Система смазывания и охлаждения — Технарь
Система смазывания станка должна обеспечивать непрерывную или периодическую подачу к трущимся поверхностям смазочного материала в количестве, достаточном для того, чтобы между этими поверхностями сохранилась по возможности непрерывная пленка смазки, и чтобы температура этих поверхностей была в установленных пределах. Смазывание способствует уменьшению трения, потерь энергии, изнашивания и нагрева трущихся поверхностей, увеличению долговечности станка, плавности и бесшумности работы передач, повышению КПД, длительному сохранению точности.
Системы смазывания в станках подразделяют на индивидуальные, когда отдельные механизмы смазывают независимо друг от друга, и централизованные, когда точки смазывания объединены. Централизованную систему смазывания применяют в тех случаях, когда сборочные единицы станка не изменяют относительного расположения и можно использовать один смазочный материал.
Схема автоматической централизованной системы смазывания зубострогального станка 5А250 показана на рис.
Точки 1—3 являются распределительными. Очистка масла от мельчайших твердых частиц и грязи осуществляется пятью фильтрами (Ф1 — Ф5). Смазывание может осуществляться самотеком, циркуляционным способом или под давлением. Для централизованной системы смазывания применяют шестеренные и пластинчатые насосы с постоянной подачей жидкости. Очищают масло от мельчайших твердых частиц и грязи пластинчатыми, войлочными, сетчатыми и магнитными фильтрами.
Для смазывания быстроходных шпинделей и других сборочных единиц станка находит применение смазывание масляным туманом. Достоинством этого вида смазывания является то, что воздух, который используется для распыления масла, уносит тепло, возникающее в результате трения, и расход масла значительно меньше, чем при обычном смазывании, а также практически отсутствует утечка масла через соединительные места и зазоры. Это дает возможность сократить количество уплотнительных устройств.
При смазывании перемещающегося механизма масляным туманом (рис. 2.39) воздух под давлением проходит через влагоотделитель 2, осушитель 3, реле давления 4, регулятор давления 5 и попадает в маслораспылитель 6, откуда образованный масляный туман по шлангу 7 через распределитель 8 поступает к механизму станка 1. Использованное масло через воронку .9 стекает в сборник 10 масляного конденсата.
Систему охлаждения применяют для подачи смазочно-охлаждающей жидкости к режущим кромкам инструмента в процессе резания, что способствует повышению производительности при работе на станке. К наиболее распространенным методам подачи смазочно-охлаждающей жидкости в зону резания относятся: подача СОЖ поливом струей (рис. 2.40, а), под давлением (рис. 2.40, б), под давлением по специальным каналам в теле инструмента (рис. 2.40, в), в распыленном состоянии, через специальные оправки инструмента и поры шлифовального круга. При поливе свободно падающей струей смазывающее действие жидкости снижено, так как она почти не попадает в зону контакта инструмента с изделием и со стружкой. Кроме того, имеет место сильное разбрызгивание жидкости. Лучший результат получается при подаче жидкости под давлением с направлением струи в зону резания.
Система смазки и охлаждения — WIKA Россия
Уровень в резервуаре со смазочно-охлаждающей жидкостью и ее концентрация меняются из-за испарения на инструменте, из-за удаления с него стружки смазочно-охлаждающей жидкостью и из-за остатков инородных масел.
В больших металлообрабатывающих компаниях зачастую работники вынуждены ежедневно вести учет уровня и контролировать восполнение объема смазочных материалов. В контексте промышленной концепции 4.0 (четвёртая промышленная революция) автоматическое измерение и документирование уровня дает несколько преимуществ. В дополнение к восполнению запаса по мере необходимости осуществляется документирование потребления охлаждающе-смазочных материалов, на основе которого можно определить изменения объема (например, в результате утечек). При обработке заготовки смазочно-охлаждающая жидкость нагревается. Это тепло должно отводиться теплообменниками. Необходимо точно соблюдать температурные пределы (спецификации производителя). С помощью простого предельного выключателя можно контролировать максимальную температуру, а термометра сопротивления — температуру эмульсии в резервуаре. Таким образом можно применять охлаждение только тогда, когда оно необходимо, что позволяет значительно снизить потребление электроэнергии.
Техническим регламентом TRGS 611 предписывается регулярный контроль и документирование состояния смазочно-охлаждающей жидкости:
- Нормативы, касающиеся значения рабочей концентрации; на практике обычно 4 … 8 % (переносной рефрактометр)
- Проверка значения pH (индикаторная бумага pH)
- Определение содержания нитритов (индикаторные полоски)
- Определение температуры
- Количество микроорганизмов (до настоящего момента, без ограничений или стандартных значений)
Текущий норматив касается проводимых на объекте измерений, с последующим вводом в таблицу на бумажном носителе вручную. Компания WIKA работает над претворением в жизнь промышленной концепции 4.0 в области автоматического документирования этих измеренных значений. Помимо того, что это позволяет отказаться от проводимых вручную измерений, более частые измерения позволяют на ранней стадии предупредить перегрев смазочно-охлаждающей жидкости. Жидкость затем можно отвести из контура и тем самым избежать ее замены.
Автоматическая система смазки – путь снижения простоев технологического оборудования
А.И.Госманн, к.т.н., Lincoln GmbH & Co. KG (Германия)
В настоящее время при разработке месторождений полезных ископаемых применяется мощное и дорогостоящее землеройное и погрузочное оборудование. Специалистами горнодобывающих предприятий и учеными постоянно проводится большая работа по внедрению передовых методов, позволяющих до минимума сократить время простоев техники. Одним из эффективных способов снижения «непроизводительных простоев» технологического оборудования является, как указывалось в статье «Пути снижения простоев технологического транспорта», (авт.
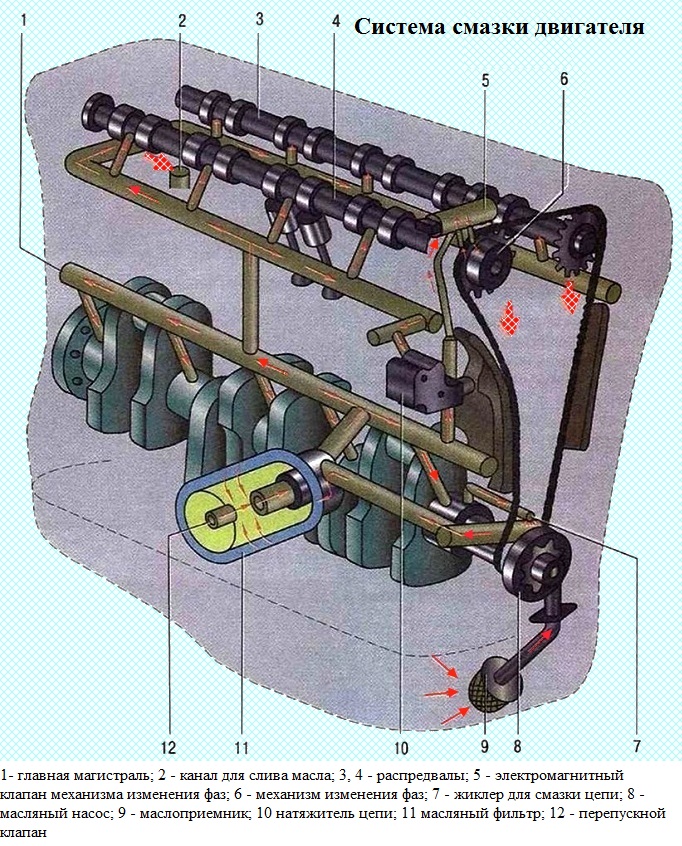
Шагающий экскаватор ЭШ 15.90 (заводской №23)
на карьере AS «Narva Karjaar»
Кроме того, при разработке АСС для экскаваторов ЭКГ-5А и ЭКГ-20 (ОАО «ОМЗ-Горное Оборудование») была разработана принципиально новая система смазки, позволяющая все труднодоступные и трудоёмкие точки трения смазывать во время работы.
В настоящее время на практике была показана целесообразность применения АСС на землеройной и погрузочной технике. С этой целью на карьере AS «Narva Karjaar» (Эстония) были проведены сравнительные испытания двух шагающих экскаваторов ЭШ 15.90 (ОАО «ОМЗ-Горное Оборудование»), один из которых (заводской №23) был оснащён автоматической системой смазки фирмы
Lincoln, а другой (заводской №24) – штатной системой смазки.
Предложенная фирмой Lincoln система смазки обеспечивала автоматическое смазывание следующих узлов экскаватора:
• открытых передач;
• центральной цапфы;
• шестерни-венца поворотной платформы;
• рельсов и поверхностей роликов;
• узлов механизма шагания.
Смазка этих узлов производилась в автоматическом режиме во время работы экскаватора.
Смазывание же осей роликов роликового круга (102 шт.) осуществлялось от насосной станции АСС во время смены экипажей. При этом все 102 ролика смазывались с одной позиции в течение 15–20 минут.
Из приведенных ниже результатов сравнительных испытаний (табл. 1) видно, что более высокая стоимость применяемого смазочного материала фирмы Addinol типа LM 2EP вполне может быть компенсирована низким её расходом и значительным сокращением времени на проведение смазочных работ.
Табл. 1 Результаты сравнительных испытаний различных систем смазки
на экскаваторах ЭШ 15.90 (на карьере AS «Narva Karjaar»)
Подача смазки к парам трения производилась от насоса с пневмоприводом, который устанавливался непосредственно в 50-ти литровую ёмкость. Основное преимущество применения такого «бочечного» насоса состоит в том, что при подаче смазки к парам трения полностью исключается попадание загрязнения к трущимся поверхностям.
Специалисты карьера AS «Narva Karjaar» высоко оценили АСС фирмы Lincoln, установленную на шагающем экскаваторе ЭШ 15.90, и, наравне с указанными выше преимуществами применения автоматической смазочной системы, отметили также следующие положительные стороны ее использования:
1. Строго дозированная подача смазки к парам трения позволяет сократить количество и номенклатуру применяемых смазок. Месячная экономия смазочного материала на один экскаватор составляет 141.
2. Отсутствие контакта человека со смазочным материалом повышает культуру производства и предотвращает наружное загрязнение экскаватора маслами.
3. Контейнерная замена смазочных ёмкостей и замкнутость АСС исключает попадание загрязнения в смазку и, тем самым, способствует увеличению рабочего ресурса смазываемых поверхностей.
4. Использование АСС позволяет увеличить время производительной работы экскаватора примерно на 1.2 часа в сутки за счёт сокращения времени на проведение смазочных работ.
Принципиальная схема АСС на ЭШ 15.90
В заключение, нам бы хотелось ещё раз подчеркнуть основные преимущества применения автоматических систем смазки:
• надёжно обеспечивает смазкой отдельные узлы оборудования;
• исключает возможность попадания загрязнения в пару трения;
• сокращает время на проведение ТО;
• сокращает расход запасных частей и ГСМ;
• повышает готовность машины к работе;
• облегчает и упрощает труд оператора;
• обеспечивает экономию энергоресурсов.
Журнал «Горная Промышленность» №6 2002
Система смазки двигателя
В современных двигателях смазка трущихся частей, как правило, производится по циркуляционной системе под давлением, создаваемым насосом. Иногда циркуляционной смазке под давлением сопутствует смазка разбрызгиванием. Тогда такую систему смазки именуют
смешанной.
Указанные системы смазки предполагают наличие следующих элементов:
насосов, обеспечивающих циркуляцию масла под давлением;
фильтров, а иногда и центробежных сепараторов, служащих для очистки масла от примесей, появляющихся при разложении самого масла и изнашивании деталей;
масляных холодильников или радиаторов, где масло охлаждается;
редукционных устройств, позволяющих регулировать давление масла в системе;
маслопроводов и маслосборника. Последний служит для сбора масла, которое затем вновь забирается насосом в систему смазки.
На фиг. 143 дана схема смешанной системы смазки. Масло циркулирует в двигателе под давлением, создаваемым шестеренчатым насосом 5, засасывающим масло из поддона 4 картера через сетчатый маслоприемник 6. Это масло нагнетается через маслопровод 3, фильтр грубой очистки 1, полость колпака фильтра тонкой очистки 10 и через холодильник 7 (в данном случае радиатор). Только небольшая часть масла пропускается через фильтр тонкой очистки и стекает по центральному каналу в поддон. Затем охлажденное масло поступает к подшипникам коленчатого вала, от которых но сверлениям в коленчатом валу поступает к шатунным подшипникам и от них по каналам в теле шатунов па смазку поршневых пальцев. Масло, как это видно из схемы, подается также для смазки подшипников распределительного вала, шестерни 8 привода топливного насоса и коромысел 9 клапанов. Если давление масла в магистрали превысит заданное, сработает редукционный клапан 2 и часть масла перепустится обратно в поддон. Рабочая поверхность цилиндра, зубья шестерен смазываются маслом, вытекающим из зазоров подшипников и разбрызгиваемым кривошипно-шатунным механизмом.
В отличие от приведенной системы смазки, где нижняя часть картера используется в качестве маслосборника, в некоторых типах двигателей применяется система смазки с сухим картером.
Здесь сливающееся в картер масло отводится из него в специальный масляный бак. Систему с сухим картером особенно часто применяют в форсированных двигателях, чем избегают сильного пенообразования в картере.
Масляные насосы в подавляющем большинстве двигателей шестеренчатого типа; принцип их действия был рассмотрен выше. Распространенность таких насосов объясняется простотой, надежностью в работе и равномерностью подачи.
Если система смазки предусматривает несколько шестеренчатых насосов, то их обычно компонуют в один агрегат из нескольких секций шестеренчатых пар). На фиг. 144 представлен трехсекционный шестеренчатый насос двигателя с сухим картером. Две верхние секции насоса отсасывают стекающее в картер масло и направляют его в бачок, из которого третья секция насоса подает масло в систему смазки. Привод насоса осуществляется шестерней 1 сидящей на оси 7 валика ведущих шестерен.
Масло из картера в верхнюю секцию проходит через сетку 2 и окно 11, а в среднюю секцию через отверстие 10, куда масло подводится по трубопроводу, также снабженному сеткой. Из обеих секций масло выходит в отверстия 3 и 5 и через штуцер 4 направляется в масляный бачок. Из бачка масло через штуцер 9 засасывается нижней секцией и через штуцер 6 подается в масляные фильтры. В приливе нижней крышки насоса расположен редукционный клапан 8.
На фиг. 145 показан лубрикатор золотникового типа, а на фиг. 146 —схема действия насосного элемента лубрикатора.
На вертикальном валу 5 (фиг. 145), приводимом во вращение от червячной шестерни 6, имеются фигурные шайбы 1 и 2, заставляющие работать ряд насосных элементов, укрепленных на неподвижной плите 8. Каждый насосный элемент состоит из плунжера 3 и золотника 4. За один поворот вертикального вала 5 фигурная шайба 1 заставляет плунжеры 3 совершать два возвратно-поступательных движения, а фигурная шайба 2 одно возвратно-поступательное движение золотников 4.
На фиг. 146, а показан момент, когда рабочий плунжер 1 совершает ход нагнетания, и золотник 2 расположен так, что масло нагнетается через канал 4 к месту смазки. Когда плунжер двигается вверх, совершая всасывающий ход, положение золотника дает возможность маслу по каналу 3 перейти в подплунжерное пространство (фиг. 146, б). При следующем рабочем ходе плунжера (фиг. 146, в) золотник, продолжая подниматься, соединяет подплунжерное пространство с каналом 5, по которому масло поступит к контрольному отводу. Этот отвод показывает количество масла, поступающего к парному с ним рабочему отводу, соединенному с каналом 4. После положения, показанного па фиг. 146, в, следует ход всасывания. Далее цикл повторяется. Количество подаваемого масла можно регулировать повертыванием винта 12 (фиг. 145), изменяющие ход плунжера. Масло заливается в корпус лубрикатора через сетку 14, открывая крышку 13.
Привод червячной шестерни 6 и вертикального вала 5 осуществляется через храповик 9 и червяк 7. Для прокачивания масла до пуска двигателя служит рукоятка 11, связанная с валикам 10 червяка 7.
На фиг. 147 представлен один из типов редукционного клапана. Клапан 1 плотно сидит па своем седле, прижимаемый пружиной 2, натяжение которой регулируется винтом 3. В. случае, если в магистрали давление масла превысит силу натяжения пружины, то клапан откроет проход маслу в картер.
Фильтры масляной системы включаются в масляную магистраль, как правило, до холодильника, так как нагретое масло имеет меньшую вязкость, а следовательно, получается меньшее сопротивление при фильтрации. Фильтры часто делаются сдвоенными, что дает возможность очищать один из них при работе другого. Конструкции фильтров весьма разнообразны и зависят от мощности, быстроходности двигателей и сорта применяемого смазочного масла. В тихоходных стационарных двигателях обычно ограничиваются грубой фильтрацией. Быстроходные дизели требуют более тщательной фильтрации масла. Здесь часто фильтры состоят из двух фильтрующих устройств. В первом производится грубая (предварительная) очистка масла от механических примесей, во втором — тонкая очистка. Фильтрующим элементом при грубой очистке служит металлическая сетка или щели. На напорных магистралях тихоходных двигателей фильтрующие сетки имеют 50—200 отверстий па 1 см2, а в быстроходных — до 10 000. В щелевых фильтрах масло очищается при проходе его через щели шириной 0,03—0,1 мм. Фильтры грубой очистки включаются в систему последовательно, и через них пропускается все циркулирующее в системе масло. Фильтры тонкой очистки включаются в масляную систему параллельно, и через них пропускается только часть масла (до 20%), которая в маслосборнике смешивается с остальным маслом. Так, на схеме (фиг. 143) количество масла, пропускаемое через фильтр тонкой очистки 10, определяется калиброванным отверстием в стяжном болте 11.
Фильтрующим элементом в фильтрах тонкой очистки могут служить войлок, ткани и другие волокнистые вещества. Наибольшее распространение получили картонные фильтры типа АСФО.
На фиг. 148 представлен сменный фильтрующий элемент картонного фильтра АСФО. Он представляет собой щелевой фильтр, состоящий из набора картонных пластин 6, между которыми установлены прокладки 4. Между пластинами образуются пространства, отделенные друг от друга ребрами прокладок. На ребрах выдавлены лучевые канавки 5, выходящие открытым концом в центральное отверстие элемента. Стяжка элемента осуществляется с помощью стяжек 1 и 3 и двух колец 2.
Масло, поступающее в корпус фильтра, просачивается между пластинами 6 и прокладками 4, заполняет пространство между ними и затем просачивается в щели между пластинами и ребрами, попадая на лучевые канавки 5. По канавкам масло проходит в центральное отверстие элемента, откуда отводится по центральной трубке корпуса фильтра. Механические примеси, смола, кокс и пр. задерживаются между пластинами и ребрами.
На фиг. 149 представлен комбинированный масляный фильтр двойной очистки. Насосом масло подается внутрь корпуса 1 фильтра.
В качестве фильтров грубой очистки здесь помещены двойные ленточные щелевые фильтры 4 и 3, где в щелях, образованных ленточной навивкой, остаются частицы механических примесей, размер которых превышает размер щели. Основная часть масла направляется в двигатель через щелевые фильтры по путям, указанным стрелками. Небольшая же часть масла, пройдя элемент тонкой очистки 5, проходит через сверление в стяжном стержне 2 и отводится в, картер.
Количество масла, прокачиваемое в единицу времени через систему смазки, зависит от количества отводимого ею тепла и примерно соответствует 2—8 л/л. с. ч. Для обеспечения указанной интенсивности циркуляции давление в системе смазки составляет:
для тихоходных двигателей с воспламенением от сжатия……… ……………………………………………..0,8—1,8 кГ/см2
для быстроходных карбюраторных двигателей и двигателей с воспламенением от сжатия…………………..2—5 кГ/см2
для двигателей повышенной мощности и быстроходности………………………………………………………6—9 кГ/см2
Удельный расход масла (как следствие испарения и выгорания) примерно составляет 2—10 г!л. с. ч
Для различных типов двигателей внутреннего сгорания выпускается большой ассортимент смазочных масел. Для смазки цилиндро-поршиевой группы и подшипников тихоходных дизелей, а также для газовых и калоризаторных двигателей применяются моторные масла марки Т (ГОСТ 1519-42). Для смазки быстроходных дизелей применяются в соответствии с ГОСТом 5304-54 дизельные масла марок Дп-8, Д-11, Дп-14, Для высокооборотных быстроходных дизелей и карбюраторных двигателей с подшипниками из свинцовистой бронзы используются авиационные масла марок МС-14, МС-10 и МС-24 (ГОСТ 1013-49).
Для компрессоров низкого давления и двухступенчатых компрессоров среднего давления применяется компрессорное масло марки 12 (М), а для многоступенчатых компрессоров повышенного давления — марки 19 (Т) (ГОСТ 1861-54).
В табл. 14 (стр. 245) приведены некоторые физико-химические свойства масел, указанных выше.
Для достижения минимального расхода масла при эксплуатации двигателя следует пользоваться смазочным маслом, рекомендуемым заводом-изготовителем.
При циркуляционной системе смазки в условиях нормальной эксплуатации двигателя замену масла обычно производят через следующее число часов:
у тихоходных двигателей…………………………………………………. от 250 до 750;
у быстроходных двигателей …………………………………………….. » 100 » 300
Длительность работы масла может быть значительно увеличена при использовании масляных фильтров тонкой очистки и периодической сепарации масла. Показателем необходимости смены масла в тихоходных дизелях обычно считается увеличение содержания механических примесей — до 1,5%, кокса —до 3% и температура вспышки в открытом сосуде ниже 150° С.
Система смазки — Энциклопедия по машиностроению XXL
В состав ГТУ обычно входят камера сгорания, газовая турбина, воздушный компрессор, теплообменные аппараты различного назначения (воздухоохладители, маслоохладители системы смазки, регенеративные теплообменники) и вспомогательные устройства (маслонасосы, элементы водоснабжения и др.). [c.174]В большинстве машин и механизмов предусматривается специальная, надежно действующая система смазки. [c.251]
Применяют циркуляционные системы смазки со специальными холодильниками (рис. 9.10, й). [c.185]
Задача IX—28. Определить избыточное давление на входе в шестеренный насос системы смазки, подающий Q = 60 л/мип масла при температуре i = 20° С (кинематическая вязкость масла v = 2 Ст, относительная плотность 6 = 0,92), [c.254]
Наилучшее решение с точки зрения надежности и удобства эксплуатации — это полностью автоматизированная система смазки, не требующая периодической смены масла. Это достижимо, если предусмотреть мерь , противодействующие окислению и тепловому перерождению масла и обеспечивающие непрерывную очистку и регенерацию масла. [c.41]
В системы смазки необходимо вводить аварийные устройства, обеспечивающие подачу масла, хотя бы,в минимальных количествах, при выходе из строя главной системы. [c.41]
Модифицирование машины для работы в. различных климатических условиях. сводится преимущественно к замене материалов. В машинах, работающих в жарком и влажном климате (машины тропического исполнения), применяют коррозионно-стойкие сплавы, в машинах, эксплуатируемых в областях с суровым климатом (машины арктического исполнения), — хладостойкие материалы системы смазки приспосабливают к работе при низких температурах. [c.49]
При компоновании должны быть учтены все условия, определяющие работоспособность агрегата, разработаны системы смазки, охлаждений сборки-разборки, крепления агрегата и присоединения к не у смежных деталей (приводных валов, коммуникаций, электропроводки), предусмотрены условия удобного обслуживания, осмотра и регулирования механизмов выбраны материалы для основных деталей продуманы способы повышения долговечности, увеличения износостойкости трущихся соединений, способы защиты от коррозии исследованы возможности форсировки агрегата и определены ее границы. [c.83]
Опоры с трением скольжения имеют следующие преимущества они могут работать при высоких скоростях и нагрузках в агрессивных средах малочувствительны к ударным и вибрационным нагрузкам их можно устанавливать в местах, недоступных для установки подшипников качения, например на шейках коленчатых палов. К основным недостаткам опор с трением скольжения относятся более высокие потери на трение при обычных условиях усложненные системы смазки тяжело нагруженных, быстроходных подшипников необходимость постоянного контроля за смазкой (исключение представляют приборные подшипники из фторопласта и капрона, а также металлокерамические подшипники), необходимость применения дефицитных материалов и высокой поверхностной твердости цапф износ большие осевые габариты. [c.426]
Схемы гидравлических и пневматических приводов, системы смазки, охлаждения и топливных систем должны отвечать общим требованиям ГОСТ 2.701 —68 правила выполнения их структурных, принципиальных и схем соединений представлены в ГОСТ 2.704-68. [c.200]
Для выбора системы смазки определяют значение у ра = 9,8- 3,93 = = 25 следовательно, допустима кольцевая смазка. Одна из типичных конструкций подшипника показана на рис. 24, где представлена также схема расположения кольца и даны его примерные размеры для подшипников с d = = 20 120 мм D SS (2ф 1,5) d А = (6 15) мм Я = h+ (2 3) мм S = = (2в>5) мм t= (0,25а.0,15) D (первое значение указанных размеров относится к валу меньшего диаметра). [c.444]
К основным недостаткам подшипников скольжения относятся высокие потери на трение усложненные системы смазки и необхо-диг.юсть постоянного контроля ее наличия необходимость применения дефицитных материалов и высокой поверхностной твердости цапф износ большие осевые габариты. [c.518]
Смазка подшипников агрегата осуществляется от общей системы смазки турбины К-300-240. [c.243]
Пуск агрегата. Пуск и остановка агрегата осуществляются с блочного или группового щита. При индивидуальной системе смазки после поступления импульса от ключа управления или АВР включается в работу пусковой маслонасос. Когда в конце масляной магистрали будет создано давление около 0,07 МПа (0,7 кгс/см ), по импульсу от контактного манометра включается масляный выключатель приводного электродвигателя. Пуск насосного агрегата с гидромуфтой производится при полном заполнении маслом гидромуфты. В этом случае нагрузка на черпак будет минимальной. После выхода электродвигателя на номинальную частоту вращения по показаниям контрольно-измерительных приборов необходимо убедиться в нормальной работе насоса. На действующем насосе следует прослушать работу его узлов и убедиться в отсутствии стуков, шумов и т. п. При пуске на незаполненный трубопровод следует, постепенно открывая байпас напорной задвижки, вытеснить воздух и создать давление на нагнетательном трубопроводе, после чего открыть напорную задвижку. [c.253]
В системах смазки питательных насосов, дымососов и другого оборудования электростанций используется шестеренные и винтовые насосы. Наибольшее применение нашли шестеренные насосы. [c.287]
Задача 3.46. В напорную линию системы смазки двигателя внутреннего сгорания включена центрифуга, выполняющая роль фильтра тонкой очистки масла от абразивных и металлических частиц. Ротор центрифуги выполнен в виде полого цилиндра, к которому подводится масло под давлением ро = 0,5 МПа, как показано на схеме, а отводится через полую ось, снабженную отверстиями. Часть подводимого масла вытекает через два сопла, расположенные тангенциально так А—/4), что струи масла создают реактивный момент, вращающий ротор. Определить скорость истечения масла через сопла (относительно ротора) и реактивный момент при частоте вращения ротора я = 7000 об/мин. Диаметр отверстий сопл do = 2,5 мм [х = ф = 0,65 расстояние от оси отверстий до оси вращения ротора/ = 60 мм р =900 кг/м . Считать, что в роторе масло вращается с той же угловой скоростью, что и ротор. [c.65]
Задача 7.13. Система смазки двигателя внутреннего сгорания сводится к эквивалентному трубопроводу длиной / = 0,25 м и диаметром d = мм с местным сопротивлением в виде отверстия в толстой стенке с диаметром do = 2 мм. [c.159]
Вода имеет теплоемкость в два раза, а коэффициент теплопередачи в пять раз больше по сравнению с маслом, что улучшает процесс теплообмена и охлаждения. Вода не дает устойчивого пено-образования. Она может с успехом применяться в судовых установках, однако применение ее как рабочей жидкости встречает возражения из-за усложнения системы защиты подшипников, из-за разделения системы смазки и питания, а также из-за коррозионного действия ее на некоторые металлы. Вследствие применения и обработки дополнительных деталей, а также применения более дорогих и дефицитных металлов и материалов, не подвергающихся коррозии, использование воды удорожает конструкцию гидродинамической передачи. [c.13]
Для отделения узла подшипника от общей системы смазки применяют маслосбрасывающие кольца 3, предохраняющие пластичные смазочные материалы от вымывания (см. рис. 16.17). Они вращаются вместе с валом кольцо имеет 2—4 канавки треугольного сечения зазор между кольцами и корпусом (стаканом) 0,1…0,3 мм. Кольца должны выходить за стенку корпуса (стакана) на 1…2 мм. [c.334]
Система смазки в двигателях обеспечивает не только подачу масла к трущимся поверхностям, уменьшение потерь на трение, увеличение долговечности деталей и охлаждение их, но также и удаление с трущихся поверхностей продуктов износа. Слой смазки на поршне и поршневых кольцах способствует уплотнению цилиндра. [c.422]
Рис. 2.27. Циркуляционная система смазки ГТД |
При проектировании и расчете машины закладывается ее надежность. Она зависит от конструкции машины и ее узлов, применяемых материалов, методов защиты от различных вредных воздействий, системы смазки, приспособленности к ремонту и обслуживанию и других конструктивных особенностей. [c.7]
Однако жидкостное трение обладает рядом недостатков. Во-первых, оно связано с существенным усложнением конструкции системы смазки. Во-вторых, наличие масляного слоя между поверхностями, величина которого зависит от нагрузки, может нарушить точность перемещения узла. [c.247]
При испытании на долговечность подшипников качения (рис. 158, а) основной узел испытательной машины состоит из вращающегося вала /, на котором установлено две пары подшипников. Одна пара смонтирована в узле радиальной нагрузки 5, а два других подшипника помещены по концам вала в корпусе машины 1120]. Имеется специальный узел 2 для создания осевой нагрузки. Нагрузка создается гидравлически от специальной системы и может изменяться в необходимых пределах. Может регулироваться также и частота вращения вала. В стенде предусмотрены система смазки подшипников и измерения их температуры. Критерием окончания испытания является шум подшипников или повышение температуры, что происходит при усталостном разрушении поверхностных слоев тел качения и износе беговых дорожек. [c.493]
СИСТЕМА СМАЗКИ ДВИГАТЕЛЕЙ [c.189]
Эффективной мерой повышения наделшостп является хорошая система смазки правильный выбор сорта масла, рациональная система подвода смазки к трущимся поверхностям, защита труш.ихся поверхностей от абразивных частиц (пыли и грязи) путем размещения изделий в закрытых корпусах, установки эффективных уплотнений и т. п. [c.13]
Цепные передачи имеют и некоторые недостатки. Основной причиной этих недостатков является то, что цепь состоит из отдельных, жестких звеньев и располагается на звездочке не по окружности, а по многоугольнику. С этим связаны износ шарниров цени, uiyM и дополнительные динамические нагрузки, необходимость организации системы смазки. [c.243]
Применение подшипников качения позволило заменить трение скольжения трением качения. Трение качения существенно меньше зависит от смазки. Условный коэффициент трения качения мал и близок к коэффициенту жидкостного трения в подшиптиобслуживание подшипника, уменьшается возможность разрушения при кратковременных перебоях в смазке (например, в периоды пусков, [c.285]
При циркуляционной системе смазки во избежание больших гидравлических сопротивлений используют масла сравнительно невысокой вязкости, повышая их несущую способность введением антнзаднрных присадок. [c.180]
Сильно усложняет эксплуатацию нерациональная система смазки, трет бующая постоянного внимания со стороны обслуживающего персонала. Периодической точечной смазки следует безусловно избегать. Если этого сделать нельзя по конструктивным условиям, то необходимо применять самосмазывающиеся опоры или вводить систему централизованной подачи смазки ко всем смазочным точкам с одного поста. [c.41]
Смазка. Подшипники насоса работают при небольших нагрузках и сравнительно высокой частоте вращения. Стенки корпуса масляной полости хорошо охлаждаются благодаря соседству потока воды в гидравлической части. В этих условиях целесообразна система смазки разбрызгиванием с применением жидкого масла небольшой вязкости и с пологой вязкостно-температурной характеристикой. Выбираем индустриальное масло 12 с вязкостью 12 сст при 50° С (по Энглеру ВУ50 = 2). [c.94]
Количес во продуктов износа измеряют химическим или спектральным анализом смазки или с помощью радиоактивных изотопов при замкнутой системе смазки. [c.481]
В отличие от гидропривода, где рабочая жидкость одновременно выполняет н функцию смазки, трущиеся поверхности рабочих органов пневмодвигателей необходимо специально смазывать. Причем, так как в процессе расширения сжатого воздуха его температура значительно понижается, для смазки необходимо применять масла с низкой температурой застывания (не выше —5 -—10° С). Обычно для этой цели применяется масло индустриальное И-ЗОА. В некоторых случаях для понижения температуры застывания масла применяются специальные присадки. Масло обычно заливается в ванну (картер) и с помощью специальных устройств подается ко всем трущимся частям. У двигателей, не имеющих собственной системы смазки, подача масла к трущимся поверхностям осуществляется из автомасленок, включаемых перед пневмодвигателями в трубопровод, подающий сжатый воздух. [c.277]
В качестве энергопривода центробежных нагнетателей применяют ГТУ либо синхронные электродвигатели, а в качестве энергопривода поршневых ГПА — газовые поршневые ДВС. В состав ГПА любого типа также входят вспомогательные системы смазки, охлаждения, регулирования, система управления и КИП. [c.155]
Задача 9-28. Определить давление на входе в шестеренчатый насос системы смазки, подающий Q=6QAjMUH MauiHHHoro масла при температу- [c.255]
Пускорезервный насос включается автоматически при снижении давления воды в питательной магистрали, причем пуск этого агрегата возможен только при наличии давления в системе смазки и открытом вентиле реци ркуляции. Релейная аппаратура обеспечивает автоматическое управление пуском, работой и остановкой питательного насоса. На электростанциях с поперечными связями предусматривается автоматическое включение находящихся в резерве насосов (АВР) при снижении давления в питательной магистрали. [c.252]
В системе смазки устанавливаются два насоса 9МД-16Х1 (рабочий и резервный) с электродвигателями переменного тока и два насоса 7МД-17Х1 (насо ы аварийного резерва) с электродвигателями постоянного тока, подключенными к независимым источникам электроэнергии. Насосы должны работать с подпором на входном пат1рубке около 10 м сверх давления паров масла. [c.282]
Рис. 2.26. Гравитационная система смазки ГТЗА |
Для уменьшения потерь из-за утечек зазоры облопатывания выполняются весьма малыми. Так, в ТВД бд = 1ч-2 мм, 62 = = l-f-1,5 мм в ТНД бд = 2- -3 мм, дг = 1,5ч-2,2 мм. Во избежание задевания и изнашивания уплотнений в процессе эксплуатации следует строго выполнять все положения соответствующей инструкции (норядйк и время нуска, наблюдение за тепловыми расширениями, уход за системой смазки и т. п.). [c.140]
Нормы расхода масла на ГТЗА указаны в инструкции завода-строителя. Расход смазочного масла определяется следующими факторами угаром и утечками в системах смазки старением масла и необходимостью его периодической замены потерями масла. Можно привести следующие ориентировочные значения удельный расход масла 0,03—0,05 г/(кВт-ч) удельная маслоемкость систем циркуляционной смазки 1,0—1,2 кг/кВт, срок службы масла — 20 тыс. ч и более [2]. [c.346]
Система смазки двигателя
: определение, детали, типы, функции
Автомобильный двигатель нуждается в смазке, поскольку он состоит из двух или более подвижных частей. Эти детали создают трение и выделяют тепло, что вызывает чрезмерный износ пар.
Смазка играет жизненно важную роль в автомобилях, поскольку способствует повышению эффективности работы и долговечности двигателя.
Когда две движущиеся части покрываются масляной пленкой, они отделены друг от друга.То есть они не вступают в физический контакт друг с другом.
В автомобилях предусмотрены световые индикаторы, которые горят при низком давлении масла в двигателе. Хотя некоторые двигатели используют индикатор, чтобы показать качество масла в двигателе.
Электрический аналоговый и электронный цифровой датчики используются для индикации давления масла. Также имеется щуп для измерения уровня масла в масляном поддоне.
Сегодня мы рассмотрим определение, детали, функции, типы и схему системы смазки двигателя в автомобилях.
Читайте: Компоненты двигателя внутреннего сгорания
Что такое смазка двигателя?Смазка двигателя — это процесс, при котором металлические части роба разделяются потоком смазывающего вещества между ними. Смазочные материалы бывают жидкими, твердыми или газообразными, но жидкость — это наиболее распространенная форма смазки, используемая в двигателях.
Функции системы смазки двигателяНиже приведены функции смазочного масла в двигателе:
- Основная цель смазки двигателя — минимизировать износ путем надежного закрытия зазора между движущимися частями, такими как валы, подшипники и т. Д.Смазка также позволяет избежать прямого контакта движущихся частей друг с другом.
- Масло служит чистящим средством в двигателе, поскольку оно перемещает частицы грязи в масляный поддон. Более мелкие частицы отфильтровываются масляными фильтрами, а более крупные задерживаются в масляном поддоне.
- Другая цель смазки двигателя заключается в том, что она служит системой охлаждения. Смазочное масло охлаждает движущиеся части двигателя и переносит горячее масло в более холодное масло в масляном поддоне.
- Масло создает уплотнение между стенками цилиндра и поршневыми кольцами. Это также снижает выброс выхлопных газов.
- Зазор между вращающимися шейками и подшипником заполнен маслом. Масло действует как амортизирующий агент, когда подшипник внезапно испытывает большие нагрузки. Масла снижают износ подшипников.
Следующие компоненты системы смазки:
Масляный поддон / поддон:Масляный поддон — это резервуар в форме чаши, в котором хранится моторное масло.Благодаря поддону масло циркулирует внутри двигателя. Деталь расположена под картером двигателя, что позволяет легко удалить масло через нижнюю часть.
Плохие дороги часто приводят к повреждению масляного поддона. Вот почему поддон изготовлен из твердого материала и имеет защиту от камней внизу. Эта защита поддона выдерживает любые удары о неровную землю или плохую дорогу.
Масляный насос:Масляный насос — это компонент, который помогает подавать смазочное масло ко всем движущимся частям двигателя.Он расположен в нижней части картера, рядом с масляным картером. Он подает масло в масляный фильтр перед отправкой дальше.
Масляные насосы со временем могут перестать работать, что может привести к повреждению двигателя. Это может быть вызвано мелкими частицами внутри смазочного масла, которые забивают масляный насос и каналы.
Чтобы избежать этой проблемы, очень необходимо менять моторное масло и фильтр в течение определенного периода времени.
Масляный фильтр:Масляный фильтр помогает задерживать мелкие частицы, отделяя их от масла, так что чистое масло может течь к деталям двигателя.Масляный насос позволяет маслу проходить через масляный фильтр в галереи, прежде чем достигнет частей двигателя.
Прочтите Что необходимо знать о блоке цилиндров автомобиля
Нефть галереи:Функция масляных каналов в системе смазки двигателя заключается в быстрой циркуляции масла для достижения всех движущихся частей в автомобиле. Таким образом, производительность масляной галереи определяет, как быстро детали вашего двигателя получают масло.
Масляные галереи представляют собой серию соединенных между собой каналов, по которым масло передается к деталям, которые в нем нуждаются.
Эти проходы представляют собой большие и маленькие отверстия, просверленные внутри блока цилиндров. Большие отверстия соединяются с меньшими, пока они не достигнут головки блока цилиндров и верхних распределительных валов.
Масляный радиатор:Маслоохладитель — это устройство, которое работает как радиатор, охлаждая горячее масло. Охладители передают тепло от моторного масла охлаждающей жидкости двигателя с помощью своих ребер. Маслоохладители стабилизируют температуру моторного масла, контролируют его вязкость, предотвращают перегрев двигателя, минимизируют износ и сохраняют качество смазочного материала
В некоторых системах смазки двигателя масло циркулирует внутри двигателя в процессе рециркуляции.Ниже приведены детали, в которые масло подается во время технологического процесса:
- Коренные подшипники коленчатого вала
- Подшипник шатуна
- Пальцы поршневые и втулки малые
- Кольца поршневые
- Зубчатая передача
- Поршень и подшипники компрессора (в грузовых автомобилях для пневматического тормоза)
- Распределительный вал и подшипники
- Клапаны
- Стенки цилиндра
- Детали масляного насоса
- Подшипники водяного насоса
- Подшипники турбокомпрессора (при наличии)
- Подшипники вакуумного насоса (при наличии)
- Подшипники продольного топливного насоса
- Толкатели и толкатели
Ниже приведены типы систем смазки двигателя:
Система смазки туманом : тип, используемый в двухтактных двигателях, где масло и топливо смешаны.Смесь вырабатывается карбюратором.
Топливо испаряется, а масло в виде тумана попадает в цилиндр через основание кривошипа. В основании кривошипа масло смазывает шатун вместе с поршневым кольцом, поршнем и цилиндром.
Система смазки мокрого поддона : обычно располагается рядом с коленчатым валом или рядом с ним. это нижняя часть двигателя, в которой есть единственный масляный насос. Этот насос перемещает масло по масляным каналам. Конструкция проще и недорого.
Система смазки с сухим картером : система с сухим картером имеет масляный резервуар, расположенный не в нижней части двигателя. Он использует два масляных насоса для поддержания циркуляции масла в двигателе. Система сложнее и дороже в проектировании. Однако конструкция сковороды более гибкая, поскольку она расположена в необычном месте. Часто встречается в высокопроизводительных двигателях.
Читайте: что такое автомобильное шасси и его значение?
Смазочная система в двухтактных и четырехтактных двигателяхРабота двухтактных и четырехтактных двигателей существенно отличается, как и их система смазки.Эти двигатели внутреннего сгорания вырабатывают механическую энергию из химической энергии, содержащейся в углеводородном топливе. Работа этих компонентов двигателя требует смазки для минимизации износа и повышения эффективности двигателя.
Основное различие между двигателями состоит в том, что двухтактные двигатели имеют рабочий ход или расширение в каждом цилиндре во время каждого оборота коленчатого вала. Процесс выпуска и впуска происходит одновременно, поскольку поршень движется через его нижнюю часть.В то время как
Четырехтактному двигателю требуется два полных оборота коленчатого вала для выполнения рабочего хода. дымовые газы сначала вытесняются поршнем во время движения вверх. Свежий заряд поступает в цилиндр во время следующего хода вниз.
Смазка четырехтактного двигателяПри смазке четырехтактных двигателей масло хранится в масляном картере или поддоне. Масло циркулирует в двигателе через систему смазки разбрызгиванием или систему смазочного насоса под давлением, что является наиболее предпочтительным выбором производителей.Хотя эти два элемента могут быть объединены в движке.
Смазка разбрызгиванием происходит, когда коленчатый вал частично погружен в масляный поддон. Импульс вращающегося коленчатого вала разбрызгивает масло на другие компоненты двигателя, такие как кулачки, стенки цилиндров, штифт и т. Д.
Смазка под давлением достигается с помощью масляного насоса для проталкивания пленки смазки между движущимися частями, такими как главные подшипники, подшипники штока и подшипники кулачка. Он также перекачивает масло в направляющие клапана двигателя и коромысла.
Прочтите Что нужно знать о системе механической трансмиссии
Смазка двухтактного двигателяОбычно двухтактные двигатели изнашиваются быстрее, поскольку в них нет источника смазки. зато есть качественное масло, значительно снижающее износ двигателя.
Двухтактные двигатели получают масло под коленчатым валом с помощью системы смазки с полным отсутствием смазки. Эта система смазки сочетает в себе масло и топливо, обеспечивая обе энергии для смазки двигателя.
Эти два агента объединяются во впускном тракте цилиндра и смазывают такие компоненты, как коленчатый вал, шатун и стенки цилиндра.
Двухтактный двигатель с впрыском масла: масло впрыскивается непосредственно в двигатель, где оно смешивается с топливом. В двухтактных двигателях с предварительным смешиванием масло-топливо смешивается перед заливкой в топливный бак.
Посмотрите видео, чтобы лучше понять работу системы смазки двигателя:
На этом статья «Система смазки двигателя».Я надеюсь, что знания достигнуты, если да, любезно комментируйте, делитесь и рекомендуйте этот сайт другим студентам технических специальностей. Спасибо!
Понимание основ автоматических систем смазки
Насос
Насос обеспечивает поток масла или консистентной смазки под давлением для приведения в действие дозирующего устройства (ей). Различные насосы предлагают различные скорости потока и диапазоны давления, а также совместимость с различными источниками питания, поэтому выбор насоса будет основываться на потребностях системы и доступных источниках питания.Насосы, используемые с форсунками, также должны иметь выпускной клапан, чтобы форсунки могли перезагружаться. Некоторые насосы также являются измерителями, например поршневые насосы, используемые в коробчатом лубрикаторе, но в большинстве случаев насос представляет собой отдельный блок.
Контроллер
Контроллер запускает график или программу для регулярной подачи смазки. Некоторые насосы имеют встроенный контроллер, но во многих системах используется контроллер, отдельный от насоса. Поскольку контроллеры являются программируемыми, они очень универсальны, и поэтому несколько контроллеров могут охватывать широкий спектр приложений.Некоторые вещи, которые следует учитывать, — это доступное напряжение и датчики, используемые в приложении. Контроллер должен иметь входы для датчиков, которые будут к нему подключены.
Трубы и фитинги
При выборе компонентов системы необходимо использовать правильную трубку, поскольку она должна быть достаточно прочной, чтобы выдерживать давление, возникающее в системе, и должна быть достаточного диаметра, чтобы смазка или масло могли проходить через нее, не создавая избыточного давления.Если трубка слишком слабая, она может лопнуть и вызвать беспорядок; или, что еще хуже, это может кого-то поранить. Если трубка слишком узкая, система может вообще не работать, потому что давление, необходимое для перемещения жидкости по трубке, может быть слишком высоким. Поэтому важно понимать потребности приложения при выборе трубки или шлангов для системы.
Дополнительные детали
Для каждой системы доступен широкий спектр дополнительных компонентов.Вот лишь несколько примеров:
- Датчики для определения цикла или давления
- Фильтры масляно-жировые и воздушные
- Датчик хода для счетчика машин
- Клапаны обратные
На первый взгляд система смазки может показаться сложной, но если разбить ее на основные компоненты, на самом деле она довольно проста. Понимание этих компонентов облегчит проектирование и заказ деталей для системы, а также устранение неполадок и ремонт существующей системы.
Компания Graco и наша сеть авторизованных дистрибьюторов могут помочь вам разработать и выбрать систему, подходящую для вашего применения.
6 различных типов систем смазки в автомобиле
Из этой статьи вы узнаете , что такое система смазки ? и Типы систем смазки с PDF загрузки.
Системы смазки и их типы
Смазка в основном требуется при техническом обслуживании автомобилей.Подача смазочного масла между движущимися частями называется просто смазкой. Смазка всех движущихся частей (кроме нейлоновых, компонентов с резиновыми втулками или предварительно смазанных компонентов) необходима для уменьшения трения, износа и предотвращения заедания.
Смазка должна выполняться должным образом, и следует использовать правильный тип смазки. Неправильная смазка двигателя вызовет серьезные проблемы, такие как царапины на цилиндрах, грязные свечи зажигания, изношенные или прогоревшие подшипники, пропуски зажигания в цилиндрах, заедание поршневых колец, отложения и шлам в двигателе, а также чрезмерный расход топлива.
Типы систем смазки
Ниже приведены 6 основных типов систем смазки :
- Система Petroil
- Система разбрызгивания
- Система давления
- Система полунапор
- Система с сухим картером
- Система с мокрым картером
1. Нефтяная система
В этих типах смазочной системы она обычно используется в двухтактных бензиновых двигателях, таких как скутеры и мотоциклы. Это простейшая форма смазочной системы.Для смазки он не имеет отдельной детали, как масляный насос.
Но смазочное масло добавляется к самому бензину при заправке бензобака транспортного средства в заданном соотношении. Когда топливо попадает в картерную камеру во время работы двигателя, частицы масла попадают на опорные поверхности и смазывают их. Таким же образом легко смазываются поршневые кольца, стенки цилиндров, поршневые пальцы и т. Д.
Если двигатель не используется в течение значительного времени, смазочное масло отделяется от бензина и начинает закупоривать каналы в карбюраторе, что приводит к проблемам с запуском двигателя.Таковы основные недостатки этой системы.
2. Система разбрызгивания
В этих смазочных системах типов смазочное масло накапливается в масляном поддоне или поддоне. В нижней части шатуна делается совок или рукоять. Когда двигатель работает, рукоять погружается в масло один раз за каждый оборот коленчатого вала, что приводит к разбрызгиванию масла на стенки цилиндра.
Это действие влияет на стенки двигателя, поршневые кольца, подшипники коленчатого вала и большие концевые подшипники.Система разбрызгивания в основном работает в сочетании с системой давления в двигателе, причем некоторые детали смазываются системой разбрызгивания, а другие — системой давления.
Читайте также: Двигатель: Типы двигателей в автомобиле с PDF
3. Система давления
В этих системах смазки детали двигателя смазываются под давлением. Смазочное масло хранится в отдельном резервуаре или поддоне, из которого масляный насос принимает масло через сетчатый фильтр и передает его через фильтр в центральный масляный канал под давлением 2-4 кг / см 2 .
Масло из главной галереи поступает в коренные подшипники, после смазки коренного подшипника часть его возвращается в поддон, часть разбрызгивается для смазки стенок цилиндра, а остальная часть идет из отверстия в шатунную шейку.
От шатунной шейки он проходит через отверстие в перемычке шатуна к поршневому пальцу, где смазывает поршневые кольца. Для смазки распределительных шестерен и распределительного вала масло проходит по отдельной масляной магистрали от масляного канала.
Лента клапана смазывается путем прикрепления основного масляного канала к направляющим поверхностям толкателя через просверленные отверстия.Манометр на панели приборов показывает давление масла в системе. Масляные фильтры и сетчатые фильтры в системе очищают масло от пыли, металлических частиц и других опасных частиц.
4. Полунапорная система
Это комбинация системы разбрызгивания и системы давления в системе смазки. Некоторые детали смазываются системой разбрызгивания, а некоторые — системой давления. Почти все четырехтактные двигатели смазываются маслом или смазкой с помощью этой полунапорной системы.
Основная подача масла в этой системе находится в основании картерной камеры. Фильтр извлекается из нижней части поддона через масло и подается через шестеренчатый насос под давлением 1 бар.
Концы подшипников большего размера смазываются распылителем. Следовательно, масло также смазывает или смазывает подшипники коленчатого вала, кулачки, стенки цилиндров и зубчатые колеса.
Подача масла измеряется с помощью манометров. Эта система менее затратна в установке.Это позволяет применять более высокие нагрузки на подшипники и частоту вращения двигателя, чем система разбрызгивания.
Читайте также: Список деталей автомобильного двигателя: его функции
5. Система сухого поддона
Система, в которой смазывающее масло собирается в масляном поддоне, известна как система мокрого поддона как система давления. Но система, в которой смазочное масло не находится в масляном картере, известна как система с сухим насосом.
В этой системе лопатки перемещают масло от впускной до выпускной стороны.Поскольку барабан устанавливается эксцентрично, объем между барабаном и отливкой непрерывно уменьшается, а давление масла на выходе увеличивается.
6. Система мокрого поддона
В этой системе масло подается к различным частям двигателя с помощью сетчатого фильтра поддона. В этой системе с мокрым картером давление масла составляет от 4 до 5 кг / см 2 . После смазки масло возвращается в масляный картер. В этом случае масло присутствует в поддоне. Поэтому ее называют системой смазки с мокрым картером.
Преимущество системы с мокрым картером заключается в ее простоте. Масло находится недалеко от того места, где оно будет применяться, в нем не так много деталей, которые нужно ремонтировать, и его относительно безопасно встраивать в автомобиль.
Вот и все, спасибо за чтение. Если вы найдете эту статью полезной, поделитесь ею со своими друзьями. Любые вопросы по «Типам систем смазки» задавайте в комментариях.
Читать дальше:
Внешние ссылки и справочные материалы:
14 CFR § 33.71 — Система смазки.| CFR | Закон США
§ 33.71 Система смазки.
(а) Общие. Каждая система смазки должна правильно функционировать в зависимости от положения и атмосферных условий полета, в которых предполагается, что самолет будет эксплуатироваться.
(b) Масляный сетчатый фильтр или фильтр. Должен быть масляный сетчатый фильтр или фильтр, через который проходит все моторное масло. Кроме того:
(1) Каждый сетчатый фильтр или фильтр, требуемый этим параграфом, который имеет байпас, должен быть сконструирован и установлен таким образом, чтобы масло текло с нормальной скоростью через остальную часть системы при полностью заблокированном сетчатом фильтре или фильтрующем элементе.
(2) Необходимо указать тип и степень фильтрации, необходимые для защиты масляной системы двигателя от инородных частиц в масле. Заявитель должен продемонстрировать, что посторонние частицы, проходящие через указанные средства фильтрации, не нарушают работу масляной системы двигателя.
(3) Каждый сетчатый фильтр или фильтр, требуемый данным параграфом, должен иметь пропускную способность (с учетом эксплуатационных ограничений, установленных для двигателя), чтобы гарантировать, что функционирование масляной системы двигателя не ухудшается из-за загрязнения маслом до некоторой степени (в отношении размера частиц и плотность), превышающую значение, установленное для двигателя в параграфе (b) (2) этого раздела.
(4) Для каждого сетчатого фильтра или фильтра, требуемого настоящим параграфом, за исключением сетчатого фильтра или фильтра на выходе из масляного бака, должны быть средства индикации загрязнения до того, как оно достигнет емкости, установленной в соответствии с параграфом (b) (3) настоящего стандарта. раздел.
(5) Любой байпас фильтра должен быть спроектирован и сконструирован таким образом, чтобы выброс собранных загрязняющих веществ был сведен к минимуму за счет соответствующего расположения байпаса, чтобы гарантировать, что собранные загрязнители не попадут в тракт байпасного потока.
(6) Каждый сетчатый фильтр или фильтр, требуемый в соответствии с настоящим параграфом, который не имеет байпаса, за исключением сетчатого фильтра или фильтра на выходе из масляного бака или для продувочного насоса, должен иметь устройства для подключения к средствам предупреждения, чтобы предупредить пилота о возникновении загрязнение экрана до того, как он достигнет емкости, установленной в соответствии с параграфом (b) (3) настоящего раздела.
(7) Каждый сетчатый фильтр или фильтр, требуемый этим параграфом, должен быть доступен для слива и очистки.
(c) Нефтяные резервуары.
(1) Каждый масляный бак должен иметь пространство для расширения не менее 10 процентов емкости бака.
(2) Должна быть исключена возможность непреднамеренного заполнения расширительного пространства масляного бака.
(3) Каждое утопленное заправочное соединение масляного бака, которое может удерживать любое заметное количество масла, должно иметь приспособление для установки слива.
(4) Каждая крышка масляного бака должна обеспечивать герметичное уплотнение. Для заявителя, желающего получить право на установку двигателя на самолет, утвержденный для ETOPS, масляный бак должен быть спроектирован таким образом, чтобы предотвратить опасную потерю масла из-за неправильно установленной крышки масляного бака.
(5) Каждая заправочная горловина масляного бака должна быть помечена словом «масло».
(6) Каждый масляный бак должен вентилироваться через верхнюю часть пространства расширения, при этом вентиляционное отверстие должно быть устроено таким образом, чтобы конденсированный водяной пар, который может замерзнуть и заблокировать трубопровод, не мог скапливаться в любой точке.
(7) Должны быть предусмотрены средства для предотвращения попадания в масляный резервуар или в любое выходное отверстие масляного резервуара любых предметов, которые могут препятствовать потоку масла через систему.
(8) На выходе каждого масляного бака должен быть запорный клапан, за исключением случаев, когда внешняя часть масляной системы (включая опоры масляного бака) является пожаробезопасной.
(9) Каждый негерметичный масляный бак не должен протекать при максимальной рабочей температуре и внутреннем давлении 5 p.s.i., и каждый масляный бак под давлением должен соответствовать требованиям § 33.64.
(10) Утечка или пролитое масло не должно скапливаться между баком и остальной частью двигателя.
(11) Каждый масляный бак должен иметь индикатор количества масла или приспособления для него.
(12) Если флюгирование воздушного винта зависит от моторного масла —
(i) Должны быть средства для улавливания некоторого количества масла в баке, если запасы масла истощаются из-за отказа какой-либо части системы смазки, кроме самого бака;
(ii) Количество захваченного масла должно быть достаточным для выполнения операции флюгирования и должно быть доступно только насосу флюгирования; а также
(iii) Необходимо принять меры для предотвращения воздействия шлама или других посторонних веществ на безопасную работу системы флюгирования гребного винта.
(d) Слив масла. Должен быть предусмотрен слив (или стоки), чтобы обеспечить безопасный слив из масляной системы. Каждый слив должен —
(1) Быть доступным; а также
(2) Иметь ручные или автоматические средства принудительной блокировки в закрытом положении.
(д) Масляные радиаторы. Каждый масляный радиатор должен безотказно выдерживать любую вибрацию, инерцию и нагрузку давления масла, которым он подвергается во время испытаний блока.
[Amdt. 33-6, 39 FR 35466, 1 октября 1974 г., с поправками, внесенными Amdt.33-10, 49 FR 6852, 23 февраля 1984 г .; Amdt. 33-21, 72 FR 1877, 16 января 2007 г .; Amdt. 33-27, 73 FR 55437, 25 сентября 2008 г .; Amdt. 33-27, 73 FR 57235, 2 октября 2008 г.]Общие сведения о лубрикаторах и смазочных системах
Смазочные устройства и системы смазки распределяют масла и смазку по механическим устройствам, таким как подшипники, конвейерные цепи, железнодорожные рельсы, пневматические инструменты или сальники, с целью минимизации трения между движущимися частями. Смазочные материалы уменьшают трение качения и скольжения, сводят к минимуму износ и коррозию, повышают эффективность, изолируют загрязнения и имеют решающее значение для работы многих движущихся механических компонентов.Лубрикаторы могут быть самыми разными: от простейшего ручного шприца для смазки до сложных автоматизированных центральных систем, которые периодически распределяют смазочные материалы во множество точек смазки на производственном предприятии, на корабле или в аналогичных ситуациях, когда механическое оборудование работает и нуждается в преимущества смазочных материалов.
Что касается систем, то данная статья в первую очередь обращается именно к этим последним, внешним системам. Хотя в двигателе внутреннего сгорания определенно используется система смазки, она не будет покупаться скрытно, но по большей части является неотъемлемой частью самого двигателя.Некоторые очень большие низкооборотные дизели используют внешние лубрикаторы для впрыска масла на стенки цилиндров, но это особые области применения.
В строительной технике используются системы смазки для обеспечения эффективной работы соединений и компонентов.
Изображение предоставлено: Lestertair / Shutterstock.com
Основная идея лубрикаторов и систем смазки состоит в том, чтобы взять на себя ручную критическую задачу — снизить трение за счет смазки или смазки — и устранить некоторые неудобные, иногда опасные и, безусловно, повторяющиеся аспекты деятельности, используя автоматизацию для меньшего или в большей степени.Если не брать в расчет шприцы для смазки, в этой статье будут рассмотрены системы смазки, охарактеризованные этими тремя классификациями:
- Лубрикаторы одноточечные
- Многоточечные системы смазки
- Централизованные, автоматизированные системы
Также будут обсуждаться некоторые специальные области применения систем смазки. Дополнительную информацию о типах масел и пластичных смазок, обычно используемых в смазочных материалах, см. В нашем соответствующем руководстве по смазочным материалам.
Особые типы оборудования
Одноточечные лубрикаторы
Одноточечные лубрикаторы предназначены для одной пресс-масленки, например, на опорных блоках или подшипниках двигателя. Они могут быть с пружинным приводом, с электрохимическим давлением или с двигателями с батарейным питанием. Одноточечные лубрикаторы также используются для дозирования масла к механическим компонентам и иногда называются капельными лубрикаторами или масляными колпачками. Они оснащены щетками и представляют собой эффективный метод смазки роликовой цепи.
Вязкость смазки зависит от температуры и влияет на способность лубрикатора распределять смазку по компонентам. Такое поведение может повлиять на выбор лубрикаторов для использования вне помещений. Моторизованные или поршневые лубрикаторы не работают против какого-либо противодавления в компоненте и могут быть рассчитаны на периодическую дозировку известного объема масла или смазки. Электрохимические лубрикаторы вырабатывают сжатый газ, который вытесняет смазку из устройства с постоянной скоростью.Скорость можно отрегулировать в соответствии с использованием компонента, но на скорость будут влиять колебания вязкости.
Электрохимические лубрикаторыобычно приобретаются как одноразовые устройства, которые можно настроить для дозирования смазки в течение определенного периода времени — например, одного месяца, трех месяцев или одного года. После установки устройства в точке смазки установщик активирует его, после чего начинается электрохимический процесс производства газа, создающий давление в устройстве. Поскольку смешивание различных смазок может ухудшить характеристики смазочного материала, производители этих устройств обычно продают их предварительно заполненными различными доступными составами.
Моторизованные лубрикаторы, поскольку они более сложные и, следовательно, более дорогие, обычно продаются как повторно заправляемые единицы. Обычно аккумулятор меняют во время заправки.
Эти узлы очень популярны для смазки подшипников и подшипниковых узлов конвейеров, двигателей, насосов и воздуходувок. Их можно установить непосредственно на подшипник или по трубопроводу можно подвести к точке смазки поблизости, чтобы обойти ограждения или барьеры или упростить замену / заправку в труднодоступных или опасных местах.
Узлы с пружинным приводом — самые простые из одноточечных лубрикаторов. Для работы им не нужны батареи или электричество. Пружины можно выбрать из нескольких диапазонов, чтобы они совпадали с выбором смазочных материалов и рабочими температурами. Многие из них многоразовые; некоторые предназначены для одноразового использования.
Масляные лубрикаторыбывают нескольких видов: самотечные или капельные, фитильные и с постоянным уровнем. Масленки с гравитационным потоком полагаются на регулируемые вручную игольчатые клапаны для подачи прерывистого потока масла к механическим компонентам.Подсчет капель в минуту осуществляется путем наблюдения за ними через смотровое стекло, которое является неотъемлемой частью масленки. Добавление фитиля или щетки к масленке с гравитационным потоком позволяет маслу лучше достигать компонента, как, например, в случае кулачкового толкателя или роликовой цепи.
Даже в старых капельных лубрикаторах используются прозрачные резервуары и стаканы.Изображение предоставлено: MRo / Shutterstock.com
Лубрикаторы постоянного уровня используются в основном с закрытыми подшипниками и зубчатыми передачами, для обеспечения надлежащей смазки которых требуется определенный уровень масла в корпусе.Внешний лубрикатор определяет, когда уровень в корпусе падает, и добавляет необходимое количество подпитки. Эти системы обычно не имеют электропитания и включают в себя прозрачные масляные резервуары, которые необходимо время от времени пополнять.
Многоточечные лубрикаторы
Самым простым из многоточечных лубрикаторов является групповая компоновка Церка, очень распространенная на мобильном оборудовании, которая позволяет механику распределить порцию смазки на все основные компоненты с одной станции. Это не совсем лубрикатор как таковой, каждый смазочный ниппель жестко прикреплен к своему конкретному компоненту, что предотвращает частое ползание со стороны механика или оператора для проведения этого базового обслуживания.На следующем этапе все точки смазки связываются с одним фитингом Церка, и оператор смазывает все сразу с помощью ручного пистолета. Такие приспособления популярны на строительной технике и аналогичных машинах, где регулярная и частая смазка является постоянной рутиной.
Подвод нескольких точек смазки к центральному месту несколько упрощает смазочные работы.Изображение предоставлено: Стивен Дилкс / Shutterstock.com
Автоматические многоточечные лубрикаторы сочетают в себе идею одноточечного лубрикатора и нескольких мест смазки для достижения автоматического дозирования смазки с помощью единственного электрического подключения.Эти устройства часто имеют программируемые функции, ограниченный набор сигналов тревоги, а также резервуары значительной емкости.
Централизованные, автоматизированные системы
Автоматизированные системы смазки можно охарактеризовать как одно-, двух- и многоточечные. Система обычно включает в себя насос, устройства измерения и контроля, контроллер, а также необходимые трубки и фитинги для каждой точки смазки.
Решение об установке одно- или двухмагистральной системы основывается на количестве точек, требующих смазки.Однолинейные системы обычно могут обрабатывать почти тысячу точек, в то время как двухлинейные системы могут обрабатывать почти вдвое больше. Оба обычно способны достигать расстояния до 100 ярдов или около того от насоса / резервуара. Однолинейные системы часто подходят для автономных машин, например, в упаковочной, полиграфической и подобных отраслях. Более крупные двухлинейные системы подходят для тяжелых, грязных перерабатывающих производств, таких как сталелитейные или цементные заводы.
Системы описываются как параллельные или прогрессивные.Параллельные системы будут распределять смазку в каждую точку независимо от состояния любой другой точки. То есть, если одна точка смазки заблокирована, все остальные точки в системе все равно будут смазаны. Прогрессивные системы полагаются на то, что каждая точка в системе успешно смазывается до того, как будут обработаны последующие точки. У каждого подхода есть свои преимущества. В параллельных системах вероятность нехватки нескольких точек сводится к минимуму. В прогрессивных системах можно потерять несколько очков из-за одной блокировки, но это маловероятно, поскольку любая неисправность в системе будет быстро обнаружена.
Ни один из методов не требует подачи электроэнергии на точки смазки. Эти системы приводятся в действие гидравлически, дозируемое количество определяется отверстиями, которые можно приобрести в различных фиксированных размерах или в виде регулируемых единиц. Электроэнергия требуется для насоса и для одного или двух датчиков давления, которые расположены непосредственно перед последними дозирующими устройствами. Электромагнитные клапаны могут быть добавлены для создания многозонных систем; Эти клапаны, конечно, требуют энергии для работы. Смазка не подается постоянно, а впрыскивается во время части системного цикла.Масло обычно подается непрерывно в циркуляционных системах смазки маслом. Автоматизированными системами смазки можно управлять с помощью базовых таймеров задержки или с помощью более сложных программируемых логических контроллеров или ПЛК, которые могут определять, когда система работает, количество циклов и т. Д. И которые предлагают уровни сигналов тревоги для состояния низкого резервуара, заблокированных выпускных отверстий и т. Д. и т. д., а также обеспечивают мониторинг расхода и температуры. Насосы обычно конфигурируются для работы с маслом или консистентной смазкой, но они могут быть ручными, гидравлическими, пневматическими или электрическими.Форсунки, используемые в однолинейных системах, зависят от давления в системе, чтобы преодолеть сопротивление пружины в форсунках. Они индивидуально регулируются для дозирования определенных объемов смазки и рассчитываются на основе максимального количества, впрыскиваемого за один выстрел. В одной системе смазки можно комбинировать форсунки разной мощности. Обычно штифт или шток обеспечивают визуальную индикацию того, что каждый инжектор работает. Разделительные клапаны используются для разделения цикла смазки на полупериоды с помощью перемещающихся поршней, которые позволяют смазывать большее количество точек с помощью данной системы.Такие клапаны обычно объединяются в группы и могут устанавливаться с закупоренными портами, чтобы обеспечить дальнейшее расширение системы смазки.
Приложения
Строительное оборудование использует автоматические и ручные системы для смазывания многих соединений кранов, экскаваторов и аналогичного крупного механического оборудования. В оборудовании, используемом для пищевой промышленности и упаковки, используются системы автоматической смазки для распределения смазки во многих точках, которые часто подвергаются мойке. Конвейерные системы и подвесные тележки полагаются на автоматическую смазку цепных дорожек конвейера.На железных дорогах применяется автоматическая смазка на крутых поворотах для снижения износа гребней колес и шума.
В станкахиспользуются системы смазки для уменьшения трения на путях, а также для подачи смазочно-охлаждающей жидкости в сам процесс обработки. Так называемые системы смазки с минимальным количеством смазки стали популярными благодаря своей способности уменьшать количество смазки, используемой при удалении металла. Редукторы часто оснащены распылительными лубрикаторами, которые непрерывно направляют масло в зубчатое зацепление.Воздушное оборудование обычно требует, чтобы FRL или лубрикаторы-регуляторы были установлены перед точками подачи.
Типичный автоматический многоточечный лубрикатор для конвейерной цепи.Изображение предоставлено: DropsA USA
Примечания к выбору
Как и любая автоматизированная система, лубрикаторы и системы смазки усложняют то, что можно было бы считать рутинной, но необходимой ручной задачей. Одним из преимуществ смазки оборудования вручную является то, что механик или оператор вынуждены обходить его и визуально и на слух проверять работоспособность и состояние машины.Регулярные визуальные осмотры могут выявить проблемы до того, как они перерастут в более серьезные поломки, которые могут привести к затратам, связанным с простоем оборудования. Этот риск не исчезает с добавлением автоматизированной системы, и ее добавление добавляет еще один уровень сложности к проблеме обеспечения правильной работы системы. Производители лубрикаторов и систем смазки добились многих успехов, чтобы обеспечить правильную работу своего оборудования и сообщить пользователям о неисправностях.
Автоматизация некоторых или всех аспектов смазки дает множество преимуществ. Правильно откалиброванные автоматические системы смазки могут подавать нужное количество смазки или масла — таким образом, избегая неудач, связанных с добавлением слишком большого или слишком малого количества смазки — и делают это по регулярному графику. Такое регулярное и последовательное введение смазки не только способствует здоровью машины, но также может снизить расходы на смазочные материалы. Смазку можно добавлять во время работы оборудования, что считается более эффективным, чем нанесение ее на статический компонент.Вращающееся оборудование с ручной смазкой также может подвергать обслуживающий персонал воздействию опасных условий, например, механических муфт. Автоматические системы также снижают риск загрязнения смазочного материала грязью и мусором.
Сколько смазки?
Чтобы получить максимальную выгоду от лубрикаторов и автоматизированных систем смазки, необходимо дозировать масло или консистентную смазку в соответствии с требованиями к смазке рассматриваемого элемента. Слишком малое количество явно отрицательно сказывается на сроке службы компонентов; слишком много может быть вредным.Производители подшипников и других смазываемых компонентов часто могут быть источником информации о рекомендуемых интервалах смазки, но факторы окружающей среды также играют роль в определении того, подходят ли эти рекомендации. В цитируемой ниже статье читатели знакомятся с двумя формулами определения соответствующих объемов смазки и применяют их к выбору компонентов, которые обычно смазываются консистентной смазкой, включая подшипники качения и подшипники скольжения. Согласно статье, смазываемые системы обычно представляют собой системы с непрерывными потерями, и, поскольку рабочие стекла неработоспособны, в этих ситуациях сложно определить, достаточно ли смазываются компоненты.
Ресурсы
Общие
Следующие организации могут предоставить дополнительную полезную информацию по многим аспектам смазки.
Общество трибологов и инженеров по смазкам
https://www.stle.org
Американская ассоциация производителей подшипников
https://www.americanbearings.org
Американская ассоциация производителей шестерен
https://www.agma.org
Отдел трибологии ASME
https: // community.asme.org
График смазки
https://www.stle.org
S мм арыйЭто руководство дает общее представление о лубрикаторах и системах смазки, а также об их выборе, использовании и применении. Для получения дополнительной информации о сопутствующих продуктах обратитесь к другим нашим руководствам или посетите платформу Thomas Supplier Discovery Platform, чтобы найти потенциальные источники поставок или просмотреть подробную информацию о конкретных продуктах.
Прочие товары по смазочным материалам
Другие товары из категории Машины, инструменты и расходные материалы
Все, что вам нужно знать об автоматических системах смазки
Размещено: 8 мая 2015 г.Автор: Майк Декерт, вице-президент и Габриэль Лопес, специалист по маркетингу, FLO Components Ltd.
В исследовании, проведенном крупным производителем компонентов, ненадлежащая смазка является причиной 53% всех отказов подшипников, основной причиной простоя оборудования и значительных ненужных затрат на техническое обслуживание, включая замену подшипников, трудозатраты на ремонт или замену подшипников, внеплановые простои и последствия о выполнении обязательств по доставке клиентов. В первую очередь, эти отказы вызваны загрязнением втулок пылью, грязью и влагой или недостаточным количеством смазки, нанесенной на подшипники.
Однако отсутствие смазки — не единственная проблема — неэффективные методы ручного смазывания часто могут приводить к чрезмерному смазыванию ключевых точек поворота, что влечет за собой собственные косвенные, но очень реальные затраты, включая потраченное впустую смазочное масло, экологические проблемы, безопасность или проблемы с хозяйством. и более высокие затраты на рабочую силу.
Автоматическая система смазки (ALS) помогает устранить эти незапланированные и ненужные расходы. Независимо от того, знаете ли вы его как автоматическую систему смазки, автосмазку или централизованную систему смазки или смазки маслом, ALS автоматически смазывает несколько точек на машине с помощью централизованного блока насоса / управления, который установлен в легкодоступном месте.Система подает небольшие отмеренные количества смазки через частые промежутки времени во время работы вашей машины, постоянно поддерживая равномерную подачу смазки в подшипники и стабильное смазочное уплотнение для предотвращения попадания грязи и загрязнений в подшипники. Это можно сравнить с праздником и голодом, которые часто ассоциируются с ручной смазкой, когда смазка выполняется «когда есть время».
В разговоре с людьми, которые в настоящее время не используют ALS, мы часто говорим вроде «Даже если я использую систему автоматической смазки, мне все равно придется проводить регулярный осмотр машины в системе».Это абсолютно правильно. ALS не заменит вам регулярного технического осмотра машины. Вам все равно нужно проверить, нет ли ослабленных или поврежденных линий, и убедиться, что все работает без сбоев. Что такое ALS, он берет у вас из рук шприц для смазки или масленку и заменяет его гаечным ключом. Затем вы можете использовать линии смазки в качестве ориентира и иметь возможность сосредоточиться на внесении любых необходимых регулировок или ремонтов при проведении регулярной проверки.
Итак, вы можете спросить себя: «В чем смысл использования ALS?» Есть 8 причин, по которым вы хотели бы использовать автоматическую систему смазки:
1) Безопасность
Система ALS помогает уменьшить или исключить возможность лазания над и под оборудованием или в труднодоступных местах, и на современном рабочем месте безопасность персонала всегда является ключевым фактором.
2) Эффективная смазка
Система ALS наносит смазку во время работы машины, поэтому вам не нужно останавливать свои дела или выделять время для смазки — иными словами, сокращается время простоя. Кроме того, поскольку подшипник вращается, когда он получает смазку, вы получаете гораздо лучшее покрытие подшипников консистентной смазкой или маслом.
3) Лучшая смазка
Нанесение консистентной смазки или масла часто бывает наиболее эффективным, когда они распределяются небольшими дозированными количествами в короткие, частые промежутки времени.К сожалению, сжатые сроки и нехватка рабочей силы или, в некоторых случаях, расположение машины часто делают метод смазки невозможным. Машину смазывают, когда она доступна, и когда у нас есть время и кто-то, кто может это сделать. Ясно, что такой подход не оптимален для точки, требующей смазки. БАС решает эту проблему.
4) Лучшая уборка
Сколько смазки или масла слишком много? Если вы приверженец старой школы, вы продолжаете накачивать его, пока не увидите, как он сочится из подшипника.Это то, что мы в FLO Components называем «избыточной смазкой». Как указывалось ранее, частые и небольшие отмерения количества воды обеспечат наилучшую защиту подшипников. В дополнение к отсутствию избыточной / недостаточной смазки это также означает, что вы получите меньше разливов и утечек. Конечным результатом является уменьшение потерь жира или масла и меньше беспорядка на вашем оборудовании и на полу. Помимо внешнего вида, еще важнее безопасность (опасность поскользнуться) и экология.
5) Меньшее время простоя, снижение затрат на техническое обслуживание и сокращение замены подшипников
Из-за нехватки времени и рабочей силы зачастую практически невозможно удовлетворить потребности машин в смазке.«Предотвращение технического обслуживания», обеспечиваемое ALS, является абсолютно ключевым для снижения затрат на техническое обслуживание и минимизации времени простоя за счет увеличения срока службы многих шарниров, подшипников, втулок и других компонентов машины. На складе также меньше запасных частей.
6) Повышение общей производительности
В результате повышения эксплуатационной готовности машины и сокращения времени простоя из-за поломок или общего технического обслуживания.
7) Увеличенный срок службы машины
Потому что опорные площадки постоянно защищены, а ваше оборудование в целом лучше обслуживается.
8) Помогает окружающей среде
С точки зрения окружающей среды, меньший преждевременный износ подшипников и других компонентов означает меньший объем захоронения отходов. Кроме того, поскольку вы не слишком много смазываете (см. «Лучшее ведение хозяйства» выше), вы истощаете меньше ресурсов из окружающей среды.
СистемыALS различаются по качеству и конструкции в зависимости от производителя, но обычно состоят из пяти основных компонентов: контроллера или таймера для запуска системы; насос и резервуар для хранения смазки; подводящий трубопровод, соединяющий насос с дозирующими клапанами; дозирующие клапаны или форсунки для измерения и распределения смазки; и подающие трубопроводы и фитинги для подачи смазки к точкам нанесения.
Сегодня в отрасли есть несколько производителей, предлагающих автоматические системы смазки, поэтому при выборе системы важно убедиться, что вы сравниваете яблоки с яблоками и задаете правильные вопросы. Первое, что нужно знать, это то, что существуют разные принципы работы, в соответствии с которыми разработаны ALS. Два наиболее распространенных типа ALS, используемых на мобильном оборудовании, — это последовательный прогрессивный и параллельный.
В однолинейной прогрессивной системе насос подает смазочный материал к точкам смазки через прогрессивные дозирующие клапаны, размер которых индивидуален для каждой точки приложения.Смазка проходит через первичный клапан, который перенаправляется на несколько вторичных клапанов, и, наконец, через питающие линии к конечным точкам нанесения. Природа этой системы такова, что если какая-либо линия / подшипник не набирает смазку, вся система отключается, и появляется (в правильно спроектированной системе) визуальное указание оператору на наличие проблемы. Это дает оператору возможность принять меры до того, как произойдет какое-либо повреждение.
В системе типа Parellel смазочный материал течет от насоса через одну линию подачи к нескольким ответвлениям форсунок.Форсунки работают одновременно, но не зависят друг от друга. Каждый инжектор обслуживает только одну точку смазки и может быть точно отрегулирован для подачи точного количества требуемого смазочного материала или масла. Природа системы параллельного типа такова, что контролируется только давление в основной магистрали, поэтому, если какая-либо линия подачи или подшипник не принимает смазку, остальная часть системы будет продолжать нормально функционировать, но подшипник, не имеющий смазки, может быть потерян.
После того, как вы определились с типом системы, вы можете задать следующие вопросы:
1.Включает ли насосный агрегат линейный масляный фильтр высокого давления?
Фильтр предотвращает попадание в распределительные линии загрязняющих веществ, которые могут вызвать отказ системы, дорогостоящую замену компонентов и затраты на рабочую силу. Для большинства производителей систем фильтр НЕ входит в стандартную комплектацию — он должен быть указан.
2. Являются ли шланги, трубки и трубные фитинги стандартной резьбой NPT?
Некоторые производители систем используют метрические концы шлангов и трубные фитинги.Для адаптации к входным отверстиям подшипников с резьбой NPT требуются специальные адаптеры, что приводит к увеличению затрат и трудозатрат, а также к возможным задержкам во время обслуживания, если вы не подготовили подходящие заменяемые фитинги.
3. Есть ли в системе манометр?
Манометр позволяет визуально контролировать давление в системе во время регулярных профилактических осмотров. Для большинства производителей систем манометр НЕ входит в стандартную комплектацию — он должен быть указан.
4.Если это система смазки, есть ли в дозирующих клапанах ручные пресс-масленки высокого давления?
Наличие ручной пресс-масленки на каждом дозирующем клапане упрощает поиск и устранение неисправностей, обслуживание, заливку и промывку смазочных линий. Отсутствие ручной пресс-масленки означает, что линии должны быть отключены для выполнения многих из этих задач, что значительно увеличивает затраты на рабочую силу. Большинство производителей либо НЕ включают пресс-масленки, либо используют стандартные пресс-масленки, которые протекают при высоком противодавлении заблокированной линии.В качестве альтернативы, использование пресс-масленок высокого давления, специально разработанных для работы с высоким противодавлением, на каждом дозирующем клапане гарантирует, что в маловероятном случае блокировки линии единственная утечка произойдет там, где ее увидит оператор машины — на предохранительном клапане давления на насосный агрегат.
5. Как узнать, не попадает ли в подшипник смазка или масло?
В прогрессивной системе дозирующие клапаны работают последовательно друг с другом. Некоторые системы включают в себя штифт индикатора цикла (CIP) на главном клапане в сборе для обеспечения визуального подтверждения цикла работы системы каждый раз.Если какая-либо линия / подшипник не принимает консистентную смазку или масло, вся система отключается, и оператор получает визуальную индикацию (CIP) о наличии проблемы, что дает оператору возможность принять меры до того, как произойдет какое-либо повреждение.
В системе параллельного типа дозирующие клапаны работают одновременно, но независимы. Система параллельного типа включает реле давления, которое контролирует только давление в основной линии, поэтому нет индикации (связанной с давлением), работает ли каждая отдельная линия подачи.Остальная часть системы продолжит нормально функционировать, но подшипник, не имеющий смазки, скорее всего, будет утерян. Для систем некоторых производителей, если какая-либо линия подачи или подшипник не забирает консистентную смазку или масло, единственным визуальным признаком является отсутствие смазки в точке подшипника. Другие будут включать в себя индикаторные штифты на каждом инжекторе, которые перемещаются внутрь и наружу по мере подачи смазки, чтобы визуально подтверждать работу каждой отдельной линии подачи.
6. Требуется ли для системы специальная смазка?
Некоторые производители требуют, чтобы вы покупали смазку непосредственно у них, чтобы гарантировать систему.Другие не имеют ограничений по марке смазочного материала, что позволяет использовать стандартную пластичную смазку в магазине и значительно сокращает запасы и затраты.
В заключение, автоматическая система смазки является ценным инструментом для сокращения прямых и косвенных затрат, связанных с неадекватной смазкой, но вам необходимо понимать, как она работает, какие типы систем доступны и какой тип лучше всего подходит вашей компании (или компаниям). стиль работы. Самое главное, при поиске ALS задайте вопросы, изложенные в этой статье, и вы будете на пути к покупке инструмента, который поможет обслуживать ваше оборудование, снизить затраты и повысить производительность на долгие годы.
О компании FLO Components Ltd .:
Основанная в 1977 году и базирующаяся в Миссиссаге, Онтарио, FLO Components Ltd. является специалистом по системам смазки и ведущим поставщиком решений Total Lube Solutions и поставок для крупных строительных, дорожных, агрегатных, горнодобывающих компаний и производителей в Онтарио. FLO является главным дистрибьютором Lincoln Industrial более 35 лет и является крупнейшей компанией Lincoln Systems House в Канаде. В 2012 году FLO стала первым официальным системным подразделением SKF в области смазочных материалов в Канаде, способным предложить весь спектр решений LINCOLN и SKF по смазочным материалам для всех областей применения.
Компоненты системы смазки турбинного двигателя самолета
Выходной поворотный фитинг управляется утяжеленным концом, который может свободно качаться под перегородкой. Заслонки в перегородке обычно открыты; они закрываются только тогда, когда масло в нижней части бака стремится устремиться к верхней части бака во время замедления. Это улавливает масло на дне резервуара, где оно собирается шарнирным соединением. Слив отстойника расположен в нижней части бака.Система вентиляции внутри бака устроена так, что воздушное пространство вентилируется постоянно, даже если масло может попасть в верхнюю часть бака при замедлении самолета.
Все масляные баки имеют расширительное пространство. Это позволяет маслу расширяться после поглощения тепла подшипниками и шестернями и после того, как масло вспенивается в результате циркуляции в системе. Некоторые резервуары также включают лоток деаэратора для отделения воздуха от масла, возвращаемого в верхнюю часть резервуара системой продувки.Обычно эти деаэраторы представляют собой канистры, в которые масло входит по касательной. Выпускаемый воздух проходит через вентиляционную систему в верхней части резервуара.
В большинстве масляных резервуаров требуется повышение давления внутри резервуара для обеспечения положительного потока масла на вход масляного насоса. Повышение давления становится возможным благодаря пропусканию вентиляционной линии через регулируемый обратный предохранительный клапан. Обратный предохранительный клапан обычно настраивается на разгрузку около 4 фунтов на квадратный дюйм, поддерживая положительное давление на входе масляного насоса.Если температура воздуха слишком низкая, масло можно заменить на более легкое. На некоторых двигателях может быть предусмотрена установка масляного нагревателя погружного типа.
Масляный насос
Масляный насос предназначен для подачи масла под давлением к частям двигателя, требующим смазки, затем для циркуляции масла через охладители и возврата масла в масляный бак. Многие масляные насосы состоят не только из элемента подачи давления, но и из продувочных элементов, например, в системе с сухим картером.Однако есть некоторые масляные насосы, которые выполняют единственную функцию; то есть они либо подают масло, либо собирают его. Эти насосные элементы могут быть расположены отдельно друг от друга и приводиться в действие разными валами от двигателя. Количество подкачивающих элементов (двух шестерен, перекачивающих масло), напорных и продувочных, во многом зависит от типа и модели двигателя. Несколько элементов промывочного масляного насоса могут использоваться для размещения большей емкости смеси масла и воздуха. Элементы продувки имеют большую перекачивающую способность, чем элемент давления, чтобы предотвратить скопление масла в поддонах подшипников двигателя.
Рис. 2. Вид шестеренчатого масляного насоса в разрезе |
Насосы могут быть одного из нескольких типов, каждый из которых имеет определенные преимущества и ограничения. Два наиболее распространенных масляных насоса — это шестеренчатый и героторный, причем чаще всего используется шестеренчатый. Каждый из этих насосов имеет несколько возможных конфигураций.
Шестеренчатый масляный насос имеет всего два элемента: один для масла под давлением и один для продувки.[Рис. 2] Однако некоторые типы насосов могут иметь несколько элементов: один или несколько элементов для давления и два или более элементов для продувки. Зазоры между зубьями шестерни и сторонами стенки насоса и пластины имеют решающее значение для поддержания правильной производительности насоса.
Регулирующий (предохранительный) клапан на нагнетательной стороне насоса ограничивает выходное давление насоса путем перепуска масла на вход насоса, когда выходное давление превышает заданный предел. [Рис. 2] Регулирующий клапан можно отрегулировать, если необходимо, для приведения давления масла в допустимые пределы.Также показан участок среза вала, который вызывает срезание вала, если шестерни насоса заедают и не вращаются.
Героторный насос, как и шестеренчатый насос, обычно содержит один элемент для давления масла и несколько элементов для удаления масла. Каждый из элементов, давление и продувка, почти идентичен по форме; однако емкостью элементов можно управлять, варьируя размер героторных элементов. Например, нагнетательный элемент может иметь пропускную способность 3.1 галлон в минуту (галлон в минуту) по сравнению с производительностью 4,25 галлона в минуту для продувочных элементов. Следовательно, прижимной элемент меньше, поскольку все элементы приводятся в движение общим валом. Давление определяется оборотами двигателя при минимальном давлении на холостом ходу и максимальном давлении на промежуточных и максимальных оборотах двигателя.
Типичный набор героторных насосных элементов показан на Рисунке 3. Каждый комплект героторных насосов разделен стальной пластиной, что делает каждый комплект индивидуальным насосным агрегатом, состоящим из внутреннего и внешнего элементов.Маленький внутренний элемент в форме звезды имеет внешние выступы, которые подходят внутрь и соответствуют внешнему элементу, имеющему внутренние выступы. Маленький элемент устанавливается на вал насоса, фиксируется на нем и действует как привод для внешнего свободно вращающегося элемента. Внешний элемент помещается в стальную пластину с эксцентриковым отверстием. В одной модели двигателя масляный насос имеет четыре элемента: один для подачи масла и три для продувки. В некоторых других моделях насосы имеют шесть элементов: один для подачи и пять для продувки. В каждом случае масло течет, пока вращается вал двигателя.
Рисунок 3. Типичные героторные насосные элементы |
Масляные фильтры турбины
Фильтры являются важной частью системы смазки, поскольку они удаляют инородные частицы, которые могут находиться в масле. Это особенно важно для газовых турбин, поскольку достигаются очень высокие обороты двигателя; шариковые и роликовые подшипники антифрикционного типа могут быстро выйти из строя при смазке загрязненным маслом.Кроме того, обычно имеется множество просверленных или стержневых каналов, ведущих к различным точкам смазки. Поскольку эти проходы обычно довольно маленькие, они легко забиваются.
Рисунок 4. Элемент масляного фильтра турбины |
Существует несколько типов и мест расположения фильтров, используемых для фильтрации смазочного масла турбины. Фильтрующие элементы бывают разных конфигураций и размеров ячеек. Размеры ячеек измеряются в микронах, что является линейным размером, равным одной миллионной метра (очень маленькое отверстие).
Главный фильтрующий элемент масляного фильтра показан на рисунке 4. Внутренняя часть фильтрующего элемента изготовлена из различных материалов, включая бумагу и металлическую сетку. [Рис. 5] Масло обычно проходит через фильтрующий элемент снаружи в корпус фильтра. В одном типе масляного фильтра используется сменный ламинированный бумажный элемент, в других — очень мелкая металлическая сетка из нержавеющей стали толщиной около 25–35 микрон.
Рис. 5. Бумажный элемент масляного фильтра турбины |
Большинство фильтров расположены рядом с нагнетательным насосом и состоят из корпуса или корпуса фильтра, фильтрующего элемента, байпасного клапана и обратный клапан.Перепускной клапан фильтра предотвращает остановку потока масла в случае засорения фильтрующего элемента. Перепускной клапан открывается при достижении определенного давления. В этом случае фильтрующее действие теряется, что позволяет перекачивать нефильтрованное масло к подшипникам. Однако это предотвращает полное отсутствие масла в подшипниках. В байпасном режиме у многих двигателей есть механический индикатор, который выскакивает, чтобы указать, что фильтр находится в байпасном режиме. Эта индикация является визуальной, и ее можно увидеть только при непосредственном осмотре двигателя.В узел встроен антидренажный обратный клапан, чтобы предотвратить слив масла из бака в отстойники двигателя, когда двигатель не работает. Этот обратный клапан обычно закрывается пружиной с давлением от 4 до 6 фунтов на квадратный дюйм, необходимого для его открытия.
Рис. 6. Фильтр последнего шанса перед распылительной форсункой |
Обычно обсуждаемые фильтры используются в качестве основных масляных фильтров; то есть они деформируют масло на выходе из насоса перед подачей к различным точкам смазки.Помимо основных масляных фильтров, по всей системе расположены вторичные фильтры различного назначения. Например, может быть сетчатый фильтр с пальцами, который иногда используется для фильтрации забитой нефти. Эти сита, как правило, представляют собой сита с большой сеткой, которые задерживают более крупные загрязнения. Кроме того, существуют мелкоячеистые сита, называемые фильтрами последнего шанса, для фильтрации масла непосредственно перед его прохождением из распылительных форсунок на поверхности подшипников. [Рис. 6] Эти фильтры расположены на каждом подшипнике и помогают отфильтровывать загрязнения, которые могут забить форсунку для распыления масла.
Клапан регулирования давления масла
Большинство масляных систем газотурбинных двигателей представляют собой систему регулирования давления, которая поддерживает постоянное давление. Клапан регулировки давления масла включен в масляную систему на стороне нагнетания нагнетательного насоса. Система регулирующих клапанов регулирует давление в системе до ограниченного давления внутри системы. Это больше регулирующий клапан, чем предохранительный клапан, потому что он поддерживает давление в системе в определенных пределах, кроме открытия только при превышении абсолютного максимального давления в системе.
Регулирующий клапан на рис. 7 имеет клапан, удерживаемый пружиной напротив седла. Регулируя натяжение (увеличение) пружины, вы изменяете давление, при котором клапан открывается, а также увеличиваете давление в системе. Винт, нажимающий на пружину, регулирует натяжение клапана и давление в системе.
Рис. 7. Клапан регулирования давления |
Клапан сброса давления масла
Некоторые большие турбореактивные масляные системы не имеют регулирующего клапана.Давление в системе зависит от оборотов двигателя и скорости насоса. В этой системе есть широкий диапазон давления. Предохранительный клапан используется для сброса давления только в том случае, если оно превышает максимальный предел для системы. [Рис. 8] Эта настоящая система предохранительного клапана предварительно настроена на сброс давления и перепуск масла обратно на впускную сторону масляного насоса всякий раз, когда давление превышает максимально установленный предел системы. Этот предохранительный клапан особенно важен, когда охладители масла включены в систему, поскольку охладители легко разрушаются из-за их тонкостенной конструкции.При нормальной работе он никогда не должен открываться.
Рисунок 8. Клапан сброса давления |
Масляные форсунки
Масляные форсунки (или форсунки) расположены в напорных линиях рядом или внутри подшипниковых отсеков и вала ротора. муфты. [Рис. 9] Масло из этих форсунок подается в виде распыленной струи. В некоторых двигателях используется распылитель воздушно-масляного тумана, который создается путем подачи отбираемого из компрессора воздуха под высоким давлением к выпускному отверстию масляного сопла.Этот метод считается подходящим для шариковых и роликовых подшипников; однако метод распыления твердого масла считается лучшим из двух.
Рис. 9. Масляные форсунки для распыления смазки на подшипники |
Масляные форсунки легко забиваются из-за небольшого отверстия в их наконечниках; следовательно, в масле не должно быть посторонних частиц. Если последние фильтры в масляных форсунках засоряются, это обычно приводит к поломке подшипников, поскольку форсунки недоступны для очистки, кроме как во время технического обслуживания двигателя.Чтобы предотвратить повреждение из-за засорения масляных форсунок, основные масляные фильтры часто проверяются на предмет загрязнения.
Контрольно-измерительные приборы системы смазки
В масляную систему включены положения для подключения манометра, которые определяют давление масла, количество масла, низкое давление масла, реле перепада давления масляного фильтра и температуру масла. Манометр масла измеряет давление смазочного материала, когда он выходит из насоса и попадает в систему давления. Соединение датчика давления масла находится в напорной линии между насосом и различными точками смазки.Электронный датчик размещен для отправки сигнала в блок управления Full Authority Digital Engine Control (FADEC) и через компьютеры системы индикации состояния двигателя и оповещения экипажа (EICAS), а также на дисплеи в кабине экипажа. [Рисунок 10] Информация передатчика количества в резервуаре отправляется на компьютеры EICAS. Реле низкого давления масла предупреждает экипаж, если давление масла падает ниже определенного значения во время работы двигателя. Реле дифференциального давления масла предупреждает летный экипаж о предстоящем перепуске масляного фильтра из-за его засорения.Сообщение отправляется на дисплей на верхнем дисплее EICAS в кабине экипажа, как показано на рисунке 10. Температуру масла можно определить в одной или нескольких точках на пути потока масла в двигателе. Сигнал отправляется на компьютер FADEC / EICAS и отображается на нижнем дисплее EICAS.
Рисунок 9. Масляные форсунки для смазки подшипников распылением |
Система смазки Системы сапуна (вентиляционные отверстия)
Подсистемы сапуна используются для удаления избыточного воздуха из полостей подшипников и возврата воздуха в масляный бак, где деаэратор отделяет его от любого масла, смешанного с паром воздуха и масла.Затем воздух выходит за борт и возвращается в атмосферу. Все отсеки подшипников двигателя, масляные баки и корпуса аксессуаров вентилируются вместе, поэтому давление в системе остается неизменным.
Вентиляционное отверстие в масляном баке не позволяет давлению внутри бака подниматься выше или ниже давления внешней атмосферы. Однако вентиляционное отверстие может быть направлено через обратный предохранительный клапан, который предварительно настроен на поддержание небольшого (приблизительно 4 фунта на квадратный дюйм) давления на масло для обеспечения положительного потока на впуск масляного насоса.
В ящике для аксессуаров вентиляционное отверстие (или сапун) представляет собой защищенное экраном отверстие, которое позволяет воздуху, накопившемуся в ящике для аксессуаров, выходить в атмосферу. Очищенное масло переносит воздух в ящик для принадлежностей, и этот воздух необходимо удалить. В противном случае повышение давления внутри корпуса для дополнительных принадлежностей остановило бы поток масла, вытекающий из подшипника, заставляя это масло проходить через сальники подшипника в корпус компрессора. Если в достаточном количестве, утечка масла может вызвать ожог и неисправность уплотнения и подшипника.Экранированные сапуны обычно расположены в передней центральной части корпуса аксессуаров, чтобы предотвратить утечку масла через сапун, когда самолет находится в необычном положении в полете. Некоторые сапуны могут иметь перегородку для предотвращения утечки масла во время маневров. В некоторых двигателях может использоваться вентиляционное отверстие, которое ведет непосредственно в отсек подшипников. Этот вентиль уравновешивает давление вокруг опорной поверхности, так что более низкое давление на первой ступени компрессора не заставляет масло проходить мимо заднего масляного уплотнения подшипника в компрессор.
Обратный клапан системы смазки
Обратные клапаны иногда устанавливаются в линиях подачи масла масляных систем с сухим картером, чтобы предотвратить просачивание масла из резервуара (самотеком) через элементы масляного насоса и линии высокого давления в двигатель после остановки. Обратные клапаны, останавливая поток в противоположном направлении, предотвращают скопление чрезмерного количества масла в вспомогательной коробке передач, задней части компрессора и камере сгорания. Такие скопления могут вызвать чрезмерную нагрузку на шестерни привода вспомогательных агрегатов во время запуска, загрязнение сжатого воздуха в кабине или возгорание масла внутри.Обратные клапаны обычно представляют собой подпружиненные шаровые краны, предназначенные для свободного протекания масла под давлением. Давление, необходимое для открытия этих клапанов, варьируется, но для клапанов обычно требуется от 2 до 5 фунтов на квадратный дюйм, чтобы масло могло течь к подшипникам.
Смазочная система Термостатические перепускные клапаны
Термостатические перепускные клапаны включены в масляные системы, использующие маслоохладитель. Хотя эти клапаны могут называться по-разному, их целью всегда является поддержание надлежащей температуры масла путем изменения доли общего потока масла, проходящего через маслоохладитель.Типичный термостатический байпасный клапан в разрезе показан на рисунке 11. Этот клапан состоит из корпуса клапана, имеющего два впускных отверстия и одно выпускное отверстие, а также подпружиненного клапана с термостатическим элементом. Клапан подпружинен, поскольку перепад давления в маслоохладителе может стать слишком большим из-за вмятин или засорения трубок охладителя. В этом случае клапан открывается, пропуская масло вокруг радиатора.
Рисунок 11.Типовой термостатический байпасный клапан |
Воздухоохладители масла
Обычно используются два основных типа охладителей масла: с воздушным охлаждением и с топливным охлаждением. Воздухоохладители масла используются в системах смазки некоторых газотурбинных двигателей для снижения температуры масла до степени, подходящей для рециркуляции через систему. Маслоохладитель с воздушным охлаждением обычно устанавливается в передней части двигателя. По конструкции и принципу действия он похож на охладитель с воздушным охлаждением, используемый в поршневых двигателях.Воздушный масляный радиатор обычно входит в масляную систему с сухим картером.
[Рис. 12] Этот охладитель может иметь воздушное или топливное охлаждение, и во многих двигателях используется и то, и другое. Системы смазки с сухим картером нуждаются в охладителях по нескольким причинам. Во-первых, воздушного охлаждения подшипников с помощью отбираемого из компрессора воздуха недостаточно для охлаждения полостей подшипников турбины из-за тепла, присутствующего в области подшипников турбины.