомендуется автоклавировать ручные динамометрические ключи в открытом положении и проверять динамометрический ключ врачом перед использованием, чтобы убедиться, что детали не замерзли на месте (Рисунок 28-4). Периодически динамометрический ключ должен калиброваться компанией-производителем имплантата. 33
V-образная резьба под углом 30 градусов чаще всего используется для соединения металл-металл системы имплантатов и называется конструкцией резьбы фиксатора . 34 Этот 30-градусный наклон создает сдвигающие нагрузки на металлические компоненты и позволяет растягивать металл во время предварительного натяга, чтобы предотвратить ослабление винтов. Величина крутящего момента, рекомендуемая большинством производителей имплантатов для винтов абатмента, составляет от 20 до 35 Н-см. Однако в литературе сообщалось о большом расхождении значений оптимального крутящего момента, применяемого к винтовым компонентам, в пределах от 12.от 4 до 83,8 Н-см в зависимости от материала и конструкции винта. 35,36
Следует отметить, что, поскольку значение крутящего момента, используемого во время предварительного натяга, меньше, чем остаточная деформация материала винта, растянутая длина винта слегка отскакивает и снижает усилие зажима. Как следствие, предлагается затянуть винт до 75% его остаточной деформации (т. е. 30 Н-см), а затем ослабить и снова затянуть. Через 10 минут винт снова затягивается (после второго раза его нельзя ослаблять).Этот метод отложенного крутящего момента уменьшает количество рецидивов деформации винта. 37
Поскольку компоненты винта взаимодействуют друг с другом, износ (оседание) медленно уменьшает усилие зажима винта, удерживающее компоненты вместе. Как следствие, может быть целесообразно периодически подтягивать винт после каждого периода в несколько лет, особенно у пациентов с более сильными, чем обычно, внешними воздействиями (т. е. с парафункцией).
Стоматолог должен соблюдать осторожность при приложении крутящего момента к винтам, поскольку крутящие усилия также передаются на поверхность раздела кость-тело имплантата (Рис. 28-5).Кость на 65% слабее по отношению к силам сдвига, а крутящий момент оказывает на кость силы сдвига. Величина крутящего момента, необходимая для разрушения интерфейса остеоинтегрированного имплантата, зависит от конструкции имплантата, состояния поверхности и плотности кости, но может быть менее 20 Н-см для мягких типов костей. 38 В связи с этим рекомендуется использование контрторсионной процедуры, особенно в мягких костях.
Простой метод противодействия крутящему моменту заключается в использовании модифицированного кровоостанавливающего зажима для удерживания абатмента, пока динамометрический ключ затягивает винт (Рис. 28-6).Поскольку абатмент взаимодействует с антиротационным компонентом тела имплантата, а абатмент не может вращаться, когда кровоостанавливающий зажим находится в нужном положении, вращательные силы, прилагаемые к винту абатмента, не передаются на поверхность контакта имплантат-кость. 38
Чтобы использовать эту технику противовращения, абатмент должен зацепиться с шестигранной или антиротационной конструкцией имплантата. Чтобы убедиться, что абатмент полностью прилегает к телу имплантата и полностью входит в зацепление с шестигранником или противовращательным элементом тела имплантата, перед использованием динамометрического ключа часто необходимо сделать рентгенограмму, когда платформа имплантата находится ниже мягких тканей.