«Разборка механизмов и дефектация деталей двигателя»
1 апреля 2021 года по плану декады цикловой комиссии преподаватель профессионального цикла Криволапов Олег Николаевич провел открытый урок с обучающимися группы 4-17 специальности 23.02.03 Техническое обслуживание и ремонт автомобильного транспорта по МДК 01.02 Техническое обслуживание и ремонт автомобильного транспорта. Тема практического занятия: «Разборка механизмов и дефектация деталей двигателя».
Образовательная цель: овладение технологией проведения операций по разборке механизмов и дефектации деталей двигателя; формирование у обучающихся умений и навыков по приёмам разборки механизмов и дефектации деталей двигателей.
С целью актуализации опорных знаний преподаватель предложил студентам в форме интерактивной викторины вспомнить основные понятия, относящиеся к выполнению разборки механизмов и дефектации деталей двигателя.
В ходе практического занятия Криволапов О.Н.успешно мотивировал студентов на освоение новых знаний и формирование практических навыков:
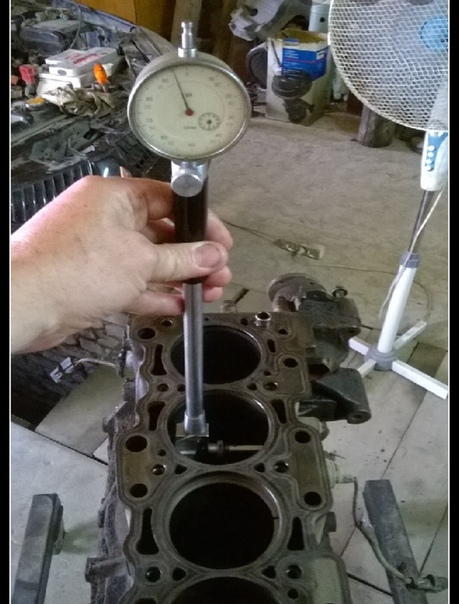
Для выполнения практической работы по разборке механизмов и дефектации деталей двигателя студенты были распределены на подгруппы. Одна подгруппа работала на учебном стенде. Вторая подгруппа выполнила интерактивную практическую работу на образовательной Интернет -платформе Akademia.media/moskow. По итогам практического занятия студенты сделали вывод о пригодности данных элементов КШМ к работе и предложили варианты ремонта. Преподаватель оценил и составил диагностическую таблицу по результатам виртуальной практической работы.
При выполнении практической работы, решении производственных ситуационных задач обучающиеся проявили заинтересованность, познавательную активность, отметили эффективность интерактивных технологий в обучении и важность практических навыков.
Коллеги отметили значительный уровень профессионального опыта преподавателя Криволапов О.Н. и высокую практико-ориентированность учебного занятия, способствующую эффективному формированию профессиональных и общих компетенций обучающихся.

Кузнецова О.В., председатель цикловой комиссии специальности 23.02.03 Техническое обслуживание и ремонт автомобильного транспорта.
- Опубликовано: 16 апреля 2021
- Обновлено: 16 апреля 2021
Дефектация деталей
Очищенные детали подвергают дефектации с целью оценки их технического состояния, выявления дефектов и установления возможности дальнейшего использования, необходимости ремонта или замены. При дефектации выявляют: износы рабочих поверхностей в виде изменений размеров и геометрической формы детали; наличие выкрошиваний, трещин, сколов, пробоин, царапин, рисок, задиров и т. п.; остаточные деформации в виде изгиба, скручивания, коробления; изменение физико-механических свойств в результате воздействия теплоты или среды.
1. Внешний осмотр. Позволяет определить значительную часть дефектов: пробоины, вмятины, явные трещины, сколы, значительные изгибы и скручивания, сорванные резьбы, нарушение сварных, паяных и клеевых соединений, выкрошивания в подшипниках и зубчатых колесах, коррозию и др.

2. Проверка на ощупь. Определяется износ и смятие резьбы на деталях, легкость проворота подшипников качения и цапф вала в подшипниках скольжения, легкость перемещения шестерен по шлицам вала, наличие и относительная величина зазоров сопряженных деталей, плотность неподвижных соединений.
3. Простукивание. Деталь легко остукивают мягким молотком или рукояткой молотка с целью обнаружения трещин, о наличии которых свидетельствует дребезжащий звук.
4. Керосиновая проба. Проводится с целью обнаружения трещины и ее концов. Деталь либо погружают на 15-20 мин в керосин, либо предполагаемое дефектное место смазывают керосином. Затем тщательно протирают и покрывают мелом. Выступающий из трещины керосин увлажнит мел и четко проявит границы трещины.
5. Измерение. С помощью измерительных инструментов и средств определяется величина износа и зазора в сопряженных деталях, отклонение от заданного размера, погрешности формы и расположения поверхностей.
6. Проверка твердости. По результатам замера твердости поверхности детали обнаруживаются изменения, произошедшие в материале детали в процессе ее эксплуатации.

7. Гидравлическое (пневматическое) испытание. Служит для обнаружения трещин и раковин в корпусных деталях. С этой целью в корпусе заглушают все отверстия, кроме одного, через которое нагнетают жидкость под давлением 0,2-6,3 МПа. Течь или запотевание стенок укажет на наличие трещины. Возможно также нагнетание воздуха в корпус, погруженный в воду. Наличие пузырьков воздуха укажет на имеющуюся неплотность.
9. Ультразвуковой способ. Основан на свойстве ультразвуковых волн отражаться от границы двух сред (металла и пустоты в виде трещины, раковины, непровара).

10. Люминесцентный способ. Основан на свойстве некоторых веществ светиться в ультрафиолетовых лучах. На поверхность детали кисточкой или погружением в ванну наносят флюоресцирующий раствор. Через 10—15 мин поверхность протирают, просушивают сжатым воздухом и наносят на нее тонкий слой порошка (углекислого магния, талька, силикагеля), впитывающего жидкость из трещин или пор. После этого деталь осматривают в затемненном помещении в ультрафиолетовых лучах. Свечение люминофора укажет расположение трещины. Используются стационарные и переносные дефектоскопы. Способ применяется в основном для деталей из цветных металлов и неметаллических материалов, так как их контроль магнитным способом невозможен.
По результатам дефектоскопии, детали сортируют на три группы: годные, требующие ремонта и негодные. После сортировки детали маркируют по группам, например, краской разного цвета. Отнесение деталей к той или иной группе определяется величиной износа, технологическими и экономическими соображениями.
Результаты дефектации деталей заносят в ведомость дефектов, являющуюся основным документом для определения объема ремонтно-восстановительных работ и потребности в новых деталях, запасных частях, материалах. Таким образом определяется стоимость ремонта машины.
Ремонт деталей двигателя внутреннего сгорания
Основная цель дефектации двигателя – определение степени износа и/или повреждения всех его деталей. Это необходимо для того, чтобы, с одной стороны, приобрести необходимые запасные части, а с другой – определить те детали, которые могут быть отремонтированы или восстановлены. Ремонт деталей двигателя внутреннего сгорания судов производится после тщательной дефектацииДефектация судовых технических средств по требованиям и правилам эксплуатации.
СодержаниеСвернуть
- Чугунные и стальные фундаментные рамы
- Ремонт деталей двигателя. Разнос дизеля после моточистки
Чугунные и стальные фундаментные рамы
Оси гнезд рамовых подшипников должны лежать на одной прямой. Отклонение между осями двух соседних гнезд допускаются не более 0,02—0,04 мм.
Положение осей в вертикальной плоскости проверяют, перемещая индикатор вдоль верхней плоскости рамы. Для измерений используют шлифованное кольцо, которое поочередно укладывают в каждое гнездо. Соосность гнезд в горизонтальной плоскости проверяют, перемещая индикатор вдоль каждого гнезда в плоскости разъема. Измерительной базой для индикатора служит боковая кромка рамы.
Фундаментная рама судового дизеляОсь гнезд должна быть параллельна верхней плоскости рамы, этим при сборке блока и рамы обеспечивается перпендикулярность осей цилиндров оси коленчатого вала. Отклонение от параллельности допускается не более 0,03 мм на 1 м длины и не более 0,1 мм на всей длине рамы.
Проверку осуществляют перемещением индикатора по верхней плоскости рамы одновременно с проверкой первого требования. Плоскости опорных лап для удобства сборки двигателя на заводском стенде выполняют параллельными верхней плоскости рамы с точностью до 0,05 мм на 1 м.
Торцовые плоскости рамы, если к ним крепятся вспомогательные механизмы, кинематически жестко связанные с коленчатым валом, должны быть перпендикулярны оси гнезд подшипников. Допустимая неточность — 0,05 мм на 1 м длины. Высокие требования предъявляют к прямолинейности верхней плоскости рамы. Отклонения от плоскости (допускаются местные вогнутости) при проверке линейкой, длиной 3—4 м, и щупом — не более 0,05 мм.
Читайте также: Классификация судов и технический надзор
Для контроля прямолинейности начинают широко применять оптические приспособления, в частности оптическую линейку. Проверку плоскостности прямолинейных поверхностей выполняют с помощью линейки (3 м) и щупа в продольном, поперечном и диагональном направлениях.
Цилиндрические поверхности гнезд подшипников проверяют фальшвалом, изготовленным из трубы, толщина стенок которой не менее 10 мм. Шейки фальшвала обрабатывают на круглошлифовальном станке с точностью до 0,01—0,02 мм на диаметр.
Для определения правильности цилиндрической поверхности контрольный вал укладывают в гнезда подшипников и измеряют зазоры щупом в нескольких точках по окружности каждого торца гнезда. Зазор между шейкой вала и поверхностью гнезда не должен превышать 0,03 мм.
Параллельность осей гнезд подшипников верхней плоскости рамы определяют индикатором, устанавливаемым на плоскость рамы с обоих концов фальшвала. Разность замеров не должна превышать 0,1 мм. Положение вертикальных реперов замков относительно оси гнезд удобно проверять калибром (рис. 1). Для этого калибр вставляют в гнездо и устанавливают регулировочным винтом равенство зазоров Δ1 и Δ2.
Затем щупом проверяют боковые зазоры δ1 и δ2. Ширина базы калибра 5 равна номинальной ширине замка. Наличие трещин в корпусе рамы проверяют легким постукиванием слесарного молотка. Дребезжащий звук свидетельствует о дефекте рамы.
Герметичность рамы проверяется наливом воды, температура которой должна быть не ниже 10°С. Продолжительность испытания — 1 ч. Течь и отпотевание не допускаются. Обнаруженную трещину зачищают и осматривают через лупу 5—7-кратного увеличения.
Читайте также: Ремонт деревянных частей корпуса судна и изоляционные работы
Ремонт деталей двигателя предусматривает наличие несоответствий требованиям целостности. При наличии всех вышеуказанных дефектов ремонт фундаментной рамыУстановка и центровка фундаментной рамы выполняют обычно в такой последовательности. Заделывают трещины, пробоины, раковины и изломы. Исправляют или нарезают резьбу под шпильки, крепящие рамовые подшипники. Растачивают гнезда рамовых подшипников. Окрашивают внутренние поверхности масло- и влагостойкой краской.
Трещины в рамах обычно заделывают при помощи сварки без подогрева. По согласованной с Регистром технологии разделывают шов с постановкой винтов и обваркой их специальными электродами. Небольшие трещины заделывают с помощью ввертышей или стяжек.
При наличии более значительных повреждений, вызванных трещинами или разрывами в чугунных деталях, применяют сварку малоуглеродистыми электродами, устанавливая винты и дополнительные связи. Иногда выполняют комбинированное крепление, в котором сочетают усиленные накладки с постановкой связей. Указанные дефекты могут быть устранены с помощью накладок на болтах.
В настоящее время получает широкое распространение способ устранения трещин эпоксидными смолами. Ликвидацию трещин в стальной раме осуществляют сваркой.
Дефекты резьб в отверстиях под шпильки исправляют калибровкой метчиками. Если имеется срыв более трех ниток резьбы, отверстие рассверливают на больший диаметр, а затем после развертывания нарезают резьбы ближайшего размера.
В малых дизелях трещины или изломы в поперечных перегородках или других частях рамы, изготовленной из чугуна, ремонтируют постановкой металлических накладок. Накладки с поперечной перегородкой и ребрами жесткости соединяют призонными болтами.
Количество призонных болтов выбирается в зависимости от площади накладок, которая в свою очередь зависит от протяженности трещин. Шаг болтов должен быть не более 100 мм. К бобышкам накладные планки крепят призонными штифтами.
Если при установке стальных накладок на перегородки рамы требуется, кроме прочности, обеспечить еще и плотность, то между накладкой и стенкой рамы устанавливают тонкую прокладку из листового свинца на свинцовых белилах или сурике.
После обработки и калибровки вертикальных и горизонтальных поверхностей замков гнезд приступают к исправлению цилиндрической поверхности гнезд подшипников фундаментной рамы. Расточку гнезд ведут в сборе с верхними крышками рамовых подшипников.
Работа может выполняться как на горизонтально-расточном станке, так и с помощью переносной борштанги, монтируемой совместно с приводами на обрабатываемой раме.
На рис. 2 показано растачивание гнезд подшипников в раме крупного двигателя на горизонтально-расточном станке. Бор-штанга станка с резцовыми головками направляется подшипниками промежуточных опор, закрепленных на верхних плоскостях. Рама установлена на четырех чугунных призмах. При установке и креплении рамы следят по индикатору, чтобы не было упругой деформации. За установочную базу принимают обработанную верхнюю плоскость рамы.
Рис. 2. Расточка гнезд подшипников фундаментной рамы 1 — борштанга; 2 — кронштейн подшипников; 3 — головка резцоваяПравильное положение борштанги относительно вертикальных реперов замков устанавливают при помощи приспособления — кронштейна подшипников, напоминающего собою калибр. Установку борштанги ведут по концевым подшипникам рамы. Промежуточные опоры для удобства установки борштанги устроены так, что расстояние от оси их подшипника до плоскости прилегания лап равно расстоянию от оси гнезд подшипников рамы до ее верхней базовой поверхности.
Читайте также: Самолет с шасси на воздушной подушке
Благодаря удлиненным овальным отверстиям в лапах промежуточные опоры могут перемещаться в горизонтальной плоскости. При снятых крышках подшипников рамы и промежуточных опор борштангу укладывают вдоль оси рамы. Симметричность положения ее относительно вертикальных реперов замков крайних подшипников устанавливают также калибром.
При отсутствии необходимого оборудования ремонт постелей производят при помощи пустотелого фальшвала, обладающего достаточной жесткостью. Диаметры утолщенных шеек этого вала равны диаметру гнезд рамовых подшипников плюс масляный зазор, а длина шейки равна длине вкладыша подшипника плюс 30 мм. На шейке фальшвала наносят тонкий слой краски, укладывают его на гнезда рамовых-подшипников и проворачивают 2—3 раза на 30—40° в разные стороны.
После удаления фальшвала по количеству оставшихся на постели пятен судят о состоянии поверхностей. Если количество пятен оставшейся краски недостаточно, то путем шабровки постелей добиваются, чтобы количество пятен на 1 см2 было не менее одного-двух и щуп толщиной 0,05 мм не проходил между фальшвалом и постелью. Ось фальшвала должна быть параллельна контрольным плоскостям рамы.
Параллельность оси фальшвала проверяют просадочной скобой, индикатором, установленным на специальном приспособлении. Допустимая непараллельность оси фальшвала относительно контрольных плоскостей не должна превышать 0,05 мм на 1 м длины вала. По уложенному в постели фальшвалу пришабривают крышки рамовых подшипников.
Постель промывают и вытирают насухо, наносят тонкий слой краски на каждую ее поверхность, укладывают вкладыш в постель, плотно прижимают и перемещают его по окружности на 20—25 мм в каждую сторону 2—3 раза. Затем вкладыш вынимают из постели и осматривают. Места, которыми вкладыш не касается окрашенной поверхности постели, остаются чистыми от краски, а места, касающиеся поверхности постели, окрашиваются краской.
Снимая излишки окрашенного металла сначала напильником, а потом шабером, добиваются плотного прилегания затылка вкладыша к поверхности постели. О качестве пригонки поверхности судят по размерам пятен и равномерности их распределения на затылочной стороне вкладыша. При хорошем прилегании поверхностей на площади 1 см2 должно быть не менее одного-двух пятен, а щуп 0,03 мм не должен входить в плоскость разъема вкладыша и постели на глубину более 5—10 мм.
В процессе перезаливки вкладыши коробятся и плоскости разъема сдвигаются внутрь, нарушается параллельность плоскостей разъема и образующей наружной поверхности вкладыша. Плоскости разъема пришабривают по плите, проверяют непараллельность затылочной части вкладыша по отношению к плоскости разъема, которая не должна превышать 0,01 мм на 100 мм длины вкладыша. Вследствие деформации вкладышей необходимо проверить пригонкуТехнологические процессы разборки и сборки механизмов судна их затылочной поверхности по постелям (гнездам) фундаментной рамы.
Ремонт деталей двигателя. Разнос дизеля после моточистки
Сноски
Sea-Man
Методы дефектации деталей, узлов судовых дизелей и механизмов (2-е издание, переработанное и дополненное)
Изложенный материал по методу производства дефектации и соответствующего оформления дает возможность эксплуатационникам принятие решения о методе и объеме ремонта детали, узла двигателя или всего двигателя.
В данном пособии, наряду с технологией дефектации, изложены материалы по мерительному инструменту, использующемуся при производстве дефектации.
Поскольку для каждого типа двигателей установлены свои зазоры, допуски и размеры, в книге приводится справочный материал, применяемый для наиболее распространенных типов судовых двигателей. Только при отсутствии руководящих документов, следует пользоваться усредненными нормами, приведенными в настоящей книге.
Книга предназначена для всех судовых механиков, эксплуатирующих судовые дизельные установки, а также может быть полезна учащимся морских учебных заведений по судомеханической специальности.
Содержание
Предисловие
Раздел 1 Дефектация механизмов, периодичность профилактических осмотров, гидравлические затяжные приспособления
1.1. Общая часть
1.2. Метод дефектации визуальным наружным осмотром
1.4. Применение измерительного инструмента и приборов
1.

1.6. Периодичность технического обслуживания дизелей
1.6.1. Работы техобслуживания, проводимые ежедневно
1.6.2. Работы техобслуживания, проводимые через каждые 500 часов работы двигателя
1.6.3. Работы техобслуживания, проводимые через каждые 1500 часов работы двигателя
1.6.4. Работы техобслуживания, проводимые через каждые 3000 часов работы двигателя
1.6.5. Работы техобслуживания, проводимые через каждые 3000-6000 часов работы двигателя
1.6.6. Работы техобслуживания, проводимые через каждые 6000-8000 часов работы двигателя
1.7. Освидетельствование деталей и узлов дизеля
1.7.1. Цилиндры и втулки рабочих цилиндров
1.7.2. Поршни и поршневые кольца
1.7.3. Поршневые пальцы, цапфы поперечин, штоки, шатуны
1.7.4. Параллели и ползуны крецкопфных дизелей
1.7.5. Вкладыши головных, мотылевых и рамовых подшипников
1.7.6. Коленчатые валы
1.7.7. Проверка высоты камеры сжатия и установка крышки цилиндра
1.
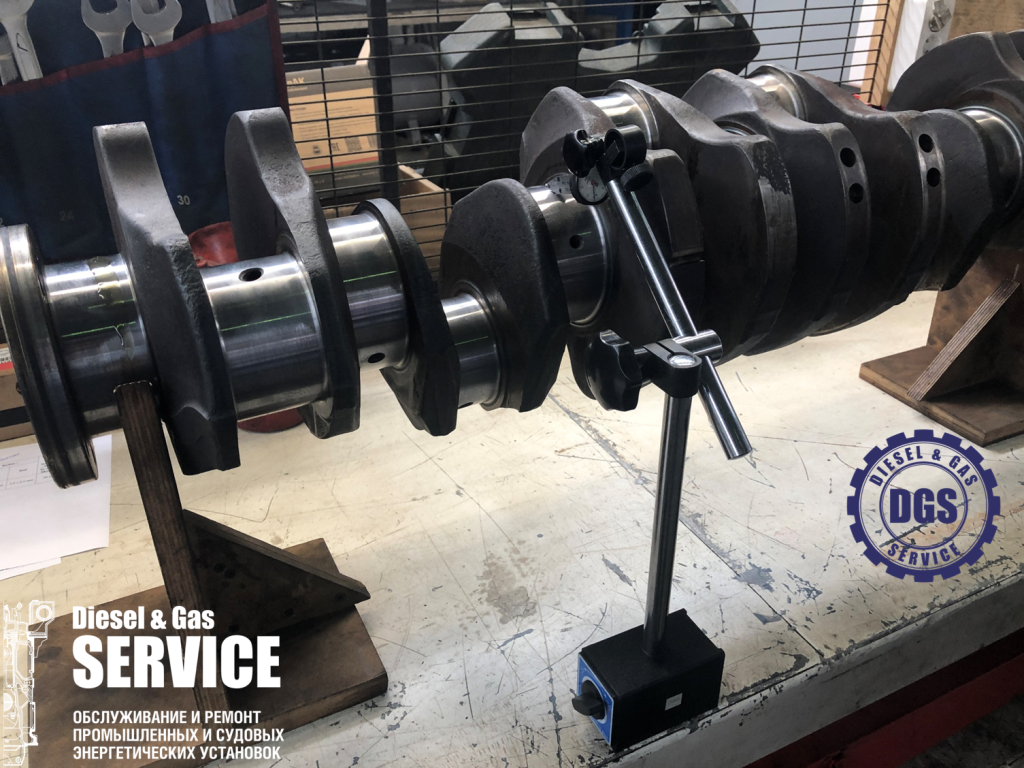
1.7.9. Проверка положения ползунам параллели
1.8. Гидравлические затяжные приспособления для двигателя Зульцер RTA
1.8.1. Гидравлическое затяжное приспособление для затяжки фундаментных болтов и опор генераторов № 94950
1.8.2. Гидравлическое затяжное приспособление для затяжки анкерных связей
1.8.3. Гидравлическое приспособление для затяжки податливых болтов крышек цилиндров. № 94215
1.8.4. Гидравлическое приспособление для затяжки гайки штока выпускного клапана № 94251
1.8.6. Гидравлическое приспособление для затяжки нижних болтов шатуна
1.8.7. Гидравлическое приспособление для затяжки податливых болтов корпуса клапана. № 94252
1.8.8. Гидравлическое приспособление для демонтажа седла выпускного клапана. № 94260
1.8.9. Гидравлическое приспособление для распределительного вала №94424
1.9. Общая инструкция по использованию гидравлических приспособлений
1.
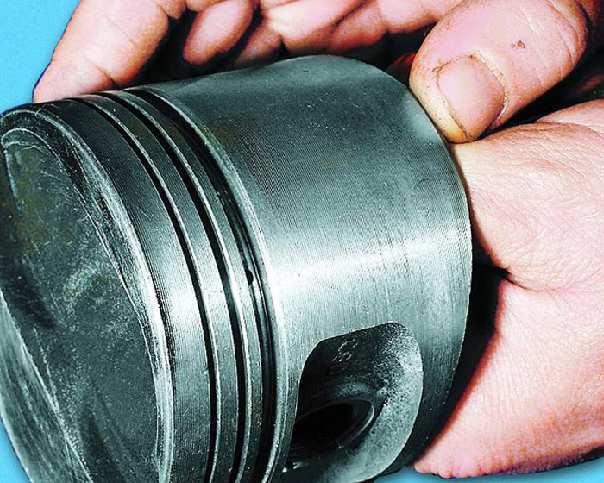
1.11. Порядок применения гидравлического приспособления при отдаче гаек
1.12. Проверка затяжки анкерных связей
Раздел 2 Дефектация и диагностика деталей дизеля RTA при ревизии
2.1. Диагностика цилиндровой втулки дизеля RTA 5863
2.2. Удаление поршня из цилиндровой втулки, разборка, дефектация поршневого узла
2.3. Проверка выгорания днища поршня с помощью шаблона
2.4. Ревизия сальника ходовых труб охлаждения поршня
2.5. Монтаж сальников ходовых труб
2.6. Сальник поршневого штока
2.7. Крейцкопф и ползун
2.8. Смазка крейцкопфа
2.9. Шатун и подшипники шатуна
2.10. Рамовый и упорный подшипники
2.11. Реверсивный серводвигатель распределительных топливных кулачков
Раздел 3 Ревизия, дефектация деталей дизеля типа MAN B&W 6L60MC
3.1. Технология удаления поршня из цилиндра и его разборка
3.2. Ревизия, дефектация поршневой группы, замеры и составление технологических карт дефектации
3.

3.4. Разборка, дефектация цилиндровой втулки, составление технологической карты дефектации
3.5. Конструкция цилиндровой втулки и ее замеры, составление технологической карты дефектации
3.6. Подшипники двигателей MAN B&W: головной, мотылевый, рамовый
3.7. Рамовые подшипники
3.8. Замер раскепа коленчатого вала дизеля
3.9. Сальник поршневого штока
3.10. Привод распредвала
3.11. Способ определения вытяжки цепи распредвала и дефектов зубьев шестерен
3.12. Ревизия, дефектация выпускных клапанов дизелей
3.13. Проверка положения цилиндропоршневой группы центровка двигателя MAN B&W
Раздел 4 Вспомогательные двигатели дизельгенераторов
4.1. Цилиндровые втулки дизельгенераторов
4.2. Поршни и поршневые кольца
4.3. Ревизия и дефектация поршней
4.4. Втулка и палец головного подшипника
4.5. Замеры пальца головного подшипника
4.6. Дефектация и ревизия деталей головного подшипника
4.
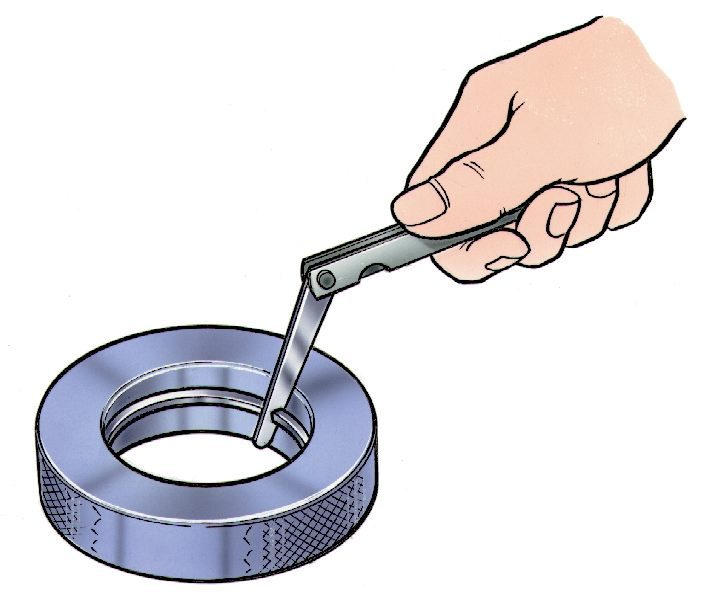
4.8. Выпрессовка и запрессовка подшипниковой втулки
4.9. Конструктивные особенности мотылевых и рамовых подшипников четырехтактных двигателей
4.10. Определение масляного зазора мотылевого подшипника
4.11. Определение масляного зазора по разности размеров внутреннего диаметра подшипника и диаметра мотылевой шейки
4.12. Определение зазоров в головном и мотылевом подшипнике с помощью прибора ПЗ-1М1
4.13. Замер масляного зазора мотылевого подшипника
4.14. Составление технологической карты замера внутреннего диаметра подшипника и мотылевой шейки, расчет масляного зазора
4.15. Дефектация подшипников
4.15.1. Трещины в подшипниках
4.15.2. Полное разрушение вкладыша
4.16. Результаты обмера рамовых и мотылевых шеек
4.17. Замер раскепов
4.18. Распредвал — ревизия кулачных шайб, замер зазоров в подшипниках, составление технологических карт дефектации
4.19. Ревизия и дефектация распредвала
4.20. Замер зазоров в подшипниках распредвала
4.
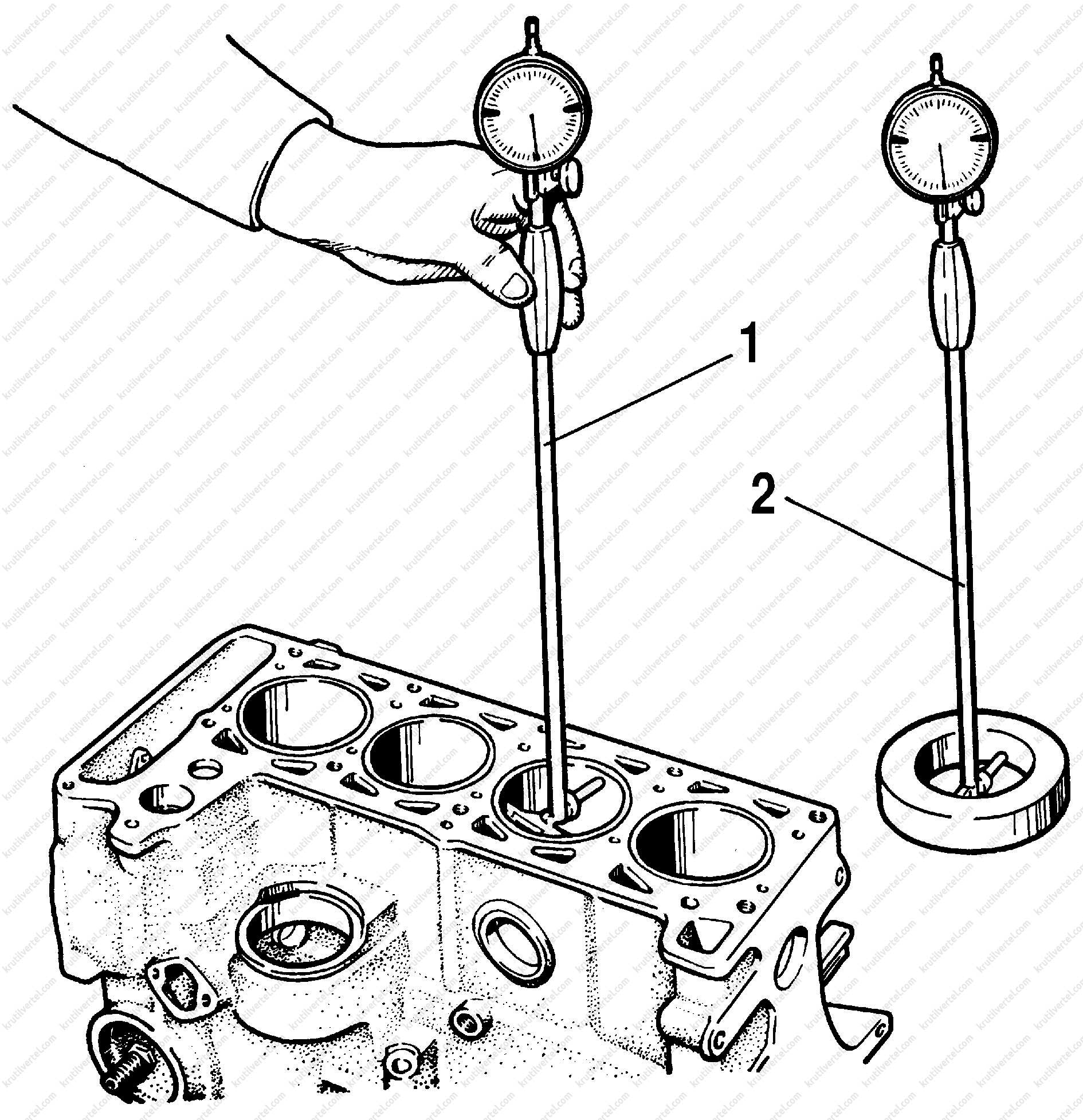
4.22. Осмотр шестерен привода
4.23. Возможные повреждения зубьев шестерен
4.23.1. Замер зазоров двумя индикаторами
4.23.2. Замер зазоров индикатором либо щупом
4.24.3. Замер зазоров свинцовой выжимкой
4.25. Газораспределение, технологическая карта замеров впускных и выпускных клапанов
4.26. Клапана впускные и выпускные: дефектация и методы устранения повреждений
4.27. Ревизия и дефектация клапанов
4.28. Привод клапанов: ревизия и дефектация
4.29. Коленчатый вал дизеля — технология укладки
4.30. Ревизия буферных колодок маховика коленчатого вала
4.31. Осмотр буферных колодок
4.32. Ревизия и дефектация коленчатого вала
Раздел 5 Ревизия и дефектация турбокомпрессоров
5.1. Дефектация роторов турбокомпрессоров
5.2. Контактное кольцевое уплотнение
5.3. Лопатки рабочего колеса газовой турбины
5.4. Дефектация подшипников
5.5. Подшипники качения
5.6. Турбокомпрессор типа VTR 454,564,714
5.
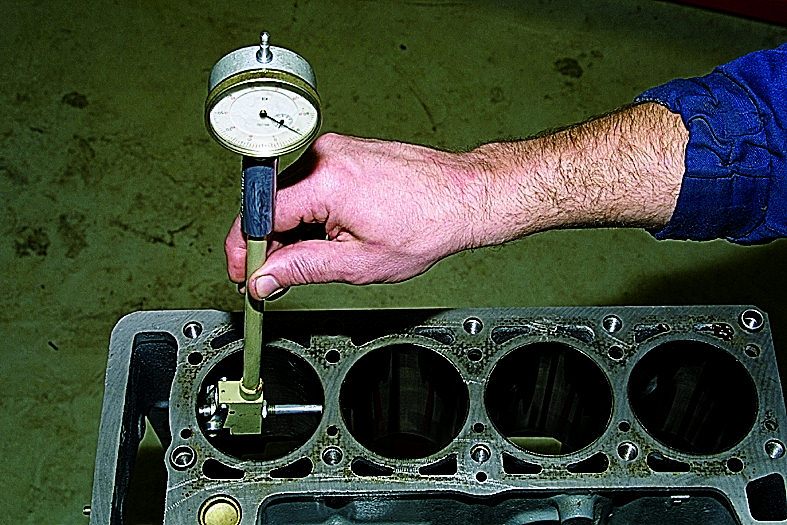
5.7. Контрольные зазоры в турбокомпрессорах типов -А-,-Б-,-В
Раздел 6 Дефектация и ремонт воздушных компрессоров
6.1. Дефектация и ремонт воздушных компрессоров
6.2. Дефектация самодействующих клапанов судовых поршневых компрессоров
6.3. Дефекты деталей и узлов воздушных компрессоров. Способы их устранения
Раздел 7 Дефектация гидравлической части электронасосов
Раздел 8. Приложения
Нормы зазоров в основных узлах и допускаемых износов основных деталей дизелей
8.1. Наибольший допустимый износ втулок цилиндров дизеля
8.2. Наибольший допустимый износ поршней цилиндров и поршневых штоков
8.3. Наибольший допустимый износ штока поршня
8.3. Диаметральные монтажные зазоры между поршнем и цилиндром
8.4. Результаты обмера рамовых и мотылевых шеек
8.5. Наибольший допустимый износ шеек коленчатого вала
8.6. Диаметральные зазоры в рамовых и мотылевых подшипниках
8.

8.8. Диаметральные зазоры в головных подшипниках
8.10. Крейцкопф и ползун. Монтажные и предельно допустимые зазоры между параллелями и ползунами
8.11. Замеры раскепов коленчатого вала
Литература
§ 15. Дефектовщик авиационной техники (6-й разряд) / КонсультантПлюс
§ 15. Дефектовщик авиационной техники
6-й разряд
Характеристика работ. Дефектация технического состояния и определение вида ремонта летательных аппаратов среднего типа. Дефектация сложных и мощных газотурбинньх двигателей. Установление причин возникновения дефектов деталей, узлов, агрегатов, приборов, оборудования и систем вооружения летательных аппаратов среднего типа, выбор способов их восстановления. Проверка и настройка применяемых контрольно-измерительного инструмента, приборов и аппаратуры. Выбор способов дефектации деталей, агрегатов и систем вооружения летательных аппаратов среднего типа. Подбор взаимозаменяемых деталей по размерам, упругости, весу и частотам собственных колебаний с применением ЭВМ. Проведение контроля несъемных деталей неразрушающими методами контроля на изделии при проведении ремонта летательного аппарата. Проведение микрометрического обмера сложных и точных несъемных деталей. Заполнение карточек отказа и дефектов изделий летательных аппаратов среднего типа. Проверка формуляров двигателей. Выписка и оформление карт дефектации.
Должен знать: виды и методы ремонта авиационной техники; характерные и нехарактерные дефекты деталей летательных аппаратов среднего типа, в том числе из пластических масс и других неметаллических материалов, причины их возникновения и способы устранения; основы технологии механической обработки металлов; технологию сварочных, сборочно-клепальных и клеевых работ, правила наладки точных измерительных инструментов и приборов; оптимальные способы применения неразрушающих методов контроля деталей летательных аппаратов среднего типа; конструктивные отличия изделий летательных аппаратов среднего типа по сериям их изготовления; требования к сертифицированным изделиям летательных аппаратов среднего типа; основы механики, электротехники, электроники, радиотехники, баллистики, метрологии.
Требуется среднее профессиональное образование.
Примеры работ
1. Агрегаты и узлы управления летательного аппарата — дефектация.
2. Агрегаты топливной автоматики типа ЦИА, ИМТ, ТППО — дефектация с применением измерительных и оптических приборов повышенной точности.
3. Агрегаты топливной системы типа РСФ, насосы топливные — дефектация.
4. Аппаратура радиолокационная — проверка и дефектация.
5. Блоки электронные, электрические, механические пилотажных приборов — комплексная дефектация.
6. Бортовые вычислители — дефектация.
7. Винты воздушные, соосные — дефектация.
8. Гермовыводы управления и штурвальной колонки летательных аппаратов среднего типа — дефектация.
9. Замки шасси и грузолюков — дефектация.
10. Зеркала антенн и облучателей радиолокационной аппаратуры — проверка согласно техническим условиям.
11. Камеры сгорания — осмотр с прибором ПДК.
12. Корпусы форсажных диффузоров, жаровые трубы — дефектация.
13. Пары золотниковые, плунжеры топливных насосов — дефектация.
14. Подшипники опор турбокомпрессоров ГТД — подсчет радиальных и осевых зазоров, посадок.
15. Разъемы штепсельные — дефектация.
16. Редукторы вертолетов — дефектация.
17. Регуляторы оборотов, датчики давления масла, топлива, сигнализации — дефектация.
18. Узлы двигателей — динамическая балансировка при дефектации.
19. Устройства силовые вспомогательные, неразъемные детали ВСУ и двигателя — дефектация.
20. Центропланы, гермокабины, фюзеляжи, мотогондолы, силовые элементы конструкций планера — дефектация.
21. Электроаппаратура радиоцепей — дефектация.
Открыть полный текст документа
Дефектация деталей и сопряжений — лекция
Страница 1 из 2
РМО.
Тема: Лекция о дефектации деталей и сопряжений.
План:
1.Сущность и основные задачи дефектации.
2. Классификация дефектов типовых деталей.
3. Методы дефектации. Оборудование и инструмент для дефектации.
4.Обнаружение скрытых дефектов.
1.Сущность, задачи и методы дефектации.
Дефектация — это процесс выявления состояния деталей и сопряжений путем сравнения фактических показателей с данными технической документации, где приведены нормальные, допустимые и предельные значения размеров деталей, зазоров и натягов сопряжений, а также отклонения от нормы и от взаимного расположения поверхностей деталей и другие параметры их состояния.
Основная задача дефектовочных работ – не пропустить на сборку детали, ресурс которых исчерпан или меньше планового межремонтного срока, и не выбраковать годные без ремонта детали.
Организация работ по дефектации.
В достаточно крупных и специализированных ремонтных предприятиях для выполнения работ по дефектации создаются специальные участки.
Например:
Рис. 1. План размещения оборудования в отделении дефектовки деталей специализированного ремонтного предприятия (годовая программа ремонта 400—500 тракторов):
/ — рольганг; 2 — стол для дефектовки средних и мелких деталей; 3 — стол для дефектовки крупных деталей; 4 — ящик для утиля; 5 — стеллаж; 6 — шкаф для инструмента; 7 — конторский стол; 8 — кран-балка; 9 — стол для комплектования узлов.
Как видно из плана, отделение дефектовки включено в поточную технологическую линию (конвейер). Детали поступают из разборочно-моечного отделения и после дефектации направляются в отделение комплектования.
Рабочие места в отделениях дефектовки, по мере необходимости, оснащаются специальным оборудованием и инструментом. Примерный перечень оборудования приведен в таблице 1.
Таблица 1.Обобрудование участка дефектации.
Оборудование |
Тип, чертежная модель |
Габаритные размеры в плане, мм |
Стол для дефектации деталей |
ОРГ — 1468-0 1-090А |
2400X800 |
Стол для дефектации металлоизделий (метизов) |
70-7825-1505 |
1160X695 |
Стол монтажный металлический |
ОРГ — 1468-0 1-080 А |
1200X800 |
Шкаф с набором универсаль-ных инструментов |
ОРГ-1661 |
615X750 |
Шкаф для материалов и измерительного инструмента |
ОРГ — 1468-07 |
860X360 |
Подставка для корпусных деталей |
— |
966X636 |
Контейнер для выбракованных Деталей |
ОРГ-1598 |
885Х 865 |
Контейнер для выбракован-ных подшипников |
— |
700Х 570 |
Стол для поверочной плиты |
3702-08А |
966X636 |
Автоматическая справочная установка |
АСУ-50 |
1000X900 |
Центры универсальные для проверки валов |
2ЖМ-00-00 |
1566X666 |
Дефектоскоп магнитный |
УМД-Э-2500 или МД-50П или ПМД-70 |
1800X700 1000X780 620Х 500 |
Стенд для испытания на герметичность головок блоков цилиндров ДВС. |
КИ-1040 |
1080X900 |
Создание специальных отделений и специализированных рабочих мест позволяет увеличить производительность труда и улучшить качество работы. Пример рабочего места для дефектации крепежных деталей приведен на рисунке 2.
Рис. 2. Столы для дефектовки крепежных деталей
Рабочие места для дефектовки деталей оснащаются набором измерительного инструмента, контрольных приспособлений и приборов.
В мастерских общего назначения (в мастерских аграрных предприятий) годовая программа ремонта (годовой объем ремонтно-технических работ) недостаточен для создания поточных технологических линий. В таких мастерских дефектовка выполняется на тех рабочих местах, где производится ремонт агрегатов или восстановление деталей. При этом, необходимый для дефектации инструмент, приспособления и приборы могут постоянно находиться на данном рабочем месте, например на участках ремонта топливной аппаратуры, электрооборудования, двигателей и т. п., или в инструментальной кладовой, например инструмент, необходимый для дефектовки деталей трансмиссии, ходовой части и других агрегатов, ремонт которых выполняется в ремонтно-монтажном отделении.
В процессе дефектации все детали разделяют на Пять групп и Маркируют их краской Определенного цвета:
— годные, параметры которых находятся в пределах, допускаемых для использования с деталями, бывшими в эксплуатации или новыми;
— годные, параметры которых находятся в пределах,
допускаемых для работы только с новыми деталями;
— утратившие работоспособность, которую можно восстановить в условиях данного предприятия;
— утратившие работоспособность, ремонт и восстановление которых возможны только на специализированных предприятиях;
— те, которые по своему состоянию не могут быть использованы в дальнейшем; их сдают во «Вторчермет».
Методы дефектации Могут быть классифицированы в соответствии со схемой, изображенной на рисунке 3.
Рис. Методы дефектации деталей и сопряжений.
Осмотр — наиболее распространенный метод дефектации для выявления наружных повреждений деталей:
— деформации, трещины, обломы, выкрашивание, прогар;
— отложения, раковины, задиры, царапины, повреждение покрытий, коррозия;
— негерметичность и др.
Осмотр возможен как Невооруженным глазом, так и с помощью Оптических средств: простых и бинокулярных луп, микроскопов.
Простукивание — используется для определения Плотности посадки шпилек, нарушения сплошности (целостности) деталей.
Метод основан на изменении тона звучания детали при нанесении по ней легкого удара молотком.
Звучание чистое — посадка плотная и деталь сплошная.
Звук глухой, дребезжащий – целостность детали нарушена.
Опробование вручную и проверка на ощупь – позволяет определить:
— наличие зазора,
— плавность вращения,
— перемещение детали,
— свободный ход рычагов,
— эластичность резинотехнических деталей,
— наличие местного износа.
Органолептические методы в большинстве случаев не позволяют сделать окончательный вывод о состоянии детали, поскольку имеют Субъективный характер.
Измерение размеров.
Порядок измерения, применяемый инструмент и приспособления, место и число замеров оговаривается в соответствующих технологических картах.
Для выполнения измерений используются универсальные и специальные измерительные инструменты и приспособления, а так же контрольные средства.
Например:
— универсальные инструменты: штангенциркуль (рис.4.), микрометр (рис.5.) , нутромер и т. п.;
— специальные – штангенрейсмус, штангензубомер (рис. 6), и др.;
— контрольные средства – калибры, шаблоны, щупы, поверочные плиты, угольники и др. (рис.7 — 15).
Калибры для контроля шлицевых соединений.
Калибры для контроля отверстий.
Калибры для контроля валов.
Калибры для контроля конусных поверхностей.
Калибры для контроля длин.
Калибры для контроля расположения отверстий.
Рис. Калибры для контроля соосности отверстий.
Рис. Регулируемые калибры-скобы для контроля болтов.
Рис. 15. Использование калибров.
Капиллярные методы — основаны на способности некоторых жидкостей с хорошей смачиваемостью проникать в мельчайшие трещины.
К этим методам относятся люминесцентная и цветная дефектоскопии (метод красок), применяемые для выявления поверхностных трещин в деталях, изготовленных из магнитных и немагнитных материалов.
Магнитная дефектоскопия применяется для обнаружения наружных скрытых дефектов (трещин) в деталях, изготовленных из стали и серого чугуна. Метод основан на появлении магнитного поля рассеивания вокруг дефекта при прохождении магнитно-силовых линий через деталь и концентрации ферромагнитного порошка по краям дефектного участка.
Для намагничивания деталей применяют стационарные и переносные магнитные дефектоскопы (М-217, 77МД-1, 77МД-ЗМ).
Трансформатор. Схема магнитного дефектоскопа.
Ультразвуковая дефектоскопия основана на способности ультра-звуковых колебаний распространяться в материале на большую глубину в виде направленных пучков и отражаться от дефектного участка вследствие разного изменения акустического сопротивления среды. В практике ремонтного производства используются дефектоскопы, работающие по теневому методу и методу отражения.
Рис. Схема ультразвукового дефектоскопа:
А — работающего по теневому методу:
1— ультразвуковой генератор; 2 — излучатель; 3 — деталь;
4 — Ультразвуковые волны; 5 — приемник; 6 — дефект; 7 — индикатор;
Б — Работающего по методу отражения: 1— контролируемое изделие; 2 — приемная пластина; 3 — Элемент; 4 — усилитель; 5 — электронно-лучевая трубка; 6 —генератор; 7— генератор развертки; 8 — дефект; А — начальный импульс; В — отраженный импульс; С — Донный сигнал.
Дефектация и восстановление деталей двигателя КАМАЗ своими руками, руководство, неисправности, фото, последовательность, запчасти
Блок цилиндров испытывают на стенде 470-086 для обнаружения пробоин и трещин, проходящих через каналы масляной магистрали и стенки водяной рубашки. Герметичность каналов и водяной рубашки проверяют сжатым воздухом под давлением 0,3…0,4 МПа (3…4 кгс/см2). При утечке воздуха блок цилиндров бракуют. При наличии устанавливаемых визуальным контролем пробоин стенок блока, трещин и кавитационных разрушений в зоне уплотнительных колец гильз цилиндров, входящих в канавки, блок бракуют. Если указанные разрушения не входят в канавки, их обрабатывают под установку сдвоенного кольца. Коробление поверхности сопряжения с головками цилиндров устанавливают с помощью металлической поверочной линейки и щупов. При неплоскостности поверхности более 0,08 мм или наличии на ней раковин поверхность обрабатывают до устранения дефекта.
При задирах или износе втулок под распределительный вал до диаметра более 54,05 мм втулки заменяют. Ослабление посадок втулок обнаруживают при легких ударах медным молотком. Этот дефект устраняют обработкой посадочных отверстий поп втулки до ремонтного размера 59,0 (+0,03 мм), а если диаметр отверстий больше указанного размера, блок бракуют.
При износе паза под выступ упорного полукольца задней опоры по ширине до размера более 14,2 мм блок бракуют. Торцевую поверхность задней опоры коленчатого вала под полукольца упорного подшипника, изношенную до размера менее 27,97 мм, обрабатывают до ремонтного размера 27,4 (—0,021 мм), а при размере менее 27,37 мм блок цилиндров бракуют.
При деформации или износе верхнего посадочного отверстия под гильзу цилиндра до диаметра более 137,58 мм, износе нижних посадочных поясков под гильзу до диаметра более 134,1 мм указанные поверхности обрабатывают до ремонтного размера: верхнее отверстие — до 138,5 (+0,04 мм), нижние пояски — до 135 (+0,04мм).

Гильзу цилиндра бракуют при наличии трещин или обломов, задиров и выбоин на посадочных поверхностях, рисках или задирах на рабочей поверхности, а также при износе: рабочей поверхности — до диаметра более 120,03 мм; верхнего посадочного пояска — до диаметра менее 137,40 мм; нижнего посадочного пояска — до диаметра менее 133,90 мм.
Крышку блока переднюю бракуют при наличии обломов и трещин, захватывающих поверхности под подшипник, манжету или масляные каналы, а также при износе отверстия под подшипник до диаметра более 110,05 мм.
Картер маховика бракуют при наличии обломов или трещин, а также износе отверстия под манжету до диаметра более 130,15 мм.
Маховик бракуют при наличии обломов или трещин на выступах и на зубчатом ободе, износе пазов под шипы ведущего и нажимного дисков сцепления до размера более 60,2 мм, износе отверстия под установочный штифт до диаметра более 12,18 мм.

Направляющую толкателей бракуют при наличии обломов или трещин, а также износе отверстия под толкатели до диаметра более 22,05 мм.
Толкатель клапана бракуют при наличии трещин или выкрашивания, износе стержня до диаметра d (рис. 5.28) менее 21,78 мм, неравномерном износе или выкрашивании рабочей поверхности. Размер а до шарика диаметром 17,463 мм должен быть не менее 24,3 мм. Толкатель клапана КАМАЗ (рис. 5.28) Штангу толкателя проверяют на изгиб с помощью поверочной плиты и набора щупов. Допуск неплоскостности образующей стержня 0,6 мм. При большем изгибе деталь бракуют. Ослабление посадки наконечника в стержне штанги определяют от руки. При наличии дефекта следует обжать наконечник. Износ сферических поверхностей верхнего и нижнего наконечников проверяют на краску.

Распределительный вал бракуют при наличии обломов или трещин, а также биении средних опорных шеек относительно крайних более 0,035 мм. Схема измерения поверхностей кулачков распределительного вала КАМАЗ (рис. 5.29) При размере а (рис. 5.29) кулачков менее 35,45 мм или размере b менее 44,00 мм распределительный вал бракуют. При износе опорных шеек до диаметра менее 53,88 мм их обрабатывают до ремонтного размера:
I — 53,75 (-0,085)(-0,105) мм;
II — 53,50 (-0,085)(-0,105)мм:
III — 53,25 (-0,085)(-0,105)мм.
При диаметре опорных шеек менее 53,145 мм распределительный вал бракуют. При износе пятой опорной шейки до диаметра менее 41,92 мм ее обрабатывают до ремонтного размера 41,75 (-0,05)(-0,07), а при ее диаметре менее 41,68 мм распределительный вал бракуют. Его также бракуют при износе шейки под шестерню до диаметра менее 35,01 мм и износе шпоночного паза по ширине до размера менее 5,01 мм.

Корпус подшипника распределительного вала в сборе бракуют при наличии обломов или трещин и ослаблении посадки втулки, устанавливаемом при легких ударах медным молотком. При износе отверстия во втулке до диаметра более 42,02 мм ее заменяют и обрабатывают под начальный (42+ 0,015 мм) или ремонтный (41 +0,015 мм) размер в зависимости от размера шейки вала.
Шестерню распределительного вала бракуют при наличии разрушения рабочих поверхностей зубьев, износе зубьев по толщине до размера менее 4,35 мм, износе отверстия под шейку вала до диаметра более 35,01 мм. При износе шпоночного паза по ширине до размера более 5,10 мм фрезеруют новый паз под углом 180° к изношенному либо выбраковывают шестерню.
Коллектор выпускной бракуют при наличии обломов фланцев крепления или трещин. При износе отверстия под соединительную втулку до диаметра более 52,03 мм его обрабатывают до ремонтного размера 53 (+0,03)мм, при значении более 53,03 мм коллектор бракуют. Коробление поверхности фланца крепления трубы глушителя устанавливают на поверочной плите с помощью щупа.

Втулку соединительную выпускного коллектора бракуют при наличии обломов или трещин. При износе посадочных поверхностей втулки до диаметра менее 52,0 мм, а втулки ремонтного размера — до диаметра менее 53,00 мм втулку бракуют.
Патрубок выпускного коллектора бракуют при наличии обломов или трещин. При износе отверстия под втулку до диаметра более 52,07 мм его обрабатывают до ремонтного размера 53 (+0,046)мм, при значении более 53,07 мм патрубок бракуют.
Масляный поддон картера блока цилиндров восстанавливают сваркой при наличии пробоин или трещин и нарушении сварных соединений. Коробление поверхности прилегания к блоку цилиндров устанавливают на поверочной плите с помощью щупов. Допуск неплоскостности поверхности 2,0 мм. При большем значении, а также при наличии вмятин на стенках и перегородках поддон правят.
Шестерню ведущую привода распределительного вала в сборе с промежуточной шестерней бракуют при наличии выкрашивания рабочих поверхностей зубьев, износе зубьев по толщине до размера менее 4,35 мм (у обеих шестерен), износе посадочного отверстия под подшипник до диаметра более 62,05 мм.

Ось ведущей шестерни привода распределительного вала бракуют при наличии обломов или трещин и износе шейки под подшипник по наружному диаметру до размера менее 29,95 мм.
Вал ведомой шестерни привода ТНВД бракуют при наличии обломов или трещин, износе посадочных поверхностей под подшипники до размера менее 24,99 мм (наружного подшипника) и 34,99 мм (внутреннего), при задирах или износе шеек вала под сальники до диаметра менее 19,8 мм. При износе шпоночного паза по ширине до размера более 5,1 мм фрезеруют новый паз под углом 180° к изношенному либо выбраковывают вал. Износ конической поверхности определяют калибром с конусностью 1:5 при диаметре конуса 18 мм в плоскости А на длине b = 91 ± 0,23 мм (рис. 5.30). Схема измерения износа конической поверхности вала ведомой шестерни привода ТНВД КАМАЗ (рис. 5.30) При смещении торца калибра относительно большого диаметра конуса более 1,5 мм вал бракуют.
Корпус переднего подшипника бракуют при наличии обломов или трещин, износе отверстия под подшипник до размера более 62,06 мм и износе наружной посадочной поверхности до диаметра менее 74,95 мм.
Корпус заднего подшипника бракуют при наличии обломов или трещин, износе отверстия под подшипник до размера более 72,06 мм и износе отверстия под манжету до диаметра более 42,1 мм.
Передний фланец ведущей полу муфты привода ТНВД бракуют при наличии обломов или трещин, износе отверстия под ведущую полумуфту до диаметра более 22,03 мм и износе шпоночного паза по ширине до размера более 5,1 мм.
Задний фланец ведущей полумуфты привода ТНВД бракуют при наличии обломов или трещин и износе шпоночного паза по ширине до размера более 5,1 мм.
Полумуфту ведущую привода ТНВД бракуют при наличии обломов или трещин и износе шейки под фланец ведущей полумуфты до диаметра менее 21,857 мм. При износе шпоночного паза по ширине до размера более 5,1 мм фрезеруют новый паз под углом 180° к изношенному либо выбраковывают полумуфту.
Коллектор впускной правый и левый бракуют при наличии обломов или трещин. Коробление сопрягаемых поверхностей устанавливают на поверочной плите с помощью щупов. Допуск неплоскостности поверхностей 0,15 мм. При большем значении поверхности обрабатывают до устранения дефекта, не допуская уменьшения толщины привалочных плоскостей до размера менее 8 мм. При невозможности устранения дефекта коллектор бракуют.
Патрубок соединительный впускных коллекторов бракуют при наличии обломов или трещин. Коробление поверхностей фланцев крепления патрубка к впускным коллекторам устанавливают с помощью металлической поверочной линейки и щупов. Допуск неплоскостности фланцев 0,15 мм. При большем значении фланцы обрабатывают до устранения дефекта, не допуская уменьшения размера а (рис. 5.31) до значения менее 66,0 мм. При невозможности устранения дефекта патрубок бракуют. Патрубок соединительный впускных коллекторов в сборе КАМАЗ (рис. 5.31) Трубу водяную правую и левую бракуют при наличии обломов или трещин. Коробление поверхности прилегания к головкам цилиндров устанавливают на поверочной плите с помощью щупа. Допуск неплоскостности поверхностей 0,15 мм. При большем значении поверхности обрабатывают до устранения дефекта, не допуская уменьшения размера а (рис. 5.32) до значения менее 47 мм. При невозможности устранения дефекта трубу бракуют, как и при кавитационных разрушениях водоотводящих поясков, если размеры b и с менее 3,5 мм. Труба водяная КАМАЗ (рис. 5.32) Патрубок водяной коробки бракуют при наличии обломов, трещин, а также раковин на внутренней поверхности и разрушении кромок патрубка, затрагивающих более половины толщины стенки. Коробление поверхности прилегания патрубка к водяной коробке устанавливают на поверочной плите с помощью щупа. Допуск неплоскостности поверхности 0,15 мм. При большем значении поверхность обрабатывают до устранения дефекта, не допуская уменьшения толщины прилива до размера менее 28,5 мм. При невозможности устранения дефекта патрубок бракуют.
Коробку водяную бракуют при наличии обломов и трещин. Коробление привалочной плоскости устанавливают на поверочной плите с помощью щупа. Допуск неплоскостности поверхности 0,1 мм. При большем значении привалочную плоскость обрабатывают до устранения дефекта, не допуская уменьшения её толщины до размера менее 6 мм. При невозможности устранения дефекта коробку бракуют.
Трубы перепускные (подводящую и соединительную) бракуют при наличии раковин на внутренней поверхности глубиной более 1,0 мм и кавитационных разрушениях: наружных посадочных поверхностей при разрушениях глубиной 0,1 мм на расстоянии 5 мм друг от друга; концевых поясков при разрушениях на длине 10 мм в двух местах по окружности. Далее предварительная сборка двигателя КАМАЗ.
(PDF) Обнаружение неисправностей в двигателе путем объединения информации от мультивибрационных датчиков
Согласно таблице 6, когда используется модель SVDD
с одним датчиком, трудно принять решение, поскольку
существует сходство принадлежности между нормальные
и незначительные состояния, а уровень точности классификации составляет
приблизительно 72%. Однако точность классификации
составляет более 91% при объединении теории доказательств
SVDD и D-S.Эти результаты показывают
, что существует неопределенность и меньшее доверие, когда
использует информацию только из одного источника для обнаружения неисправностей. Однако мы можем воспользоваться преимуществами дополнительной и избыточной информации при использовании нескольких источников
, что повысит надежность диагностики и точность
.
Уровень точности классификации составляет 81% с использованием комбинации SVM и теории доказательств D-S, что на
выше, чем у метода, использующего один источник, но на
ниже, чем у предлагаемого метода.Однако время обнаружения
для комбинированного SVM и D-S свидетельствует о том, что
ory больше, чем время, необходимое для предлагаемого метода
, из-за большого объема вычислений в
SVM. Статистические данные по 90 тестовым образцам показали, что предложенный метод
лучше, чем
BPNN и FCM по точности классификации и времени обнаружения.
Заключение
Для обнаружения неисправностей двигателя был представлен метод, сочетающий SVDD и теорию свидетельств D-S,
, в котором информация от трех датчиков вибрации
может быть объединена.
Этот метод использует преимущества избыточности и
дополнительной информации в каждом датчике и решает
проблему неопределенности и низкой достоверности, которая присутствует в
при использовании информации с одного датчика. Экспериментальные результаты
показывают, что предложенный метод
имеет более высокую степень точности классификации и быстрее
, чем некоторые методы, включая комбинацию SVM
и теории доказательств D-S, BPNN и FCM.
Заявление о конфликте интересов
Автор (ы) заявили об отсутствии потенциальных конфликтов интересов с
в отношении исследования, авторства и / или публикации этой статьи
.
Финансирование
Автор (ы) раскрыл получение следующей финансовой поддержки
за исследование, авторство и / или публикацию этой статьи
: Эта работа была поддержана Национальным естественным научным фондом
Китай (нет.60674111) и Фонд естественных наук Тяньцзинь
в рамках гранта 15JCTPJC64200.
Эта поддержка признательна.
Ссылки
1. Qin Y, Mao Y и Tang B. Составляющая вибрационного сигнала
разделение путем итеративного использования поиска по базису и его применения
для обнаружения механических неисправностей. J Sound Vib
2013; 332: 5217–5235.
2. Шарма А., Сугумаран В. и Бабу Девасенапати С.
Обнаружение пропусков зажигания в двигателе IC с использованием сигнала вибрации
и алгоритмов дерева решений.Измерение 2014 г .; 50:
370–380.
3. Чамай М., О С-Д и Ким И-Дж. Разработка диагностической системы
с использованием анализа LPC / cepstrum в вибрации машины
. J Mech Sci Tech 2013; 27 (9):
2629–2636.
4. Ван X, Лю Ц., Би Ф. и др. Диагностика неисправностей дизельного двигателя
на основе адаптивных вейвлет-пакетов и фрактальной размерности EEMD-
. Сигнал системы мех. Pr 2013; 41:
581–597.
5. Li Z, Yan X, Wang X и др.Обнаружение трещин зубчатых колес в
сложной коробке передач ветряных турбин с использованием контролируемого
ограниченного компонентного анализа сигналов вибрации, поступающих с многоканальных датчиков. J Sound Vib 2016;
371: 406–433.
6. Сафизаде М.С. и Латифи С.К. Использование данных нескольких датчиков
fusion для диагностики дефектов вибрации подшипников качения
с помощью акселерометра и датчика веса. Сообщите Fusion
2014; 18: 1–8.
7.Ли Зи, Ян Х, Го Зи и др. Новый интеллектуальный метод слияния
многомерных датчиков и его применение
для диагностики неисправностей трибосистем судовых дизельных двигателей.
Tribol Lett 2012; 47: 1–15.
8. Цао В., Донг Г., Чен В. и др. Мультисенсорная информация
Интеграциядля онлайн-мониторинга состояния износа двигателей
sel. Tribol Int 2015; 82: 68–77.
9. Цзян З, Фэн Х, Фэн Х и др. Изучение алгоритма
на базе СВДД для диагностики неисправностей механического оборудования системы
.Физические процедуры 2012; 33: 1068–1073.
10. Чжан И, Лю X-D, Xie F-D и др. Классификатор неисправностей
вращающихся механизмов на основе описания данных взвешенного опорного вектора
. Expert Syst Appl 2009; 36:
7928–7932.
11. Zhang XL, Chen W., Wang BJ, et al. Интеллектуальная диагностика неисправностей
вращающегося оборудования с использованием опорного вектора
машина с алгоритмом муравьиных колоний для синхронного выбора параметров и оптимизации параметров.Нейрокомпьютер-
2015 г .; 167: 260–279.
12. Дуан Л., Се М., Бай Т. и др. Новый метод описания опорных векторных данных
для диагностики неисправностей оборудования с несбалансированными наборами данных
. Expert Syst Appl 2016; 64:
239–246.
13. Yin G, Zhang Y-T, Li Z-N, et al. Онлайн-диагностика неисправностей
Метод, основанный на описании дополнительных векторных данных поддержки
и экстремальной обучающей машине с выходной структурой приращения
.Нейрокомпьютинг 2014; 128: 224–231.
14. Хуэй К.Х., Лим М.Х., Леонг М.С. и др. Dempster – Shafer
теория доказательств для диагностики неисправностей нескольких подшипников. Eng
Appl Artif Intell 2017; 57: 160–170.
15. Моосавиан А., Хазаи М., Наджафи Г. и др. Распознавание неисправностей свечи зажигания
на основе комбинации датчиков и классификатора
с использованием теории свидетельств Демпстера – Шафера.
Appl Acoust 2015; 93: 120–129.
16. Басир О. и Юань X.Диагностика неисправностей двигателя на основе объединения данных нескольких датчиков
с использованием теории свидетельств Демпстера – Шафера
. Сообщите Fusion 2007; 8: 379–386.
8 International Journal of Distributed Sensor Networks
Приложение для раннего обнаружения неисправностей коленчатого вала и поршня двигателя внутреннего сгорания
1. Введение
Мониторинг рабочих условий двигателя внутреннего сгорания является важной темой, особенно при разработке нового двигателя и проведении испытаний на повышение производительности с прототипом.Есть много движущихся частей с высокой скоростью и ускорениями, а пределы подшипников и соединений должны выдерживать силы инерции и сгорания. Всегда есть необходимость максимизировать производительность двигателей, и конструкторы используют ограничения компонентов. Следовательно, многие компоненты находятся на пределе перегрева, а многие подшипники и соединения используются на пределе своей несущей способности. Системы охлаждения и смазки также используются на пределе своих возможностей, передавая тепловую энергию и обеспечивая необходимое давление масла.
Прототипы, созданные для испытаний при разработке двигателей, имеют множество датчиков температуры, давления и расхода, размещенных в критических местах для контроля характеристик и эксплуатационных ограничений компонентов. Многие измерения деформации и ускорения также выполняются во время испытаний на долговечность и вибрацию, чтобы проверить, соответствует ли конструкция ограничениям. Ускорение и акустическая эмиссия, измеренные во время испытаний на долговечность, также используются для понимания повреждений и / или износа компонентов. Этот подход является темой мониторинга состояния конструкций (SHM), и он широко используется из-за простоты применения и преимуществ раннего обнаружения повреждений для понимания основных причин и механизма повреждения.
SHM — это мультидисциплинарный подход, использующий методы, представленные в структурной динамике, неразрушающей оценке, обработке сигналов, теории обнаружения, машинном обучении, вероятности и статистике, а также курсах по сенсорным сетям [1]. Его применение является обычным для высокопроизводительных механических систем, таких как аэрокосмическая промышленность, где для достижения целей необходимо применять легкие и устойчивые к повреждениям конструкции. Также важно применять его к долгосрочным конструкциям с высокими инвестициями, таким как мосты, морские нефтяные платформы, здания и системы выработки электроэнергии, чтобы иметь возможность предотвращать катастрофические отказы путем раннего обнаружения отказов или повреждений.
В литературе было проведено много исследований по обнаружению неисправностей для двигателей внутреннего сгорания. Киммих и Изерманн [2] представили исследование по обнаружению неисправностей на основе модели для впрыска, внутреннего сгорания и трансмиссии дизельных двигателей. Они заявили, что большинство доступных бортовых систем диагностики в основном основаны на простом контроле пороговых значений или проверке достоверности измеренных сигналов, а также на методах, основанных на сигналах, таких как частотный анализ сигнала частоты вращения двигателя.Этот подход не подходит для сложных систем машин, таких как двигатели внутреннего сгорания. Чтобы улучшить мифологию обнаружения неисправностей, они предложили метод обнаружения неисправностей на основе моделей, при котором аналитическая информация о процессе в форме математических моделей процесса используется для оценки информации различных датчиков. Это позволяет получить более конкретную информацию о характеристиках неисправности. Kimmich et al. [3] далее разработали свой подход к обнаружению неисправностей на основе модов для системы впуска, системы впрыска с системой сгорания и системы выпуска.Они использовали полуфизические модели, идентификацию с помощью локальных линейных нейронных сетей, модели сигналов и фильтры, чтобы оценить разницу между нормальным и неисправным состояниями работы. Они проверили, что их подход успешен в режиме реального времени на испытательных стендах. Клевер и Изерманн [4] разработали метод обнаружения неисправностей в многопараметрических системах с использованием такого входного возбуждения и его применение к системе всасываемого воздуха современного дизельного двигателя с общей топливной магистралью. Они успешно применяются для дифференциации неисправностей датчика воздушных масс от других неисправностей технологического процесса.
Khelil et al. [5] предложили методологию с использованием нейронной сети для мониторинга работоспособности двигателя и диагностики неисправностей. Шаг обучения нейронной сети улучшается за счет выбора ее входных данных с использованием корреляционного исследования и эвристической информации. Они подтвердили свою модель на реальных данных, соответствующих реальным ошибочным ситуациям. Они успешно разработали этапы генерации остаточных и пороговых значений и показали, что их результаты демонстрируют хороший компромисс между чувствительностью к сбоям и устойчивостью к ложным срабатываниям.
Oskoueian и Nuawi [6] предложили метод обнаружения износа блока двигателя с помощью тензометрических измерений и его обработки с применением методов статистического анализа. Они проанализировали эксцесс сигнала деформации для разных частотных диапазонов отдельно.
Jena и Panigrahi [7] представили подход к обнаружению дефектов поршневых отверстий мотоциклов на основе анализа сигнатур шума двигателя. Они разработали надежный алгоритм фильтрации и систему принятия решений на основе статистического обучения с использованием шумовой сигнатуры двигателя исправных и неисправных транспортных средств.Они обнаружили, что спектр СПМ акустического сигнала не указывает точно на наличие дефекта. Показано, что непрерывное вейвлет-преобразование с использованием биортогонального вейвлета работает удовлетворительно, но не оправдывает ожиданий, для выявления дефекта отверстия поршня в двухколесных транспортных средствах. Было обнаружено, что комплексный вейвлет Морле является наиболее подходящим вейвлетом для характеристики всплеска акустического сигнала из-за дефекта отверстия поршня и связанных с ним частот. Пачки акустического сигнала из-за таких дефектов несут частотные составляющие примерно от 100 до 300 Гц.Механизмы статистического обучения, такие как искусственная нейронная сеть и машина опорных векторов, предназначены для классификации дефектов. Показано, что нейронная сеть с прямой связью и обратным распространением способна классифицировать исправные и неисправные транспортные средства со средним показателем успеха 99,98% и 98,11% соответственно.
Wu et al. [8] представили метод обработки сигналов для нормализации и разделения источников нелинейных сигналов акустической эмиссии многоцилиндрового дизельного двигателя для приложений мониторинга состояния и обнаружения неисправностей.Они показали, что алгоритм разделения источников может отделить помехи сигнала соседних цилиндров от контролируемого цилиндра, если известны постоянная затухания волны и задержка времени прихода на пути распространения. В них использовались четыре датчика акустической эмиссии резонансного типа, установленные на головке блока цилиндров. Они предварительно усиливаются перед записью системой сбора данных с частотой дискретизации 1 МГц. Они обнаружили, что их подход особенно полезен при применении техники для мониторинга состояния малогабаритных дизельных двигателей, где сильные помехи сигнала от соседних цилиндров.
Chen et al. [9] разработали диагностическую систему для обнаружения отказов поршня в двигателях внутреннего сгорания. Они использовали искусственные нейронные сети, обучая сеть с помощью большого количества данных в различных условиях двигателя (различные условия скорости / нагрузки в нормальных условиях и с разными местоположениями / уровнями неисправностей). Они предложили трехступенчатые сетевые системы для выявления неисправностей поршней, локализации неисправностей и серьезности неисправностей. Многослойные сети персептронов использовались на стадии обнаружения и стадии серьезности / прогноза.Вероятностная нейронная сеть использовалась для определения цилиндра, в котором произошла ошибка. Они подтвердили свой подход реальными испытаниями.
Dayong et al. [10] выполнили исследование для извлечения компонентов неисправности из аномальных акустических сигналов и автоматической диагностики неисправности дизельного двигателя. Они предложили новый метод с наложением дислокаций для улучшения техники случайного декремента и поиска метода начальной точки для выделения компонента разлома из аномальных акустических сигналов. Они обнаружили, что их подход лучше, чем традиционный метод анализа сигналов о вибрации и акустическом сигнале.
Флетт и Боун [11] разработали систему обнаружения и диагностики неисправностей для обнаружения неисправностей деформированной пружины клапана и аномального зазора клапана с помощью сигнала акселерометра. Среди различных реализованных методов классификации наилучшую общую производительность показал метод Наив-Байеса с самой низкой точностью обнаружения 99,95%.
Moosavian et al. [12] предложили метод определения неисправности задира поршня путем измерения ускорения. Они проанализировали сигнал вибрации во временной области, частотной области и частотно-временной области.Они использовали непрерывное вейвлет-преобразование для получения частотно-временных представлений. Они показали, что задиры поршня возбуждают полосу частот 2,4–4,7 кГц, в которой больше влияет частота 3,7 кГц. Из сигналов вибрации двигателя было извлечено семь различных характеристик, относящихся к полосе частот 2,4–4,7 кГц. Результаты показали, что максимальное, среднее значение, среднеквадратичное значение, асимметрия, эксцесс и импульсный коэффициент вибрации двигателя, относящиеся к найденному диапазону частот, значительно увеличились из-за неисправности задира поршня.Полученные результаты показали, что предложенный метод выявил дефект задира поршня и обнаружил вибрационные характеристики этого дефекта в виде полосы частот.
Целью исследования является представление неисправностей подшипников и поршней, возникающих в двигателе внутреннего сгорания, путем обработки сигнала ускорения. Для этого был оборудован двигатель внутреннего сгорания, который прошел испытания в контролируемых условиях. Затем сигнал ускорения обрабатывался во временной и частотной областях.Осмотр неисправных деталей показал, что сигнал вибрации можно успешно использовать для обнаружения неисправностей подшипников и поршней в двигателе внутреннего сгорания.
2. Обнаружение неисправностей
Чтобы проверить эффективность измерения ускорения от блока цилиндров и головки блока цилиндров для раннего обнаружения неисправности подшипников, дизель I4 был оснащен 3 акселерометрами. Для записи и обработки сигнала использовалась система сбора данных (Reilhofer Delta Analyzer v2) (рис.1). Расположение датчиков показано на рис. 2.
Рис. 1. Схема тестовой установки
Рис. 2. Акселерометры на блоке двигателя
а)
б)
в)
Отказ подшипников коленчатого вала и поршня может вызвать серьезные повреждения двигателя. Типичные причины выхода из строя гидродинамического подшипника шейки коленчатого вала:
• проблема с подачей давления масла,
• проблема качества масла,
• перегрев масла,
• высокие силы инерции и сгорания,
• инородные частицы.
Двигатели внутреннего сгорания имеют датчики температуры и давления для контроля надлежащего функционирования системы смазки. Однако эти датчики обычно размещаются далеко от коленчатого вала и поршня, и локальный отказ одного из подшипников не может быть обнаружен сразу. Поверхности подшипников могут повредиться до того, как будет обнаружено изменение температуры. Поврежденный подшипник может не работать должным образом, если он слегка поврежден, даже если условия, вызвавшие его выход из строя, больше не существуют.
Чтобы вызвать повреждение подшипника, был применен следующий сценарий испытаний. Во-первых, были проведены измерения ускорения, чтобы определить пределы нормальной работы. Затем количество масла уменьшилось на треть, чтобы не было достаточного давления масла на гидродинамические подшипники и произошел контакт металла с металлом. Кривые частоты вращения, крутящего момента, температуры масла и давления масла показаны на рис. 3. Температура масла повышается с 800 ° C до 1550 ° C примерно за 300 секунд.
Фиг.3. Параметры работы двигателя во временной области
Рис. 4. Нормальное рабочее ускорение (зеленый) и неправильное рабочее ускорение (красный) в частотной области
Когда сигнал ускорения был обработан для получения изменения амплитуды вибрации в зависимости от порядка работы двигателя, как это видно на рис. 4, наблюдается существенное изменение между нормальными условиями (зеленые кривые) и неисправным состоянием (красное состояние) для вибрации. амплитуда в районе 20-го и 700-го двигателей заказов.Это изменение амплитуды ускорения на высокой частоте является признаком контакта металла с металлом в подшипниках и / или стенках поршня и цилиндра.
Базовая концепция — Penn State
TY — JOUR
T1 — Обнаружение и локализация неисправностей в авиационных газотурбинных двигателях. Часть 1
T2 — Базовая концепция
AU — Gupta, S.
AU — Ray, A.
AU — Sarkar, S.
AU — Yasar, M.
N1 — Авторские права: Авторские права 2008 Elsevier B.В., Все права защищены.
PY — 2008
Y1 — 2008
N2 — Мониторинг деградации имеет первостепенное значение для безопасности и надежности эксплуатации воздушного судна, а также для своевременного обслуживания его критических компонентов. В этом документе, состоящем из двух частей, формулируется и подтверждается новая методология мониторинга деградации авиационных газотурбинных двигателей с упором на обнаружение и локализацию возникающих неисправностей. В сложной системе с несколькими взаимосвязанными компонентами (например,авиационный двигатель), устранение неисправностей становится важной задачей из-за возможных взаимодействий ввода-вывода и обратной связи между отдельными компонентами. В этой статье, которая является первой из двух частей, представлены основные концепции обнаружения и изоляции неисправностей (FDI) в сложных динамических системах. Алгоритмы FDI сформулированы в настройке символической динамической фильтрации (SDF), о которой недавно сообщалось в литературе. Основная концепция SDF построена на принципах символической динамики, статистического распознавания образов и теории информации.Помимо резких крупных сбоев, алгоритмы на основе SDF способны обнаруживать медленно развивающиеся аномалии (т. Е. Отклонения от номинального поведения) на основе анализа данных временных рядов критических переменных процесса различных компонентов двигателя. Вторая часть, являющаяся сопроводительным документом, проверяет концепцию, изложенную в первой части, на испытательном стенде типовой модели двухконтурного турбовентиляторного авиационного двигателя для обнаружения и локализации зарождающихся неисправностей.
AB — Мониторинг деградации имеет первостепенное значение для безопасности и надежности эксплуатации воздушного судна, а также для своевременного обслуживания его критических компонентов.В этом документе, состоящем из двух частей, формулируется и подтверждается новая методология мониторинга деградации авиационных газотурбинных двигателей с упором на обнаружение и локализацию возникающих неисправностей. В сложной системе с несколькими взаимосвязанными компонентами (например, авиационным двигателем) изоляция неисправностей становится важной задачей из-за возможных взаимодействий ввода-вывода и обратной связи между отдельными компонентами. В этой статье, которая является первой из двух частей, представлены основные концепции обнаружения и изоляции неисправностей (FDI) в сложных динамических системах.Алгоритмы FDI сформулированы в настройке символической динамической фильтрации (SDF), о которой недавно сообщалось в литературе. Основная концепция SDF построена на принципах символической динамики, статистического распознавания образов и теории информации. Помимо резких крупных сбоев, алгоритмы на основе SDF способны обнаруживать медленно развивающиеся аномалии (т. Е. Отклонения от номинального поведения) на основе анализа данных временных рядов критических переменных процесса различных компонентов двигателя.Вторая часть, являющаяся сопроводительным документом, проверяет концепцию, изложенную в первой части, на испытательном стенде типовой модели двухконтурного турбовентиляторного авиационного двигателя для обнаружения и локализации зарождающихся неисправностей.
UR — http://www.scopus.com/inward/record.url?scp=45749141186&partnerID=8YFLogxK
UR — http://www.scopus.com/inward/citedby.url?scp=45749141186&partnerID=8YFLog
U2 — 10.1243 / 09544100JAERO311
DO — 10.1243 / 09544100JAERO311
M3 — Артикул
AN — SCOPUS: 45749141186
VL — 222
SP — 307
JE — 307 изSP — 307 Инженеры-механики, часть G: Journal of Aerospace Engineering
JF — Proceedings of the Institution of Engineering Engineers, Part G: Journal of Aerospace Engineering
SN — 0954-4100
IS — 3
ER —
AI Visual Inspection Для обнаружения дефектов на производстве
«Почему я должен заботиться о новой крутой технологии, пока она не решит какие-либо мои проблемы?» — именно такой разговор я имел с руководителем завода по очистке воды за чашкой теплого кофе.
То, что начиналось как пустая болтовня, в конечном итоге превратилось в проницательную и содержательную дискуссию о технологиях искусственного интеллекта для обнаружения дефектов и контроля качества. Этот разговор существенно изменил мое видение и подход.
Цель этой статьи — описать, как реализовать визуальный осмотр на основе искусственного интеллекта для обнаружения дефектов. Дело не в крутизне искусственного интеллекта — нет, дело в практических решениях конкретных проблем.
Изображение предоставлено
Концепция визуального осмотра с использованием искусственного интеллектаИскусственный интеллект в производстве — модный термин.Когда доходит до описания решений для обнаружения дефектов на основе ИИ, часто речь идет о какой-то технологии визуального контроля, основанной на глубоком обучении и компьютерном зрении.
Что такое глубокое обучение при визуальном осмотре?
Глубокое обучение — это аспект технологии машинного обучения, основанный на искусственных нейронных сетях. Принцип работы технологии глубокого обучения — научить машины учиться на собственном примере. Предоставляя нейронную сеть с помеченными примерами конкретных типов данных, можно выделить общие закономерности между этими примерами, а затем преобразовать их в математическое уравнение.Это помогает классифицировать будущую информацию.
Благодаря технологии визуального контроля интеграция алгоритмов глубокого обучения позволяет различать части, аномалии и символы, которые имитируют визуальный осмотр человека при работе компьютеризированной системы.
Итак, что именно это означает? Приведем пример.
Если вам нужно было создать программное обеспечение для визуального контроля для автомобилестроения, вам следует разработать алгоритм, основанный на глубоком обучении, и обучить его примерам дефектов, которые оно должно обнаружить.При наличии достаточного количества данных нейронная сеть в конечном итоге обнаружит дефекты без каких-либо дополнительных инструкций.
Системы визуального контроля, основанные на глубоком обучении, хороши для обнаружения сложных по своей природе дефектов. Они не только устраняют сложные поверхности и косметические недостатки, но также обобщают и концептуализируют поверхности деталей.
Как интегрировать систему визуального контроля AI
1. Постановка проблемы
Разработка визуального контроля часто начинается с бизнес-анализа и технического анализа.Цель здесь — определить, какие дефекты должна обнаруживать система.
Другие важные вопросы, которые следует задать:
- Что такое среда системы визуального контроля?
- Следует ли проводить проверку в реальном времени или отложить?
- Насколько тщательно система визуального контроля должна обнаруживать дефекты и должна ли она различать их по типу?
- Существует ли какое-либо существующее программное обеспечение, которое интегрирует функцию визуального контроля, или оно требует разработки с нуля?
- Как система должна уведомлять пользователей об обнаруженных дефектах?
- Должна ли система визуального контроля регистрировать статистику обнаружения дефектов?
- И ключевой вопрос: Существуют ли данные для разработки модели глубокого обучения, включая изображения «хороших» и «плохих» продуктов и различных типов дефектов?
Инженеры по обработке и анализу данных выбирают оптимальное техническое решение и последовательность действий на основе полученных ответов.
2. Сбор и подготовка данных
Инженеры по обработке и анализу данных должны собрать и подготовить данные, необходимые для обучения будущей модели, до начала разработки модели глубокого обучения. Для производственных процессов важно внедрить аналитику данных Интернета вещей. Когда мы говорим о моделях визуального контроля, данные часто представляют собой видеозаписи, где изображения, обработанные с помощью модели визуального контроля, включают видеокадры. Существует несколько вариантов сбора данных, но наиболее распространенными являются:
- Создание существующей видеозаписи, предоставленной клиентом
- Создание видеозаписей с открытым исходным кодом, применимых для определенных целей
- Сбор данных с нуля в соответствии с требованиями модели глубокого обучения
Самыми важными параметрами здесь являются качество видеозаписи.Более качественные данные приведут к более точным результатам.
После сбора данных мы готовим их к моделированию, очищаем, проверяем на наличие аномалий и обеспечиваем актуальность.
3. Разработка модели глубокого обучения
Выбор подхода к разработке модели глубокого обучения зависит от сложности задачи, необходимого времени выполнения и бюджетных ограничений. Есть несколько подходов:
3.1 Использование службы разработки моделей глубокого обучения (например, Google Cloud ML Engine, Amazon ML и т. Д.)
Такой подход имеет смысл, когда требования к функциям обнаружения дефектов соответствуют шаблонам, предоставляемым данной службой. Эти услуги могут сэкономить время и бюджет, поскольку нет необходимости разрабатывать модели с нуля. Вам просто нужно загрузить данные и настроить параметры модели в соответствии с соответствующими задачами.
В чем подвох? Эти типы моделей не подлежат настройке. Возможности моделей ограничены опциями, предоставляемыми данной услугой.
3.2 Использование предварительно обученных моделей
Предварительно обученная модель — это уже созданная модель глубокого обучения, которая выполняет задачи, аналогичные той, которую мы хотим выполнить. Нам не нужно строить модель с нуля, поскольку она использует обученную модель, основанную на наших данных.
Предварительно обученная модель может не на 100% соответствовать всем нашим задачам, но она обеспечивает значительную экономию времени и средств. Использование моделей, предварительно обученных на больших наборах данных, позволяет нам настраивать эти решения в соответствии с нашей проблемой.
3.3 Разработка модели глубокого обучения с нуля
Этот метод идеален для сложных и безопасных систем визуального контроля. Подход может потребовать много времени и усилий, но результат того стоит.
При разработке пользовательских моделей визуального контроля специалисты по данным используют один или несколько алгоритмов компьютерного зрения. К ним относятся классификация изображений, обнаружение объектов и сегментация экземпляров.
Многие факторы влияют на выбор алгоритма (ов) глубокого обучения.К ним относятся:
- Бизнес-цели
- Размер объектов / дефектов
- Условия освещения
- Количество продуктов для проверки
- Виды дефектов
- Разрешение изображений
Пример категорий дефекта:
источник: NECAM
Допустим, мы разрабатываем модель визуального осмотра для оценки качества зданий. Основное внимание уделяется обнаружению дефектов на стенах.Для получения точных результатов визуального осмотра необходим обширный набор данных, поскольку категории дефектов могут быть невероятно разнообразными, от отслаивающейся краски и плесени до трещин в стенах. Оптимальным подходом здесь будет разработка модели на основе сегментации экземпляров с нуля. В некоторых случаях также возможен подход с предварительно обученной моделью.
Другой пример — визуальный осмотр фармацевтического производства, при котором вы хотите отличить пузырьки воздуха от частиц в таких продуктах, как высоковязкие исходные растворы.Наличие пузырьков — единственная категория дефектов, поэтому требуемый набор данных не будет таким обширным, как в приведенном выше примере. Оптимальный подход к разработке модели глубокого обучения может заключаться в использовании службы разработки модели вместо разработки ее с нуля.
4. Обучение и оценка
Следующим шагом после разработки модели визуального контроля является ее обучение. На этом этапе специалисты по обработке данных проверяют и оценивают производительность и точность результатов модели. Здесь пригодится тестовый набор данных.Для системы визуального контроля это может быть набор видеозаписей, которые либо устарели, либо похожи на те, которые мы хотим обработать после развертывания.
5. Развертывание и улучшение
При развертывании модели визуального контроля важно учитывать, насколько архитектура программного и аппаратного обеспечения системы соответствует мощности модели.
Программное обеспечение
Структура программного обеспечения, основанного на визуальном контроле, основана на сочетании веб-решений для передачи данных и инфраструктуры Python для обработки нейронных сетей.
Ключевым параметром здесь является хранение данных. Существует три распространенных способа хранения данных: на локальном сервере, в облачной потоковой службе или в бессерверной архитектуре.
Система визуального контроля предполагает хранение видеозаписей. Выбор решения для хранения данных часто зависит от функциональности модели глубокого обучения. Например, если система визуального контроля использует большой набор данных, оптимальным выбором может быть облачная потоковая служба.
Аппаратные средства
В зависимости от отрасли и процессов автоматизации, устройства, необходимые для интеграции системы визуального контроля, могут включать:
- Камера. Основная опция камеры — потоковое видео в реальном времени. Некоторые примеры включают IP и CCTV.
- Шлюз. Как специализированное оборудование, так и программное обеспечение хорошо подходят для системы визуального контроля.
- ЦП / графический процессор . Если необходимы результаты в реальном времени, графический процессор будет лучшим выбором, чем центральный процессор, поскольку первый может похвастаться более высокой скоростью обработки, когда речь идет о моделях глубокого обучения на основе изображений. Можно оптимизировать ЦП для работы с моделью визуального контроля, но не для обучения.Примером оптимального графического процессора может быть Jetson Nano.
- Фотометр (дополнительно). В зависимости от условий освещения среды системы визуального контроля могут потребоваться фотометры.
- Колориметр (дополнительно). При обнаружении цвета и яркости в источниках света колориметры визуализации имеют неизменно высокое пространственное разрешение, что позволяет проводить подробный визуальный контроль.
- Термографическая камера (опция). В случае автоматизированного обследования пароводяных трубопроводов и объектов рекомендуется иметь данные термографической камеры.Данные термографической камеры предоставляют ценную информацию для обнаружения утечки тепла / пара / воды. Данные тепловизионной камеры также полезны для проверки теплоизоляции.
- Дроны (опционально). В настоящее время сложно представить автоматизированное обследование труднодоступных мест без дронов: внутренних устройств зданий, газопроводов, визуального осмотра танкеров, осмотра ракет / шаттлов. Дроны могут быть оснащены камерами высокого разрешения, которые могут обнаруживать дефекты в реальном времени.
Модели глубокого обучения открыты для улучшения после развертывания.Подход глубокого обучения может повысить точность нейронной сети за счет итеративного сбора новых данных и повторного обучения модели. В результате получается «более умная» модель визуального контроля, которая обучается за счет увеличения объема данных во время работы.
Примеры использования визуального осмотра
Здравоохранение
В рамках борьбы с COVID-19 большинство аэропортов и пограничных переходов теперь могут проверять пассажиров на наличие признаков заболевания.
Baidu, крупная китайская технологическая компания, разработала крупномасштабную систему визуального контроля, основанную на искусственном интеллекте.Система состоит из камер компьютерного зрения и инфракрасных датчиков, которые прогнозируют температуру пассажиров. Теперь технология, работающая на железнодорожном вокзале Цинхэ в Пекине, может проверять до 200 человек в минуту. Алгоритм AI обнаруживает любого, у кого температура выше 37,3 градуса.
Другой пример из реальной жизни — система на основе глубокого обучения, разработанная компанией Alibaba. Система может обнаружить коронавирус на компьютерной томографии грудной клетки с точностью 96%. Имея доступ к данным о 5000 случаях COVID-19, система выполняет тест за 20 секунд.Более того, он может отличить обычную вирусную пневмонию от коронавируса.
Авиакомпания
По данным Boeing, 70% рынка аэрокосмических услуг стоимостью 2,6 триллиона долларов в настоящее время посвящено качеству и техническому обслуживанию. В 2018 году Airbus представила новую автоматизированную систему проверки самолетов на базе дронов, которая ускоряет и упрощает визуальные проверки. Эта разработка сокращает время простоя самолетов, одновременно повышая качество отчетов об инспекциях.
Автомобильная промышленность
Toyota недавно согласилась на 1 доллар.Расчет в размере 3 миллиардов долларов из-за неисправности, которая приводила к ускорению автомобилей, даже когда водители пытались замедлить скорость, что привело к 6 смертельным случаям в США. Используя когнитивные возможности систем визуального контроля, таких как Cognex ViDi, производители автомобилей могут анализировать и выявлять проблемы с качеством намного точнее и разрешите их до того, как они возникнут.
Производство компьютерного оборудования
Растет спрос на печатные платы меньшего размера. Fujitsu Laboratories возглавляет разработку систем распознавания на базе искусственного интеллекта для электронной промышленности.Они сообщают о значительном прогрессе в области качества, стоимости и доставки.
Текстиль
Реализация автоматизированного визуального контроля, наряду с подходом глубокого обучения, теперь может обнаруживать проблемы с текстурой, плетением, вышивкой и соответствием цветов.
Например, система искусственного интеллекта Datacolor может учитывать исторические данные прошлых визуальных проверок для создания настраиваемых допусков, которые более точно соответствуют образцам.
В заключение мы приведем цитату генерального менеджера, о которой мы упоминали ранее: «Для меня не имеет значения, является ли предлагаемая технология лучшей, но меня действительно волнует, насколько хорошо она решит мои проблемы.”
Панели солнечных батарей
Солнечные панели, как известно, страдают от пыли и микротрещин. Автоматическая проверка солнечных панелей во время производства, а также до и после установки — хорошая идея для предотвращения отправки неисправных солнечных панелей и быстрого обнаружения поврежденных панелей на вашей солнечной ферме. Например, DJI Enterprise использует дроны для проверки солнечных батарей.
Инспекция трубопроводов
Известно, что газо- и нефтепроводы имеют огромную протяженность. Последние данные за 2014 год дают в общей сложности чуть меньше 2 175 000 миль (3 500 000 км) трубопроводов в 120 странах мира.Утечки газа и нефти могут нанести огромный вред природе в результате химического загрязнения, взрывов и пожаров.
Обследование спутников и дронов с помощью техники компьютерного зрения — хороший инструмент для раннего обнаружения и локализации утечки газа / нефти. Недавно DroneDeploy сообщил, что они нанесли на карту около 180 миль трубопроводов.
AI Визуальный осмотр: основные выводы
- Concept
Визуальный осмотр Al основан на традиционных методах компьютерного зрения
и человеческом зрении. - Выбор
Подход к разработке модели глубокого обучения зависит от задачи, времени выполнения и ограничений бюджета. - Алгоритм
Алгоритмы глубокого обучения обнаруживают дефекты путем имитации человеческого анализа при работе компьютеризированной системы. - Архитектура
Программное обеспечение и оборудование должны соответствовать возможностям модели глубокого обучения. - Главный вопрос
При запуске визуального осмотра главный вопрос: «Какие дефекты должна обнаруживать система?» - Улучшения
После развертывания модель глубокого обучения становится «умнее» за счет накопления данных.
Визуальный осмотр на базе искусственного интеллекта для обнаружения дефектов
Скачать PDFОтправляя свой адрес электронной почты, вы соглашаетесь с нашей Политикой конфиденциальности и соглашаетесь получать информацию о наших новостях и деловых предложениях. Вы можете в любой момент отозвать свое согласие, отправив запрос на [email protected].
Спасибо!
URL для загрузки файла PDF был отправлен на вашу электронную почту
OkПодключенная диагностика Телематика и диагностика неисправностей
Connected Solutions Вход для клиентов
Линия жизни для вашего двигателя
С помощью телематики подключите свой двигатель к Cummins по беспроводной сети для непрерывного мониторинга и диагностики предупреждений о сбоях в системе как на дорогах, так и вне дорог на широком спектре оборудования, используя удобное мобильное приложение, электронную почту или веб-портал.
Щелкните, чтобы просмотреть брошюру
Устранение пробелов в анализе производительности
Принимайте лучшие решения о том, когда остановиться, идентифицируя и ранжируя коды ошибок в порядке серьезности и сообщая предполагаемую основную причину сбоев системы на уровне компонентов.
Избегайте прогрессирующего повреждения двигателя
Будьте в курсе с помощью практических сведений о таймерах критических двигателей в течение нескольких секунд после срабатывания при возникновении неисправности, что поможет вам предотвратить ненужные расходы на ремонт и свести к минимуму незапланированные простои.
Быстрее возвращайтесь на водительское сиденье
С помощью Cummins Care ™ представитель сможет предоставить вам информацию о неисправностях и определить ближайшее сертифицированное место ремонта с опытными техническими специалистами, которые будут использовать оригинальные запчасти Cummins для обслуживания вашего оборудования.
Оставайтесь на связи с полем из любого места с нашим передовым мобильным приложением
Проверка состояния оборудования парка
Просматривайте свой автопарк с помощью интеллектуальной приборной панели для определения оборудования высокого риска
Интеллектуальное исследование силовых агрегатов
Анализ критических и серьезных неисправностей со снижением производительности в реальном времени
Помощь при диагностике в реальном времени
Найдите местных поставщиков услуг Cummins, которые помогут вам быстро решить проблемы с обслуживанием
Участвующие поставщики телематических услуг
В целом это был отличный опыт.«
«Профилактическое обслуживание очень важно для нас, — говорит Натан Саммер, супервайзер гаража Юго-Восточного школьного округа Гамильтона. «Для наших 300 автобусов у нас есть только два запасных транзитных автобуса и четыре обычных запасных. Поэтому очень важно избегать любой возможности простоев или сбоев на маршруте. Мы особенно должны защищать детей; мы не можем позволить им ждать сторона дороги, особенно в холодную погоду.
Connected Diagnostics и Connected Advisor помогли нашим автобусам не сбиться с пути.Мы нашли продукты Cummins Smart Connected Products очень полезными. Было приятно, что диагностический отчет о работоспособности настроен и доставлен нам автоматически. Это также очень помогает, когда мы планируем техническое обслуживание с нашим специалистом по обслуживанию на месте, зная, что требует немедленных действий, а что нет ».
Мы уважаем вашу конфиденциальность. Прочтите нашу политику.
Оценка гибридного состояния для обнаружения аномалий авиационных двигателей и устранения неисправностей
[1] Volponi A.J., «Управление состоянием газотурбинных двигателей: прошлые, настоящие и будущие тенденции», журнал , посвященный двигателям для газовых турбин и энергетическим транзакциям ASME , Vol. 136, № 5, май 2014 г., документ 051201 https://doi.org/10.1115/1.4026126
[2] Чен М., Ху LQ и Тан Х.Л., «Подход к выбору оптимальных измерений на газотурбинном двигателе. Диагностика неисправностей », Журнал двигателей для газовых турбин и силовых операций стандарта ASME , Vol. 137, № 7, июль 2015 г., Документ 071203.https://doi.org/10.1115/1.4029171
[3] Донг Г. К. и Чжу З. Х., «Автономный роботизированный захват не взаимодействующей цели с помощью адаптивного расширенного фильтра Калмана на основе визуального сервопривода», Acta Astronautica , Vol. 122, май – июнь 2016 г., стр. 209–218. https://doi.org/10.1016/j.actaastro.2016.02.003
[4] Чжун С.С., Луо Х. и Лин Л., «Улучшенный подход к обнаружению аномалий на основе корреляции для данных мониторинга состояния промышленных предприятий. Оборудование », Международная конференция IEEE по прогнозированию и управлению здоровьем, , IEEE Publ., Пискатауэй, Нью-Джерси, июнь 2016 г., статья 7542850.
[5] Ли Ю. Г., «Оценка летных характеристик газовой турбины с использованием измерений газового пути двигателя», Journal of Propulsion and Power , Vol. 31 № 3, 2015, с. 851–860. https://doi.org/10.2514/1.B35381
[6] Леонард О., Боргет С. и Деваллеф П., «Алгоритм адаптивной оценки для мониторинга характеристик авиационных двигателей», Journal of Propulsion and Power , Vol. 24, No. 4, 2008, стр.763–769. https://doi.org/10.2514/1.34320
[7] Видерхольд О., Кинг Р., Ноак Б.Р., Нойхаус Л., Нейз В., Энгардт Л. и Свобода М., «Адаптивное управление в Осевой турбовентилятор: реализация без модели с коротким временем отклика », AIAA Journal , Vol. 2011. 49, № 7. С. 1429–1436. https://doi.org/10.2514/1.J050702
[8] Тахан М., Цоутсанис Э., Мухаммад М. и Карим ЗАА, «Мониторинг, диагностика и прогнозирование состояния здоровья на основе результатов газовых турбин: обзор », Applied Energy , Vol.198, июль 2017 г., стр. 122–144. https://doi.org/10.1016/j.apenergy.2017.04.048
[9] Саймон Д., «Сравнение подходов к фильтрации для оценки состояния авиационных двигателей», Aerospace Science and Technology , Vol. 12, № 4, 2008, с. 276–284. https://doi.org/10.1016/j.ast.2007.06.002
[10] Сан С.Л., Лин Х.Л., Ма Дж. и Ли XY, «Распределенная оценка объединения нескольких датчиков с приложениями в сетевых системах: Обзорная статья », Information Fusion , Vol.38, ноябрь 2017 г., стр. 122–134. https://doi.org/10.1016/j.inffus.2017.03.006
[11] Ян К., Конг ХХ и Ван Х., «Диагностика неисправностей на основе модели для снижения производительности газового тракта турбовентиляторного двигателя с помощью оптимального Устойчивые остатки », ASME Turbo Expo: Техническая конференция и выставка турбин , июнь 2016 г., статья GT2016-56300.
[12] Карлсон Н. А., «Объединенный фильтр для отказоустойчивых интегрированных навигационных систем», IEEE PLANS »Отчет о симпозиуме 88 по определению местоположения и навигации -« Навигация в 21 век », IEEE Publ., Пискатауэй, штат Нью-Джерси, ноябрь 1988 г., стр. 110–119. https://doi.org/10.1109/PLANS.1988.195473
[13] Поурбабаи Б., Мескин Н. и Хорасани К., «Обнаружение, изоляция и идентификация неисправностей датчика с использованием гибридного фильтра Калмана на основе нескольких моделей. для газотурбинных двигателей », IEEE Transactions on Control Systems Technology , Vol. 24, № 4, 2016, с. 1184–1200. https://doi.org/10.1109/TCST.2015.2480003
[14] Сюн З., Чен Дж. Х., Ван Р. и Лю Дж.Ю., «Новый алгоритм обмена информацией с динамическим вектором в федеративном фильтре», Aerospace Science and Technology , Vol. 29, № 1, 2013, с. 37–46. https://doi.org/10.1016/j.ast.2013.01.006
[15] Тиан Т., Сан С.Л. и Лин Х.Л., «Распределенный комбинированный фильтр для многосенсорных систем с коррелированными шумами с конечным шагом. ” Информация Fusion , Vol. 46, март 2019 г., стр. 128–140. https://doi.org/10.1016/j.inffus.2018.05.002
[16] Ван С.К., Рен В. и Чен Дж., «Полностью распределенная оценка динамического состояния с неопределенными моделями процессов», IEEE Transactions по управлению сетевыми системами , Vol. 5, № 4, 2018, с. 1841–1851. https://doi.org/10.1109/TCNS.6509490
[17] Ван Г.К., Ли Н. и Чжан Ю.Г., «Диффузионный нелинейный фильтр Калмана с периодическими наблюдениями», Труды Института инженеров-механиков, часть G —Журнал аэрокосмической техники , Vol. 232, No. 15, 2017, с.2775–2783. https://doi.org/10.1177/0954410017716192
[18] Нетто М. и Мили Л., «Надежный управляемый данными фильтр Купмана-Калмана для оценки динамического состояния энергосистем», IEEE Transactions on Power Systems , Vol. 33, № 6, 2018, с. 7228–7237. https://doi.org/10.1109/TPWRS.2018.2846744
[19] Кабальеро-Агила Р., Эрмосо-Карасо А. и Линарес-Перес Дж., «Сетевое распределенное объединение оценок при неопределенных выходах со случайными задержками передачи. , Потери пакетов и многопакетная обработка », Signal Processing , Vol.156, март 2019 г., стр. 71–83. https://doi.org/10.1016/j.sigpro.2018.10.012
[20] Ван З.Г., Чен Д.Й. и Ду Дж.Х., «Распределенная робастная фильтрация с ограничениями по дисперсии со случайно возникающими нелинейностями и отсутствующими измерениями по сенсорным сетям. , ” Neurocomputing , Vol. 329, февраль 2019 г., стр. 397–406. https://doi.org/10.1016/j.neucom.2018.10.025
[21] Чен Б., Чжан В.А. и Ю Л., «Распределенная фильтрация Калмана слияния на конечном горизонте и ограничении полосы пропускания для беспроводного датчика с ограничением энергии. Сети », IEEE Transactions on Signal Processing , Vol.62, № 4, 2014, с. 797–812. https://doi.org/10.1109/TSP.2013.2294603
[22] Динг Дж., Сан С.Л., Ма Дж. и Ли Н., «Оценка слияния для многосенсорных сетевых систем с компенсацией потерь пакетов», Информация Fusion , Vol. 45, январь 2019 г., стр. 138–149. https://doi.org/10.1016/j.inffus.2018.01.008
[23] Баттилотти С., Какаче Ф., д’Анджело М. и Джермани А., «Распределенная фильтрация Калмана по сенсорным сетям с Неизвестные случайные отказы каналов связи », Письма по системам управления IEEE , Vol.2, № 4, 2018, с. 587–592. https://doi.org/10.1109/LCSYS.2018.2845304
[24] Лин К., Чжэн Р.Х., Ян Г.Ф. и Лу Си, «Анализ сходимости распределенной фильтрации Калмана для сетей относительного зондирования», Frontiers of Information Технология и электроника , Vol. 19, № 9, 2018, с. 1063–1075. https://doi.org/10.1631/FITEE.1700066
[25] Гэн Х., Ван З. Д. и Ченг Й., «Распределенное объединение объединенных фильтров Тобита Калмана в сети с задержкой пакетов: вероятностная перспектива», IEEE Transactions по обработке сигналов , Vol.66, № 17, 2018, с. 4477–4489. https://doi.org/10.1109/TSP.2018.2853098
[26] Кабальеро-Агила Р., Эрмосо-Карасо А., Линарес-Перес Дж. и Ван З. «Новый подход к распределенной фильтрации слияния для сетевых систем со случайными матрицами параметров и коррелированными шумами », Information Fusion , Vol. 45, январь 2019 г., стр. 324–332. https://doi.org/10.1016/j.inffus.2018.02.006
[27] Рашеди М., Лю Дж. и Хуанг Б., «Задержки связи и потери данных в распределенных адаптивных EKF с высоким коэффициентом усиления, AIChE Journal , Vol.62, № 12, 2016, с. 4321–4333. https://doi.org/10.1002/aic.15351
[28] Лу Ф., Чжэн У.Х., Хуанг Дж.К. и Фэн М., «Оценка характеристик жизненного цикла и мониторинг работоспособности газотурбинного двигателя в полете», Журнал измерения и управления динамическими системами , Vol. 138, № 9, сентябрь 2016 г., документ 091009. https://doi.org/10.1115/1.4033556
[29] Джонатан А., Джонатан С. и Дин К., «Модульная авиационная силовая установка. Моделирование двигателя большого коммерческого самолета », AIAA Paper 2008-4579, 2008.
[30] Синополи Б., Шенато Л., Франческетти М., Пула К., Джордан М. И. и Састри С. С., «Фильтрация Калмана с периодическими наблюдениями», IEEE Transactions on Automatic Control , Vol. 49, № 9, 2004, с. 1453–1464. https://doi.org/10.1109/TAC.2004.834121
[31] Лу Ф., Гао TYY, Хуан Дж. К. и Цю XJ, «Новый распределенный расширенный фильтр Калмана для оценки состояния газового тракта авиационного двигателя с помощью датчика. Неопределенность термоядерного синтеза », Aerospace Science and Technology , Vol.84, январь 2019 г., стр. 90–106. https://doi.org/10.1016/j.ast.2018.10.019
[32] Meijer GCM, Wang GJ и Fruett F., «Датчики температуры и источники опорного напряжения, реализованные в технологии CMOS», Sensor Journal , Vol. 1, № 3, 2001, с. 225–234. https://doi.org/10.1109/JSEN.2001.954835
[33] Ли Дж., Фан Д., Цзи ЦД и Бу ЗП, «Метод улучшения возможностей динамического отклика для датчика температуры авиационного двигателя», журнал Journal авиакосмической энергетики , Vol.27, № 3, 2012, с. 707–714 (на китайском языке). https://doi.org/10.13224/j.cnki.jasp.2012.03.030
[34] Xiao WD, Wu JK и Xie LH, «Адаптивное планирование сенсоров для отслеживания целей в беспроводной сенсорной сети», Proceedings SPIE — Международного общества оптической инженерии , Vol. 5910, SPIE Publ., Беллингем, Вашингтон, 2005 г., документ 59100B. https://doi.org/10.1117/12.618124
Диагностика неисправностей и экспериментальный анализ 4-тактного 4-цилиндрового бензинового двигателя с использованием FaultTree Analysis
Диагностика неисправностей и экспериментальный анализ 4-тактный 4-цилиндровый бензиновый двигатель с неисправностью Анализ дерева
Международный журнал инженерных тенденций и технологий (IJETT) | | |
© 2017, журнал IJETT | ||
Том-46 Номер-8 | ||
Год издания: 2017 | ||
Авторы: Махадев Найк, Прабодхан Кадам, Свапнил Кадам, Дхирадж Кадам, Дигвиджай Кулкарни | ||
10.14445/22315381 / IJETT-V46P278 |
Махадев Найк, Прабодхан Кадам, Свапнил Кадам, Дхирадж Кадам, Дигвиджай Кулкарни «Диагностика неисправностей и экспериментальный анализ 4-тактный 4-цилиндровый бензиновый двигатель с неисправностью Анализ дерева «, Международный журнал инженерных тенденций и технологий (IJETT), V46 (8), 445-453 апрель 2017 г. ISSN: 2231-5381. Www.ijettjournal.org. Опубликовано исследовательской группой седьмого чувства
Abstract
Двигатель внутреннего сгорания играет жизненно важную роль
роль в любом автомобильном и механическом
системы.Эти двигатели используются во всем мире как устройства
преобразование одной формы энергии в другую форму
и стоимость их так высока; поддержание таких
двигатели это существенная вещь. В этом проекте основное внимание
занимается обнаружением неисправностей и экспериментальным анализом
двигатель. Доступная литература была тщательно изучена.
рассмотрены и многие методы обнаружения неисправностей
были изучены. Завершение обзора исследования.
тот анализ дерева отказов, который использует логические элементы и
Булева алгебра.Это техника графического дизайна
которые обеспечивают блок-схему надежности и дерево
разработано выявит первопричины. Используя
этот метод — простой способ выявить неисправные части
системы. После выявления неисправных частей
двигатель эти детали будут либо отремонтированы, либо заменены
и проводились различные экспериментальные испытания, такие как нагрузка,
Скорость и тест Морзе на двигателе. Сравнивать
выполнение тестовой установки с деревом отказов и без него
используются подходы к анализу.Полученные результаты
Использование анализа дерева отказов является эффективным способом. В
производительность двигателя увеличивается после
метод технического обслуживания и анализа дерева отказов
способствует успешной оптимизации обслуживания
усилие.
Список литературы
[1] DobrivojeCatic (2013), «Анализ дерева отказов солнечной
Концентраторы »Международный журнал исследований качества, т.
7, выпуск 4, стр 595–604.
[2] Рафал Ласковски (2015), «Анализ дерева отказов как инструмент для
моделирование структуры надежности главного судового двигателя »
Научные журналы Морского университета Щецина, т.
41, выпуск 113, стр 71-77.
[3] Х. Э. Ламберт (2003), «Использование анализа дерева отказов для
Анализ надежности и безопасности автомобилей »SAE Society of
Всемирный конгресс автомобильных инженеров, UCRL-JC-154905.
[4] Глисович Ясна (2014), «Анализ дерева отказов гидроусилителя.
система »Int. J. Дизайн транспортных средств, том 64, № 1, стр. 26-
45
[5] Ахмед Али Байг (2013 г.), «Анализ надежности с использованием дерева отказов.
Анализ: обзор »International Journal of Chemical
Техника и приложения, Vol.4, No. 3, pp 169-173.
[6] М. Р. Парате и С. Н. Дандаре (2012), «Идентификация неисправностей в ИС.
Движок с использованием DSP и ИНС »Международный журнал
Компьютерные приложения, стр 59-63.
[7] Naresh Kr. Рагхуванши (2012), «Анализ отказов
Клапаны двигателя внутреннего сгорания: обзор »International
Журнал инновационных исследований в области науки, техники и
TechnologyVol.