Схема кинематики токарного станка
Токарные станки составляют основную часть станочного парка многих металлообрабатывающих предприятий. Токарные станки используются для обработки внутренних и наружных поверхностей тел вращения. Режущим инструментом выступают резцы, сверла, развертки, зенкера, метчики и плашки. При помощи специальных приспособлений, таких как планшайбы, на токарных станках можно обрабатывать сложные и неправильные формы. Использование специальных устройств расширяет возможности оборудования, позволяет выполнять многие другие операции машинной обработки металла.
Расположение шпинделя — вала, на котором закрепляется патрон с обрабатываемой заготовкой, определяет всю конструкцию станка. Более распространены станки с горизонтальным расположением шпинделя, ими являются токарно-винторезные, револьверные, лоботокарные станки. Вертикальный шпиндель имеют токарно-карусельные станки, они предназначены для обработки низких заготовок большого диаметра.
Строение токарно-винторезного станка
Токарно-винторезные станки имеют максимальные технологические возможности из всего оборудования этой группы, что позволяет их эффективно использовать для изготовления небольших серий изделий. Конструкция этих станков была разработана в первой половине XIX века и с тех пор были внесены только небольшие изменения, касающиеся автоматизации оборудования.
Рис.: 1 – передняя бабка с коробкой скоростей, 2 – гитара сменных колес, 3 – коробка подач, 4 – станина, 5 – фартук, 6 – суппорт, 7 – задняя бабка, 8 – шкаф с электрооборудованием.
Как и у большинства промышленного оборудования, основой этого станка выступает станина. Она выполняется литьем или сваркой и обязательно крепится к полу анкерными болтами. С левой стороны относительно рабочего на станине располагается передняя или шпиндельная бабка. Она представляет собой пустотелый корпус, в котором находятся, шестерни, шпиндель, подшипники, система смазки и переключения диапазонов. На передней панели бабки находятся многочисленные элементы управления станком. Шпиндель выходит из передней бабки в рабочую зону. На шпиндель устанавливаются приспособления для удержания заготовки, основная часть которых — патроны с разным количеством кулачков.
Ниже передней бабки располагается коробка подач. На её передней панели находятся регуляторы для управления подачей. Коробка подач передает вращение на фартук, располагающийся в центральной зоне станка, при помощи вала при обработке поверхностей или винта при нарезке резьбы. Винт располагается над валом, на большей части его длины нарезана червячная спираль. Вал имеет более короткую спираль червячной передачи, но большего диаметра. В фартуке находится механизм, который преобразует вращательное движение вала или винта в возвратно-поступательное движение суппорта.
Суппорт является элементом станка, на котором устанавливается основной инструмент. Нижние салазки суппорта перемещаются по продольным направляющим, расположенным на станине. Сверху находятся верхние салазки, они расположены перпендикулярно к нижним. Перемещающаяся по ним резцовая каретка имеет возможность повтора в горизонтальной плоскости. На ней находится резцедержатель, в котором закрепляется инструмент.
На противоположной стороне станка, с правой стороны, располагается задняя бабка. При обработке длинных заготовок она используется как вторая точка опора, помимо шпинделя. Также на ней размещается инструмент, выполняющий сверление или обработку осевого отверстия в заготовке.
Кинематическая схема токарно-винторезного станка
Главное движение станка осуществляется односкоростным асинхронным трехфазным двигателем, в редких случаях многоскоростным.
Движение с двигателя передается на коробку скоростей посредством клиноременной передачи. В коробке скоростей находится 6-8 валов с зубчатыми колесами. Валы для удобства нумеруются римскими цифрами, первым идет вал со шкивом, далее по кинематике. Выбирая используемые передачи, можно регулировать скорость вращения шпинделя в широких пределах. На токарных станках можно получить более 20 различных скоростей вращения шпинделя с закрепленной на ней заготовкой. Для обратного вращения шпинделя предусмотрены две фрикционные муфты.
Перемещение фартука через коробку подач производится либо напрямую от шпинделя, либо через звено повышения шага, которое находится в коробке скоростей. Оно состоит из трех зубчатых передач, понижающих частоту вращения. Далее находится механизм реверса, который обеспечивает возможность перемещения фартука с суппортом в оба направления.
Коробка подач обладает двумя кинематическими схемами. Первая предназначена для формирования дюймовой резьбы, она содержит одну фрикционную муфту и передает вращение на ходовой винт. Вторая схема предназначена для обработки поверхностей, нарезки метрических резьб. Она передает вращение на ходовой вал. Управление второй цепью производится тремя фрикционными муфтами.
Ряд зубчатых передач находится в фартуке. Они преобразуют вращение вала и винта в передвижение суппорта. Отдельной частью кинематической схемы станка выступает механизм быстрого перемещения суппорта. Он приводится в действие дополнительным электродвигателем посредством ременной передачи.
Предыдущая статья
Следующая статья
Получить консультацию
по инструменту, методам обработки, режимам или подобрать необходимое оборудование можно связавшись с нашими менеджерами или отделом САПР
Также Вы можете подобрать и приобрести режущий инструмент и оснастку к станку, производства Тайваня, Израиля
Отправляя заявку, вы соглашаетесь с политикой конфиденциальности
Проработать технологию, подобрать станок и инструмент
Суппорты для токарных станков | Барановичский завод станкопринадлежностей
БЗСП > Товары > Суппорты > Суппорты для токарных станков
Категория: Суппорты Метка: точение
- Суппорты СУТ 01 и СУТ 06 предназначены для установки на токарные станки модели 16Р25П.
- Суппорты моделей СУТ 02, СУТ 03, СУТ 07, СУТ 08 предназначены для установки на токарные станки моделей МК6046, МК6056 и их модификации.
- Суппорты СУТ 04 и СУТ 05 предназначены для установки на токарные станки модели СА562.
- Суппорты СУТ 09 и СУТ 10 предназначены для установки на токарные станки модели 1К62.
- Суппорты СУТ 11 и СУТ 14 предназначены для установки на токарные станки модели 16К20.
- Суппорт СУТ 12 предназначен для установки на токарные станки модели СА630С.
- Суппорт СУТ 15 предназначен для установки на токарные станки модели СА550.
- Суппорт СУТ 16 предназначен для установки на токарно-винторезные станки модели 1М63.
Суппорты комплектуются четырехпозиционными резцедержателями моделей УГ0101.600.000.000, РДТ-4П или головкой резцовой с пальцевыми фиксаторами ГР 002.
Размеры и технические характеристики
Модель | Тип привода | Тип резцедержателя | h2 | d, h7 | h | S | D | p | K | M | L | H | Масса, кг |
---|---|---|---|---|---|---|---|---|---|---|---|---|---|
СУТ 01 | ручн.![]() | УГ0101.600 | 112 | 80 | 35 | 89 | 185 | 56 | 238 | 225 | 530 | 343 | 44 |
СУТ 02 | ручн. | УГ0101.600 | 115 | 80 | 10 | 92 | 185 | 56 | 238 | 225 | 530 | 318 | 43 |
СУТ 03 | ручн.+мех. | УГ0101.600 | 115 | 80 | 27 | 92 | 185 | 56 | 238 | 225 | 530 | 335 | 43,5 |
СУТ 04 | ручн.+мех. | УГ0101.600 | 120,5 | 80 | 27 | 97,5 | 185 | 56 | 238 | 225 | 530 | 343 | 45 |
СУТ 05 | ручн.+мех. | РДТ-4П | 120,5 | 80 | 27 | 97,5 | 185 | 56 | 238 | 225 | 530 | 342 | 43 |
СУТ 06 | ручн.![]() | РДТ-4П | 112 | 80 | 35 | 89 | 185 | 56 | 238 | 225 | 530 | 343 | 44 |
СУТ 07 | ручн.+мех. | РДТ-4П | 115 | 80 | 27 | 92 | 185 | 56 | 238 | 225 | 530 | 335 | 43,5 |
СУТ 08 | ручн. | РДТ-4П | 115 | 80 | 10 | 92 | 185 | 56 | 238 | 225 | 530 | 318 | 43 |
СУТ 09 | ручн. | УГ0101.600 | 83,5 | 90 | 7,5 | 60,5 | 180 | 56 | 220 | 220 | 497 | 287 | 34 |
СУТ 10 | ручн. | РДТ-4П | 83,5 | 90 | 7,5 | 60,5 | 180 | 56 | 220 | 220 | 497 | 282 | 34 |
СУТ 11 | ручн. | УГ0101.![]() | 86,5 | 80 | 7,5 | 63,5 | 185 | 56 | 220 | 220 | 497 | 292 | 37 |
СУТ 12 | ручн.+мех. | ГР 002 | 168,5 | 90 | 47 | 136,5 | 200 | 68,5 | 310 | 246 | 563 | 436 | 85 |
СУТ 14 | ручн.+мех. | УГ0101.600 | 86,5 | 80 | 25 | 63,5 | 185 | 56 | 238 | 225 | 530 | 311 | 37 |
СУТ 15 | ручн.+мех. | УГ0101.600 | 157 | 80 | 27 | 134 | 185 | 56 | 238 | 225 | 530 | 377 | 76 |
Вам также будет интересно…
Головки резцовые
ПодробнееСуппорт СУТ-16 для токарно-винторезных станков
Подробнее
Штангенциркуль – схема, определение, типы, применение
Содержание
Что такое штангенциркуль?
Штангенциркуль — это прецизионный измерительный инструмент, используемый для точного измерения размеров объекта. Он состоит из двух наборов губок, один набор которых скользит по шкале, а другой остается неподвижным.
Подвижная губка соединена с нониусной шкалой, используемой для точного измерения длины, диаметра или глубины. Основной корпус штангенциркуля состоит из двух рычагов, соединенных шарнирным соединением, позволяющим свободно перемещать нониусную шкалу.
Два плеча градуированы в метрических единицах, таких как миллиметры или сантиметры. На конце одного рычага находится небольшой металлический стержень, известный как нониусный указатель. Этот указатель используется для измерения наименьших приращений шкалы измерений. Другой рычаг штангенциркуля снабжен двумя губками, основной губкой и глубинной губкой.
Основная губка измеряет внешний диаметр объекта, а глубинная губка измеряет глубину отверстия или канавки. Штангенциркуль используется в различных областях, включая машиностроение, механическую обработку, научные исследования и медицину.
Он особенно удобен для измерения небольших объектов, поскольку его точность и прецизионность не имеют себе равных ни у одного другого измерительного инструмента. Он также очень прост в использовании и может измерять расстояния в миллиметрах или сантиметрах.
В целом, штангенциркуль является бесценным измерительным инструментом с высокой точностью и точностью при измерении объектов. Он широко используется во многих отраслях промышленности и является обязательным для любого машиниста или инженера.
Типы штангенциркуля:
Штангенциркуль — это прецизионный измерительный инструмент, используемый для точного измерения размеров объекта. Они обычно используются в машиностроении и производстве для измерения различных параметров, таких как внешний и внутренний диаметр цилиндра, глубина отверстия и толщина листа материала.
На рынке доступно несколько различных типов штангенциркулей, каждый из которых предназначен для измерения различных объектов. Самый распространенный тип штангенциркуля – стандартный. Этот тип штангенциркуля имеет два рычага с фиксированной губкой с одной стороны и подвижной губкой с другой.
Неподвижная губка используется для измерения внешнего диаметра, а подвижная губка используется для измерения внутреннего диаметра. Этот тип штангенциркуля прост в эксплуатации и наиболее часто используется. Штангенциркуль аналогичен стандартному штангенциркулю, но имеет дополнительный рычаг для измерения глубины отверстия или прорези.
Этот тип штангенциркуля измеряет глубину отверстия в цилиндре, глубину выемки или глубину прорези в детали машины. Штангенциркуль предназначен для измерения диаметра круглого предмета. Он имеет две руки с неподвижной челюстью с одной стороны и подвижной челюстью с другой.
Неподвижная губка используется для измерения внешнего диаметра, а подвижная губка используется для измерения внутреннего диаметра. Этот тип штангенциркуля часто используется для измерения диаметра круглого вала или цилиндра. Цифровой штангенциркуль — это более совершенный тип штангенциркуля, оснащенный цифровым дисплеем.
Этот тип штангенциркуля измеряет различные параметры, такие как внутренний и внешний диаметры, глубины и углы. Он более точен, чем стандартный штангенциркуль, и часто используется в точном машиностроении или производстве. 9Штангенциркули 0007 — бесценный инструмент для точного измерения размеров различных объектов в машиностроении и производстве. Различные штангенциркули предназначены для измерения различных объектов и используются в различных приложениях.
Использование штангенциркуля:
Использование штангенциркуля — это простой процесс, который можно использовать для измерения объектов размером от малого до большого. Он часто используется в машиностроении, столярном деле и механообработке.
Штангенциркуль может измерять длину, глубину, толщину и диаметр объектов. Он состоит из двух наборов челюстей, одного стационарного и одного подвижного, которые открываются и закрываются на объекте для измерения его размеров.
Шкала нониуса расположена на штангенциркуле, что дает точное считывание сделанных измерений. Чтобы использовать штангенциркуль, объект, который измеряется, должен быть помещен между губками штангенциркуля.
Челюсти должны быть достаточно широкими, чтобы вместить объект, но не настолько широкими, чтобы он мог двигаться. Как только объект находится на месте, подвижную челюсть можно переместить к неподвижной челюсти, чтобы закрыть суппорт на объекте.
В этот момент объект следует крепко удерживать на месте, чтобы измерение было точным. Затем можно использовать шкалу нониуса на штангенциркуле для получения точных показаний измерения. Шкала Вернье состоит из двух наборов линий, одна из которых представляет собой мажорную шкалу, а другая — шкалу Вернье.
Шкала нониуса разделена на более мелкие деления, чем основная шкала, и может использоваться для получения более точных показаний. Точное измерение объекта может быть выполнено путем совмещения двух наборов линий. После выполнения измерения штангенциркуль можно использовать для измерения других объектов.
Процесс тот же, но измерения будут различаться в зависимости от размера объекта. Важно помнить, что всегда следует читать шкалу нониуса слева направо при проведении измерений. Использование штангенциркуля — это простой и точный способ измерения размера и формы объектов.
Он часто используется в различных инженерных и механических приложениях и может использоваться для измерения объектов различных размеров. Немного потренировавшись, любой может быстро научиться пользоваться штангенциркулем.
Техническое обслуживание и уход за штангенциркулем:
Штангенциркуль — это прецизионный инструмент, который используется для точных измерений длины, ширины и диаметра объекта. Надлежащее техническое обслуживание и уход за штангенциркулем необходимы для обеспечения точных и надежных измерений.
Во-первых, важно всегда хранить штангенциркули в чистом, сухом и непыльном месте. Это поможет предотвратить попадание грязи или пыли в механизм и вызвать неточные показания.
Кроме того, важно оберегать суппорты от любых химикатов или растворителей, так как они могут вызвать коррозию металлических компонентов. Во-вторых, регулярно проверяйте суппорты, чтобы убедиться, что все детали находятся в рабочем состоянии.
Убедитесь, что все винты, болты и гайки затянуты правильно, а губки суппортов чистые и на них нет мусора. Также проверьте состояние шкалы и стрелки и убедитесь, что градуировка четкая и разборчивая.
В-третьих, для поддержания точности штангенциркуля необходимо смазывать движущиеся части. Используйте легкое масло или консистентную смазку для смазывания губок, шкалы и иглы. Это поможет обеспечить плавную и точную работу суппортов.
Схема дискового тормоза
Обновлено: 17 октября 2022 г.
Как работают дисковые тормоза: посмотрите на схему; на нем показана схема дискового тормоза с плавающим суппортом, которая является наиболее распространенной конструкцией в современных автомобилях. Тормозной диск или «ротор» (зеленая часть) устанавливается на ступицу. Колесо (здесь не показано) установлено на той же ступице. Тормозной диск вращается вместе с колесом. Схема дискового тормоза. Увеличенное изображение. Тормозной суппорт (синяя часть) неподвижен.
Две тормозные колодки, внутренняя и внешняя, устанавливаются внутри кронштейна с обеих сторон ротора. Тормозные колодки также могут скользить вбок (к диску и от него) на кронштейне.
Когда водитель нажимает на педаль тормоза, главный тормозной цилиндр, прикрепленный к педали тормоза, создает давление в гидравлической тормозной системе. Тормозная система передает давление тормозной жидкости по магистралям и шлангам на тормозные суппорты на каждом колесе.
Суппорт имеет один или два поршня. Под давлением поршень выдвигается и толкает внутреннюю тормозную колодку к тормозному диску. Противодействующая сила отталкивает суппорт от диска, а внешний конец суппорта толкает внешнюю колодку к диску.
В результате внутренняя и внешняя тормозные колодки сдавливают между собой тормозной диск. Эта прижимная сила замедляет вращение диска (и колеса) или полностью останавливает его. Кинетическая энергия движущегося автомобиля переходит в тепловую. Большинство передних тормозных дисков вентилируются для лучшего отвода тепла.
Когда вы приносите автомобиль на обслуживание, включающее, помимо прочего, осмотр тормозов, механики проверяют толщину фрикционного материала колодок и состояние тормозного диска, в том числе его толщину (см. схему). Тормоза обычно заменяют, когда толщина фрикционного материала колодки становится слишком низкой, как на этом фото.
Старые тормозные колодки и диски часто изнашиваются неравномерно, с канавками и гребнями. Новые тормозные колодки плоские.
Обработка тормозного диска на токарном станке.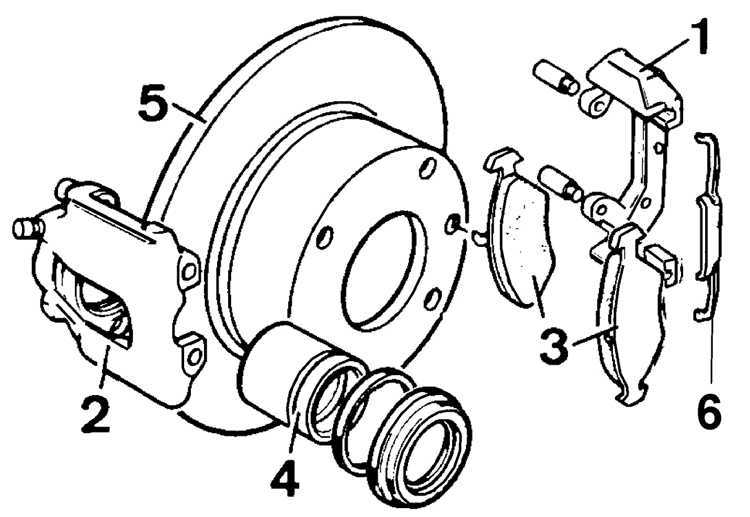
Для восстановления поверхности или «механической обработки» дисков механики используют тормозной токарный станок , который может срезать тонкие слои металла с обеих сторон рабочих поверхностей тормозных дисков, чтобы сделать их плоскими и однородными. В некоторых магазинах есть переносные токарные станки для тормозов (автомобильные токарные станки), которые могут шлифовать тормозные диски, не снимая их с автомобиля.
Восстановление поверхности по сравнению с заменой тормозных дисков:
Установлен новый OEM тормозной диск с новыми колодками Замена тормозных дисков оригинальными или качественными запасными частями является предпочтительным вариантом, поскольку шлифовка делает диски тоньше и требует больше затрат на оплату труда.Если новые диски слишком дороги или недоступны, замена старых дисков позволяет сэкономить деньги.
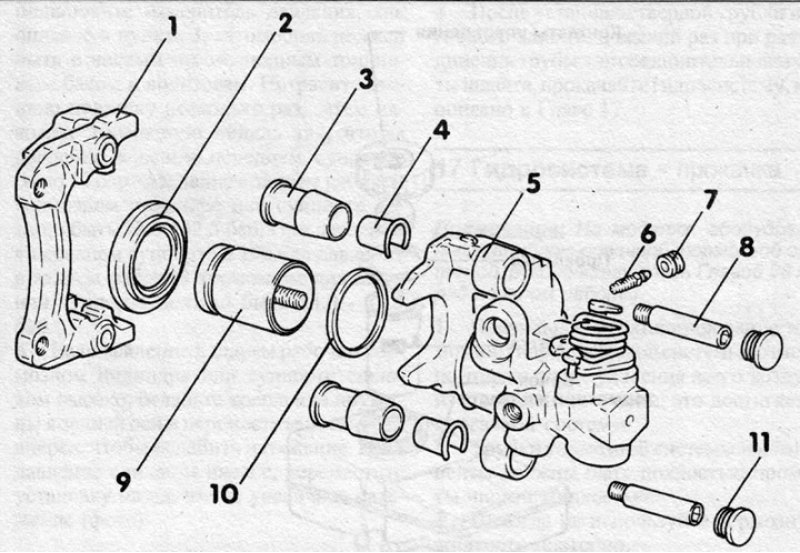