Почему ржавеют оцинкованные и алюминиевые машины
Часто сталкиваюсь с заблуждением касательно оцинкованных машин. Люди считают, что, если машина оцинкованная, она не будет гнить и ржаветь. Но, к сожалению, это не всегда так.
Такая разная оцинковка
Для начала надо понимать, что оцинковка оцинковке рознь. Можно оцинковать кузов слоем в 2 мкм, а можно слоем в 20 мкм — это первое. Второе — методов оцинковки куча. Бюджетные машины обычно оцинковывают самым бюджетным способом. Как правило, это холодная оцинковка. Цинкование происходит путём окраски кузова анафорезными грунтами с высоким содержанием высокодисперсного цинкового порошка (содержание цинка в готовом покрытии 89−93%). Такая оцинковка, конечно, лучше, чем ничего, но по факту при повреждении ЛКП от коррозии она защищает слабо.
Производители часто используют такой вид оцинковки, потому она не так сильно сказывается на цене автомобиля (в бюджетном сегменте борются за каждую копейку). К тому же это даёт право говорить, что кузов оцинкован — это выгодно из маркетинговых соображений.
Ещё один бюджетный способ оцинковки — цинкрометалл. Если простыми словами, то это обычная сталь, покрытая специальным цинкосодержащим грунтом на стадии проката. Цинкрометалл хорош в регионах, где нет высокой влажности, но в российских условиях, особенно если ЛКП повреждено, металл все равно начинает ржаветь. Пусть не так быстро, как голая сталь. Так что уповать на спасительную оцинковку в данном случае также не стоит. Нужно быстро подкрашивать сколы и царапины.
Читайте также
«Из-за коронавируса мы по уши в дерьме»Вторая зимняя волна пандемии будет намного страшнее первой
Довольно хороший способ оцинковки — гальванический. Это когда кузов купают в ванне с цинкосодержащим электролитом. Под действием электрического тока цинк осаждается на металле равномерным слоем. Обычно этот слой составляет 5−20 мкм. При таком способе оцинковки производители, как правило, дают гарантию от сквозной коррозии кузова не менее 10 лет.
Гальваническую оцинковку редко применяют на бюджетных машинах, потому что это довольно дорого, а вот на машинах С-класса и выше она встречается часто.
А лучший способ оцинковки — горячее цинкование. Сухой заранее подготовленный кузов автомобиля опускают в ванну с горячим цинком. Температура расплава обычно от 500 до 4000 °C. Такой термический способ обработки кузова не только самый лучший, но и самый дорогой. Применяют его далеко не все производители даже премиум-класса.
Цинковое покрытие в данном случае получается самым толстым и прочным. При незначительных повреждениях ЛКП место скола или царапины могут даже затянуться отложениями цинка — этот процесс называется самовосстановлением. В этом случае даже поврежденный кузов может не ржаветь 5−8 лет. Как правило, на машины, оцинкованные горячим способом, автопроизводители дают гарантию от сквозной гарантии 15 лет и больше.
Однако надо понимать, что даже самое лучшее цинкование не может защитить кузов от коррозии навечно. Если ЛКП целое, то всё хорошо, но если появился скол, царапина или другие последствия ДТП, то цинковое покрытие будет защищать металл от коррозии лишь до поры до времени.
Куда уходит цинк?
Скорость коррозии цинкового покрытия в условиях атмосферы составляет около 3 мкм в год. В сельской местности — там, где на дорогах нет агрессивной химии, соли и реагентов, — цинковый слой держится дольше, и разрушается примерно со скоростью 1−2 мкм в год. В больших городах и агрессивных средах, напротив, скорость коррозии выше — от 3 до 7 мкм в год.
Многие думают, что цинк не ржавеет, но это не так: коррозия съедает цинковое покрытие. Прелесть цинкового покрытия в том, что пока есть хоть немного цинка, металл ржаветь не будет. Говоря простым языком, цинк просто даёт вам время на подкраску и ремонт. Если у вас отслоилась краска, появился скол или царапина, она может не ржаветь несколько месяцев или даже лет. Но потом обязательно зацветет, так что с покраской всё-таки лучше не тянуть, потому что редко можно знать наверняка, как именно оцинкован кузов.
Доказать или опровергнуть наличие оцинковки можно только экспериментальным путем или с помощью дорогостоящих лабораторных исследований. Производители очень редко открывают эту информацию. Как правило, они ограничиваются общими фразами о том, что кузов оцинкован. А, как оцинкован, не говорят.
Читайте также
Путин дал команду «Суперджету»: На взлетЗа полет на самолете, вызывающем у многих пассажиров страх, будет приплачивать государство
А ведь бывает односторонняя или двухсторонняя оцинковка. Иногда цинкуют только некоторые внешние панели кузова, а внутри цинка нет. Часто у бюджетников цинкуются только самые уязвимые места. Нередко при общей оцинковке крыша остается не оцинкованной.
Порой машины слишком активно шлифуют на производстве и цинковый слой стирается. Иногда цинка нет на сварных швах. Нюансов очень много. Производитель всегда пытается сэкономить, чтобы конечная цена на автомобиль была максимально привлекательной — это надо понимать.
Если речь идет о покупке подержанной машины, то уповать на оцинковку не стоит тем более. Если машина была в авариях, то часто сами же владельцы экономят и покупают дешевые запчасти из дешевого металла без всякой оцинковки.
Проблемный алюминий
Что касается алюминиевых машин, с ними всё ещё сложнее. Они не ржавеют привычным рыжим цветом. Они подвержены электрохимической коррозии. Она возникает в местах контакта разных металлов. Например, алюминия и стали.
Полностью алюминиевые автомобили — всё ещё редкость. Часто используются алюминиевые панели, а каркас стальной. Или алюминиевые только капот, крылья, крыша и так далее. Вот в этих местах кузов будет разрушаться и сыпаться в первую очередь. Без рыжего цвета — ведь коррозия алюминия похожа на металлическую перхоть.
На колесах: Как жилось дальнобойщикам в СССР
Обзор рынка: 5 дорогих опций, за которые точно не стоит переплачивать
Кузов на Рено Логан оцинкованный или нет?
Разнообразный и суровый климат в России ставит перед автопроизводителями серьёзные требования по антикоррозийной обработке своих автомобилей. Резкие перепады температуры, высокая влажность воздуха, соль, противогололёдные реагенты способны за несколько лет съесть кузов автомобиля. По этой причине, чтобы занять прочное место на российском рынке, конструкторам автомобиля Рено Логан пришлось основательно поломать голову. Но обо всём по порядку.
Содержание
- 1 Рено Логан I поколение
- 1.1 Проблемные места
- 1.1.1 Днище автомобиля
- 1.2 Решение о полной оцинковке кузова
- 1.3 7 слоёв оцинковки
- 1.1 Проблемные места
- 2 Рено Логан II поколение
- 3 Только цифры!
- 4 Подводим итог
Рено Логан I поколение
Автомобиль Рено Логан начал свое путешествие по российским дорогам с 2005 года, тогда еще совсем новая модель неуверенно занимала автомобильный рынок, завоёвывая доверие у потенциальных покупателей. В первый год серийного выпуска автомобилей на некотором проценте машин появились проблемные зоны в виде пятен и следов коррозии на различных частях кузова.
Проблемные места
Ржавчина на петле багажника первое поколение
Рядом с петлёй вблизи
Под другим углом
Тоже самое
Таковыми оказались: арки колёс, проем багажника, рамка лобового стекла и части крыши под уплотнителями дверей. И помимо всего прочего были обнаружены трещины на лакокрасочном покрытии в районе стыков задних стоек и крыши автомобиля. Как говорится, первый блин получился комом. Однако благодаря тому, что выпуск новой модели был широко анонсирован СМИ, и вызвал большой ажиотаж, подобные проблемы в Рено Логан обросли не только множеством мифов и слухов, но иногда и вовсе были преувеличены.
Одно из самых проблемных мест старого Логана — это двери
Очаги коррозии проявлялись на автомобилях, выпущенных преимущественно в период с 2005 по 2006 год. Если говорить формально, то подобные нарушения в ЛКП (лакокрасочном покрытии), не требовали никакого гарантийного обслуживания, т.к они проявлялись уже после её окончания.
Нередко начинает ржаветь проём двери
Однако факт остаётся фактом, и реальная проблема была выявлена. Тогда концерн Рено предпринял беспрецедентные меры по расширению гарантии на ЛКП, и чтобы не потерять доверие покупателей признал все факты появления коррозии гарантийным случаем.
Днище автомобиля
Днище автомобиля практически не страдает от ржавчины за счёт высокого клиренса Логана. Клиренс позволяет меньше цеплять неровности дороги и царапать днище от ухабов.
Решение о полной оцинковке кузова
Концерн утверждает, что кузов Рено Логан при производстве подвергается оцинковке, но многие владельцы Рено Логан не доверяют этой информации
Чтобы в дальнейшем не испытывать проблем с выпускаемыми автомобилями, было принято решение об оцинковке практически всех наружных деталей.
Кроме того, с целью дополнительной защиты кузова была применена технология «жертвенных анодов», которые устанавливались преимущественно в петлях дверей в виде вставок и коррозировали вместо железа. Гарантия на антикоррозийную защищённость автомобиля составляет в пределах 15 лет, что является достаточным сроком даже для автомобилей более дорогого ценового сегмента.
Отлетел кусок краски с крыла, виден оцинкованный кузов, но ржавчина все-таки стала появляться
Результат от проделанной работы концерна Рено, не заставил себя долго ждать. Слухи о новом бюджетном и недорогом автомобиле, с оцинкованным кузовом, достаточно быстро разошлись в народе и по праву лишились претензий по качеству покрытия на «Логанах». Немногие современные автопроизводители могут похвастать таким результатом в сфере обслуживания и понимания в проблемах своих клиентов.
7 слоёв оцинковки
Модели I поколения и рестайлинга при производстве, обрабатывались 7 слоями защитного антикоррозийного покрытия и состояли из:
- Оцинковка деталей кузова снаружи
- Катафорезный слой грунта
- Герметизирующая и противокоррозионная мастика
- Второй слой грунтовки
- Слои автомобильной краски
- Слои автомобильного лака
- Антикоррозийные мастики
Такого слоёного пирога вполне достаточно, для использования автомобиля I поколения в условиях российских дорог. Абсолютное большинство «Логановодов» сходятся в одном, что дополнительная антикоррозийная обработка на технически целый кузов не требуется, мало того – это пустая трата денег.
Рено Логан II поколение
Большинство владельцев сходится во мнении о том, что кузов Рено Логан неплохо оцинкован и практически не подвержен корроззии
При конструировании кардинально изменившегося внешнего вида, автомобиля Рено Логан 2 поколения, конструкторы взглянули по-другому и на антикоррозийную обработку кузова.
Начиная с 2013 и по настоящее время на конвейерах Рено, модели Логан подвержены полной обработке кузова, включая скрытые полости путём двусторонней гальванической оцинковки (отлично сочетается с краской и грунтом) по методу погружения в цинковый электролит под воздействием тока.
Ржавчина на Логане которому меньше года (под передней правой дверью — под накладкой)
При такой обработке слой цинка составляет порядка 9-15 мкм. Тем самым при обычных условиях эксплуатации, первые следы коррозии могут проявиться не ранее, чем через 10 лет использования автомобиля.
Только цифры!
- 5-15 мкм (микрометров) – идеальная толщина цинкового покрытия для защиты от возникновения коррозии на автомобиле.
- От 1 до 6 мкм – такова скорость разрушения цинкового слоя в год, при повреждении лакокрасочного покрытия. Разрушение происходит активнее при положительных температурах.
Подводим итог
Подводя итог всему вышесказанному, можно быть уверенным, что большинство автомобилей Рено Логан на наших дорогах имеют оцинкованный кузов с высокой степенью защиты от коррозии. Имея такой автомобиль можно быть готовым ко всем неприятностям российского климата и условий эксплуатации.
История стали: повышение безопасности автомобилей
Трудно представить себе время, когда автомобили не делались почти полностью из металла. Однако до 20 века первые производители автомобилей основывали свои конструкции на деревянной лошади и повозке.
Все изменилось после 1900 года с появлением новой технологии, которая позволила производить металлические листы, которым можно было придать любую желаемую форму, а в 1916 году в США был произведен первый в мире автомобиль со стальным кузовом. Новые способы ковки более прочного и безопасного металла продолжали появляться быстрыми темпами — настолько быстро, что к концу XIX в.Цельностальные кузова автомобилей 30-х годов стали отраслевым стандартом.
Конечно, сталь, используемая в то время, сильно отличается от стали, используемой в современных моделях. За десятилетия ученые и производители открыли, как изменить микроструктуру стали, чтобы сделать ее прочнее, а транспортные средства — еще безопаснее. Действительно, несмотря на огромные успехи в области электронных средств помощи водителю, которых добилась автомобильная промышленность, одним из самых больших улучшений в области безопасности стало использование стали.
Этот веб-сайт использует Vimeo в качестве внешнего видеоплеера. Чтобы посмотреть это видео, Vimeo необходимо установить файл cookie. Пожалуйста, измените настройки файлов cookie здесь.
Современная высокопрочная сталь
С началом нового тысячелетия она стала еще прочнее. В начале 2000-х предел прочности стали, используемой в производстве автомобилей, составлял около 500 мегапаскалей.
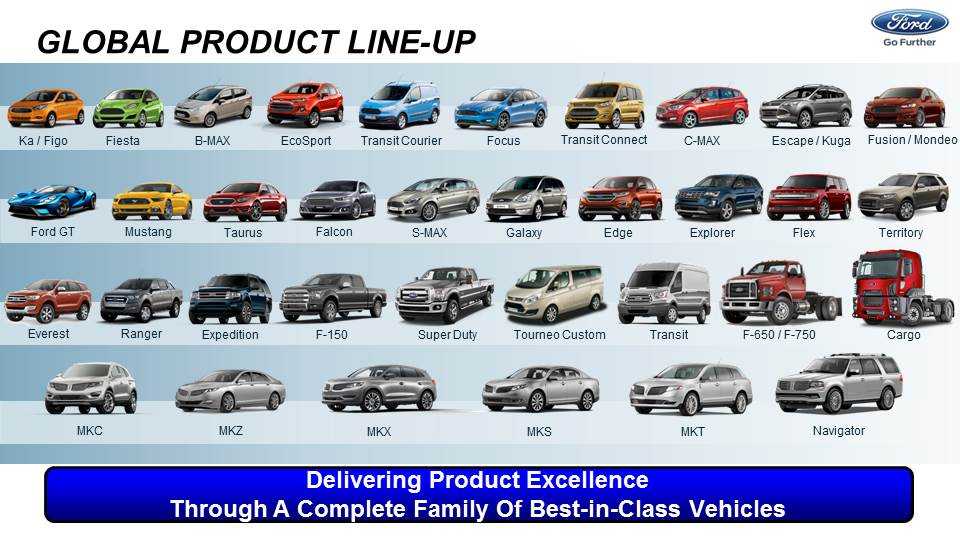
Эта новая высокопрочная сталь делает автомобили легче, повышает эффективность и позволяет лучше контролировать передачу энергии в случае столкновения. Благодаря достижениям в производстве стали, он может рассеивать и перенаправлять силу удара более эффективно, чем когда-либо.
В передней и задней части автомобиля, которые имеют больший объем для поглощения энергии столкновения до того, как она достигнет водителя и пассажиров, производители обычно используют стали, которые легче деформируются и становятся прочнее. При столкновении они сминаются до тех пор, пока ударная волна не достигает брандмауэра из высокопрочной стали, который предотвращает дальнейшее разрушение и сохраняет неповрежденной центральную структуру вокруг всех, кто находится внутри.
Hyundai Motor: единственный производитель автомобилей с собственным сталелитейным заводом
Hyundai Motor, единственный производитель с собственным сталелитейным заводом, вложила значительные средства, чтобы сделать его одним из самых передовых предприятий по производству стали в мире.
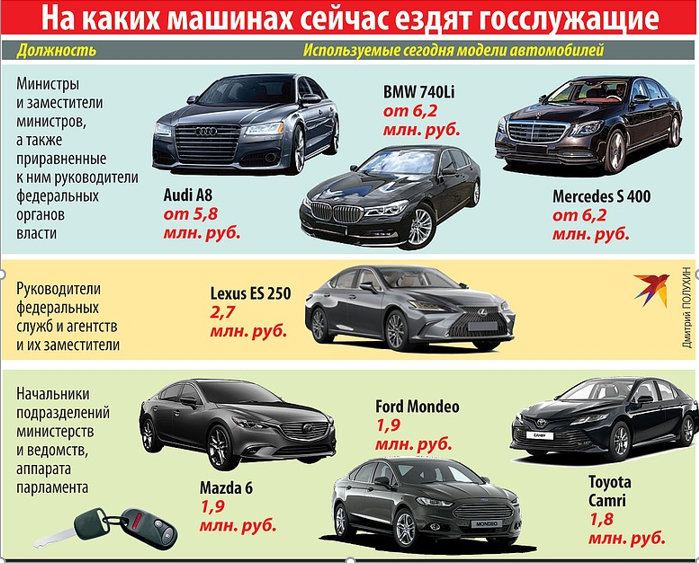
Чтобы гарантировать качество, в стандарте нет различий. Hyundai использует лучшую сталь, независимо от того, на каком рынке продается автомобиль. Чтобы доказать это, Hyundai взяла две Sonata, одну произведенную в Корее, а другую в США, и разбила их лоб в лоб на специально построенной площадке, и ни одна из них не был более скомпрометирован с точки зрения базовой структуры безопасности.
Этот веб-сайт использует Vimeo в качестве внешнего видеоплеера. Чтобы посмотреть это видео, Vimeo необходимо установить файл cookie. Пожалуйста, измените настройки файлов cookie здесь.
Реальное применение сверхвысокопрочной стали Hyundai буквально спасло жизни. Возьмем, к примеру, случай, произошедший в корейском городе Пусан еще в апреле 2012 года. При переходе моста бортовой грузовик с четырехтонным транспортным контейнером опрокинулся набок и упал на Hyundai Accent, стоявший на соседней полосе. к этому.
К счастью для всех участников, Accent выдержал вес и остался полностью неповрежденным благодаря сверхвысокопрочной стали, которую Hyundai создала для использования в центральной стойке. Стальная стойка была тщательно разработана, чтобы выдерживать нагрузки, в пять раз превышающие вес автомобиля, и при этом она на 5,5 кг легче, чем стойка предыдущей модели, для повышения топливной экономичности.
Этот веб-сайт использует Vimeo в качестве внешнего видеоплеера. Чтобы посмотреть это видео, Vimeo необходимо установить файл cookie. Пожалуйста, измените настройки файлов cookie здесь.
Hyundai использует высокопрочную сталь в своих европейских автомобилях
На европейском рынке более прочный каркас кузова, созданный, например, для Hyundai i10, использует высокопрочную сталь и включает кольцевые усиливающие петли внутри B и C-стойки, а также поперек его днища и крыши, с дополнительными распорками спереди между капотом и стойками подвески для повышения жесткости и безопасности.
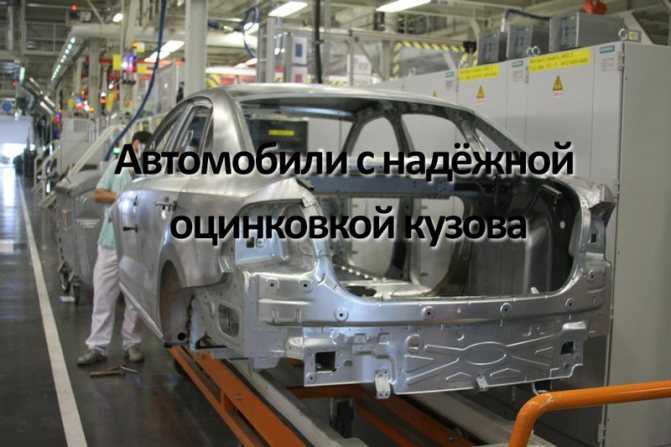
Каркас кузова i10 также стал более жестким благодаря использованию высокопрочной стали, специальных заготовок, усиливающих петель и дополнительных распорок, при этом жесткость на кручение увеличилась на 27 процентов по сравнению с его предшественником. Формы из высокопрочной стали свыше 29процента его структуры кузова — огромное увеличение по сравнению с девятью процентами, найденными в оригинальном i10. Эти основы не только улучшают ударопрочность автомобиля, но также значительно улучшают шум, вибрацию и жесткость.
Широкое использование сверхвысокопрочной стали Hyundai также улучшило управляемость и производительность i20. Это повысило его жесткость, благодаря чему колеса i20 плотно прилегают к дороге, а шасси и кузов работают в полной гармонии.
Усовершенствованная высокопрочная сталь нового поколения i30 на 10 % легче обычной низкоуглеродистой стали и в два раза жестче. Количество, используемое в каждом автомобиле, почти удвоилось до 53 процентов, одновременно снизив вес кузова i30 на 28 кг и увеличив его жесткость на 22 процента по сравнению с его предшественником. Усовершенствованная высокопрочная сталь
, высокопрочный специальный стальной сплав, также используется в ключевых областях корпуса i40, придавая ему дополнительную прочность. Излишне говорить, что эта инновация Hyundai обеспечивает еще большую защиту водителя и пассажиров в случае столкновения.
Новый каркас кузова Hyundai Tucson обладает лучшей в своем классе конструкционной жесткостью благодаря разумному использованию усовершенствованной высокопрочной стали — на 30 % больше, чем у его предшественника, — которая также обеспечивает комплексное снижение дорожного шума, обеспечивая тишину и тишину в салоне. С точки зрения безопасности водителя и разработки все более совершенных продуктов инвестиции Hyundai в сталь продолжают приносить дивиденды по всему модельному ряду.
Данные о потреблении*
i10
Бензиновые двигатели
1,0 MPI (66 л.с.): Расход топлива смешанный: 5,8–4,0 л/100 км; город: 7,3 – 4,9 л/100 км;
загородный: 4,8 – 3,5 л/100 км; CO 2 выбросы в смешанном цикле: 134–93 г/км
1,25 MPI (87 л.
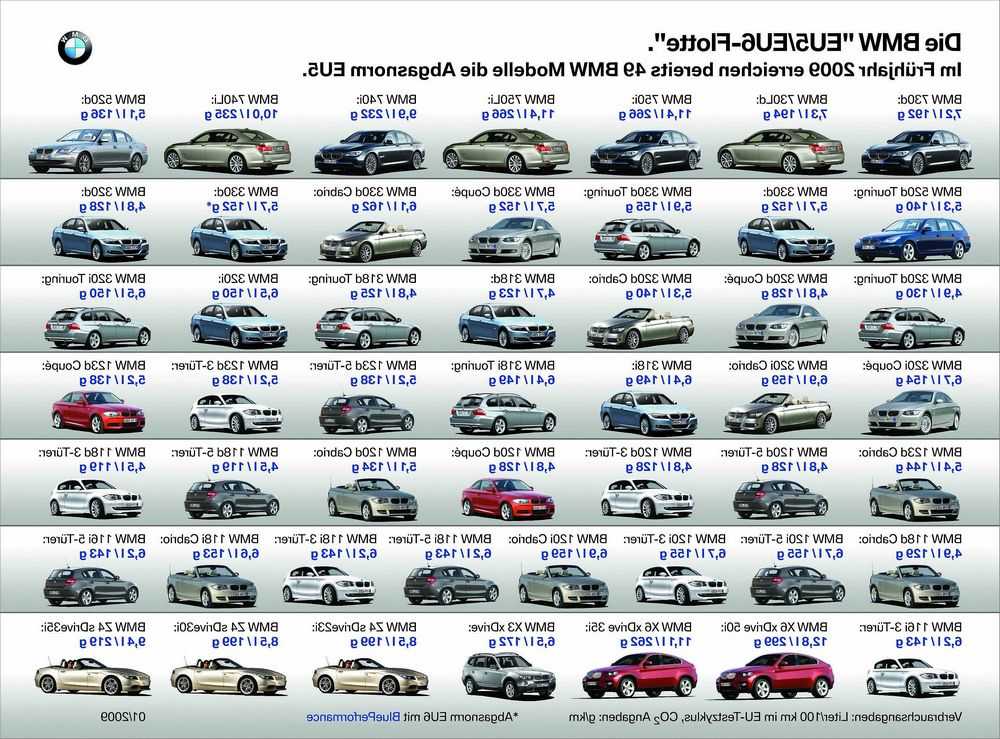
1.0 LPG (67 л.с.): Расход топлива в смешанном цикле: 6,5–5,1 л/100 км; город: 8,3 – 6,5 л/100 км;
загородный: 5,4 – 4,2 л/100 км; CO 2 Выбросы в смешанном цикле: 116–104 г/км
i20
Бензиновые двигатели
1,25 MPI (75 л.с.): л/км Расход топлива в смешанном цикле: 4,7: 5,1; город: 6,6 — 5,8 л/100 км;
загородный: 4,2 — 4,0 л/100 км; CO 2 Выбросы в смешанном цикле: 119–109 г/км
1,25 MPI (84 л.с.): Расход топлива в смешанном цикле: 5,1–4,7 л/100 км; город: 6,6 — 5,8 л/100 км;
загородный: 4,2 — 4,0 л/100 км; СО 2 Выбросы в смешанном цикле: 119–109 г/км
1,4 MPI (100 л.с.): Расход топлива в смешанном цикле: 6,4–6,2 л/100 км; город: 8,5 — 8,2 л/100 км;
загородный: 5,1 — 4,8 л/100 км; CO 2 Выбросы в смешанном цикле: 148–143 г/км
1.
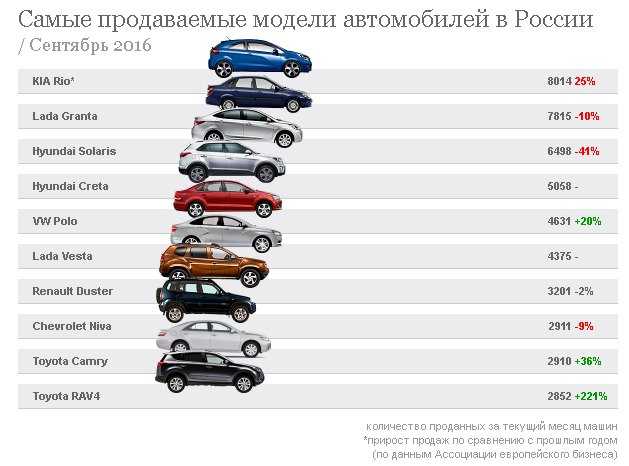
загородный: 3,9 — 3,4 л/100 км; CO 2 выбросы в смешанном цикле: 107–94 г/км
1.0 T-GDi (120 л.с.): Расход топлива в смешанном цикле: 5,0–4,6 л/100 км; город: 6,3 — 5,8 л/100 км;
загородный: 4,2 — 3,9 л/100 км; CO 2 выбросы в смешанном цикле: 115–107 г/км
Дизельные двигатели
1.1 CRDi (75 л.с.): Расход топлива в смешанном цикле: 4,0–3,2 л/100 км; город: 4,9 — 3,4 л/100 км;
загородный: 3,4 — 3,0 л/100 км; CO 2 выбросы в смешанном цикле: 103–83 г/км
1.4 CRDi (90 л.с.): Расход топлива в смешанном цикле: 4,1–3,7 л/100 км; город: 4,9 — 4,5 л/100 км;
загородный: 3,5 — 3,3 л/100 км; CO 2 комбинированные выбросы: 106 — 97 г/км
i30
Бензиновые двигатели
1,4 MPI (100 л.с.): Расход топлива смешанный: 5,6–5,4 л/100 км; город: 6,8 — 6,6 л/100 км;
загородный: 4,9 — 4,8 л/100 км; CO 2 Выбросы в смешанном цикле: 130–126 г/км
1.
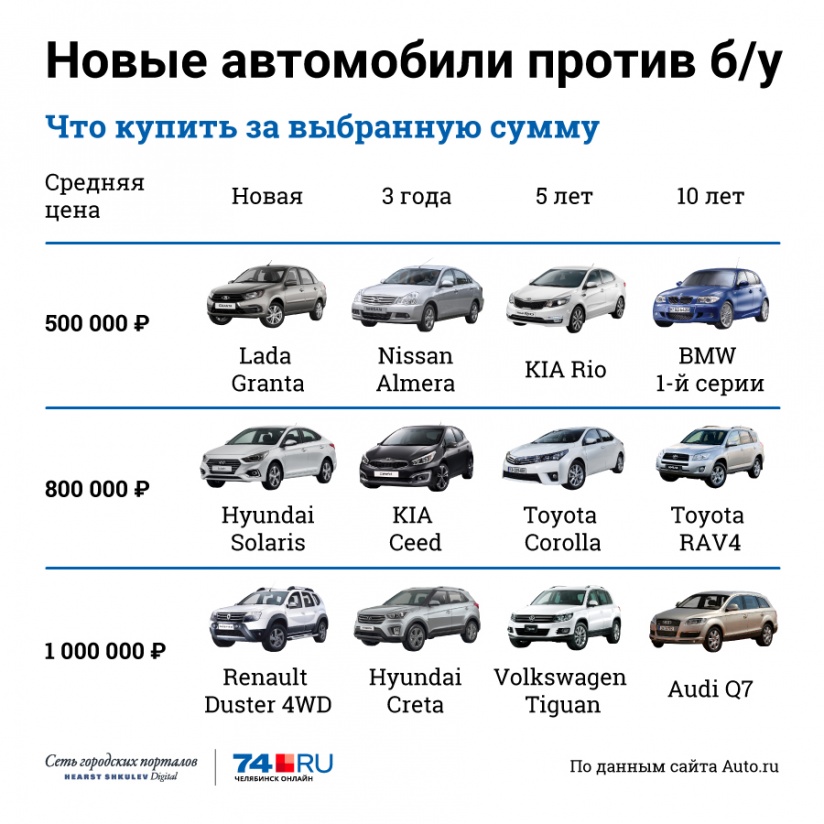
загородный: 4,6 — 4,0 л/100 км; CO 2 Выбросы в смешанном цикле: 115–103 г/км
1.4 T-GDi (140 л.с.): Расход топлива смешанный: 5,5 — 4,8 л/100 км; город: 6,6 — 5,9 л/100 км;
загородный: 5,0 — 4,1 л/100 км; CO 2 Выбросы в смешанном цикле: 125–109 г/км
Дизельные двигатели
1.6 CRDi (95 л.с.): Расход топлива в смешанном цикле: 3,8–3,6 л/100 км; город: 4,1 – 4,0 л/100 км;
загородный: 3,6 — 3,5 л/100 км; CO 2 Выбросы в смешанном цикле: 98–95 г/км
1.6 CRDi (110 л.с.): Расход топлива в смешанном цикле: 4,1–3,4 л/100 км; город: 4,4 – 3,8 л/100 км;
загородный: 3,9 — 3,2 л/100 км; CO 2 Выбросы смешанный: 109–89 г/км
1.6 CRDi (136 л.с.): Расход топлива смешанный: 4,1–3,8 л/100 км; город: 4,4 — 4,2 л/100 км;
загородный: 3,9 — 3,6 л/100 км; CO 2 Выбросы в смешанном цикле: 109 — 99 г/км
*В зависимости от отделки салона и спецификаций шин.
Борьба с ржавчиной на классических и винтажных автомобилях
Борьба с ржавчиной на классических и винтажных автомобилях
- 10 сентября 2021 г.
- Кузовной ремонт, обслуживание автомобилей, реставрация
Ржавчина может стать серьезной проблемой для тех, кто собирает или реставрирует старинные автомобили. Идеальная хромированная и эмалированная краска, на которую вы рассчитывали, внезапно повреждается, и автомобилю может потребоваться капитальный ремонт.
К сожалению, из-за того, как производители конструируют старинные и классические автомобили, ржавчина долгое время была проблемой. Часто из-за используемых металлов и красок многие из этих автомобилей начали ржаветь сразу же несколько десятилетий назад, а через несколько лет у них возникли механические проблемы. Таким образом, многие из этих транспортных средств требуют значительного объема ремонта.
Сегодня почти все автомобили на дорогах изготовлены из оцинкованной стали и в определенной степени защищены от ржавчины. В моделях с 1950-х по 1970-е годы использовалась сталь 22-го калибра без защиты от элементов, которые дает цинк. В результате основная листовая панель особенно подвержена ржавчине.
Типы ржавчины на винтажных и классических автомобилях
При поиске винтажного автомобиля для ремонта вы можете столкнуться со следующими видами ржавчины:
- Поверхностная ржавчина: Вы можете увидеть поверхностную ржавчину, даже если автомобиль хранился в оптимальных условиях хранения. Эта ржавчина развивается в результате оседания влаги на поверхности, что вызывает окисление металла под ней.
- Точечная или чешуйчатая ржавчина: Когда ржавчина проходит ниже поверхности панели кузова, на металле появляются ямки. Более поверхностная проблема, шлифовка и покраска часто могут исправить повреждение.
- Ржавые панели кузова: Некоторые детали могут быть полностью проржавел насквозь . Некоторые, возможно, придется полностью заменить, но другие можно отремонтировать.
Как правило, эта проблема начинается, когда вы замечаете ржавчину и пузыри под нижней дверью, а также спереди и сзади колеса. Любая деталь, проржавевшая до такой степени, что образовалась дыра, должна быть заменена.
При покупке классического или ретро-автомобиля полностью оцените его на наличие ржавчины и возможных структурных проблем. Области, где металл проржавел, как правило, требуют серьезного ремонта, чтобы автомобиль был безопасным и пригодным для использования.
Уход за классическим автомобилем во избежание ржавчины
Из-за риска, связанного с ржавчиной, ваш винтажный или классический автомобиль требует значительного ухода:
- Любые царапины или вмятины на кузове следует немедленно устранить. Из-за металла ржавление может произойти практически мгновенно.
- Подумайте, как вы храните и накрываете свой автомобиль. Никогда не держите его под пластиковым листом, так как под ним будет скапливаться влага, что приведет к образованию ржавчины.